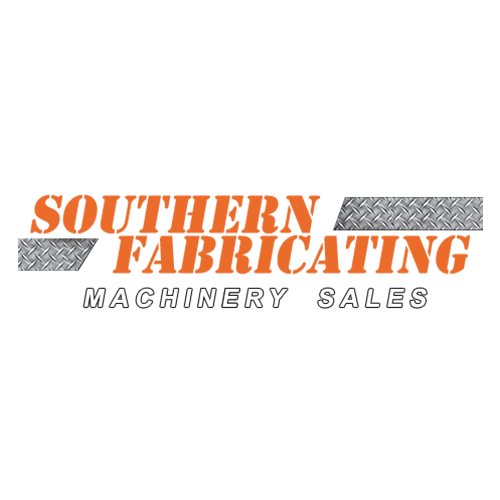
Posted By: Southern Fabricating Machinery Sales | Posted On: August 28, 2020
The 3 Types of Bending in Press Brakes
Press brake bending requires different methods of approach to achieve the desired results needed. From forming wind tower poles to intricate electrical cabinet components, press brakes are a vital tool for the fabricator and knowing that not all bending is the same is a key to the successful operation of them. Understanding the process, the tooling and the material (as all metals being bent will respond differently to each bending process) is vital to gaining accurate parts quickly and repeatedly.
As we have covered Basic Operation and Tooling in previous articles we will focus here on the different types of bending in press brakes where each one has its own purpose and benefits.
How Does a Press Brake Work?
To cover the basics a press brake has a Ram fitted with a punch that forces the material being worked into a die. The material is then formed into an angle corresponding to the angle of the die or the depth the punch forces it into the die. Press Brakes can be powered by Mechanical methods (Large Flywheel Turning a Crankshaft), Hydraulic Methods, Electric Methods or a combination of these processes. Press Brakes can also be operated by manual or CNC Controls.
Manual press brakes would be setup by hand with each individual piece of sheet metal being bent to the shape needed on angle at a time. With CNC press brakes, the machine can be pre-programmed to bend the sheet metal through many various bends completing one part at a time vs only one angle. Regardless of the type of bending machine, press brakes all use a V blade (called a punch) to push on the sheet metal with enough pressure against a die to cause it to bend. These machines can bend sheet metal work from just a few inches to some that are many feet long.
Whether the press moves up or down, both of these methods will produce the same sheet metal components and there are no restrictions on the design of your component to suit either machine.
Understanding the 3 Types of Bending in Press Brakes
There are three types of bending with press brakes that are commonly used. Coining (sometimes incorrectly referred to as Bottom Bending), Bottom Bending and Air-Bending with each requiring different strategies in tooling and press brake operation. Discovering how these bending processes work will best help you the fabricator, understand which method is best for your application.
Coining
The term comes from the process of pressing coins. In order to get the images, numbers, and lettering on a coin, there needs to be a great deal of force used to indent the metal. Here, the entire piece is put under the full tonnage of the press brake. This method requires each bend to be exactly the same, regardless of how many pieces are being made. The method actually pushes the material into the bottom of the V-Die and then crushes it an additional 10-15% securely “locking” in the angle of the die itself. The coining method requires the largest amount of tonnage in a press brake, usually 3X to 5X that of the other bending methods.
Bottom Bending
This process doesn’t require as much tonnage as the coining method but does require more tonnage then the air-bending method. Here, the metal is pushed down into the V-Die to make a bend. Because it doesn’t use as much pressure, there is a slight spring back. Bottom Bending is common practice on mechanical press brakes as the accuracy is again obtained from the tool set and not necessarily the positioning accuracy of the press brake.
Air Bending
Air Bending is the most common form of press brake forming we see today for a combination of reasons. First it requires far less tonnage to achieve, second a simple 85° Die can achieve multiple angles and lastly less tooling is required making the overall investment costs much cheaper in the long run. There also is even less contact made with the material being formed.
Air bending works by forcing the material only far enough into the die to achieve the desired angle plus a little bit more to compensate for the material springback. Again, different bend angles can be done using the same set of tools which is a highly financially beneficial benefit. The thickness of the sheet metal, its ductility, hardness and springback will determine the angle of the punch and die. This method allows for more accuracy because of its flexibility but requires an accurately positioned machine and accurately ground tooling to achieve success easily.
How to Determine Which Type of Bending to use for Your Project
Each method has its uses. What type you use will largely depend on what you are making and the tools available to you to make them with. Also the size and type of the metal you are required to bend and of course that material’s properties (ductility, springback etc). If you have a machine that is flexible and can handle more than one type, then your choices are more open. If you are using a mechanical press brake then your options are fairly limited.
Ready to Purchase New Press Brakes? SFMS is Here to Help!
Whether you need a new or used press brake, check out our inventory. Our sales staff are very knowledgeable when it comes to fabrication machinery and the press brake forming process. We can guide you through the process of coining, bottom and air-bending so that you can fully understand the benefits of each of these methods.
We also buy, sell, trade, broker, and finance equipment that you need or need to trade. Southern Fabricating Machinery Sales mission is to be equipment and application experts, providing best in class solutions for our customers and partners.
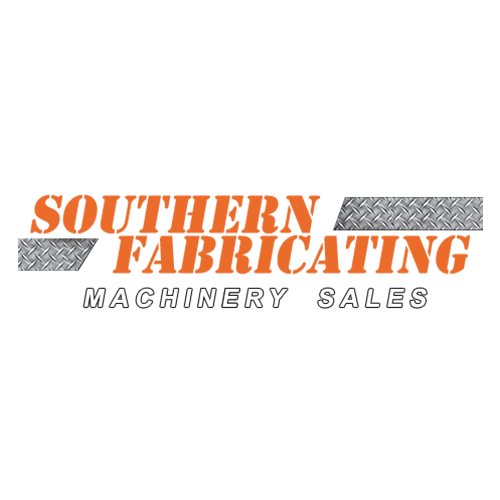