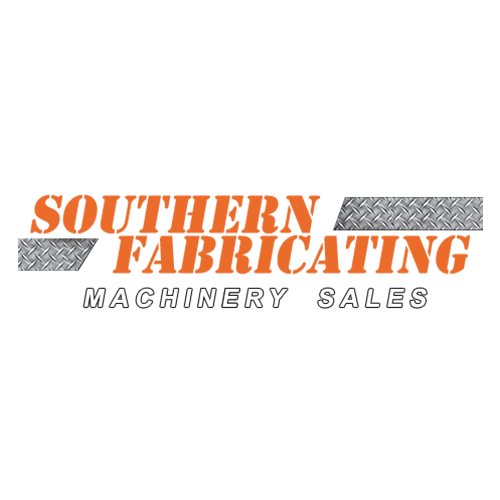
Posted By: Southern Fabricating Machinery Sales | Posted On: September 16, 2020
Why Selecting the Right Press Brake Tooling is as Important as Selecting the Right Press Brake
If you are bending or shaping metal, press brake tooling plays a very important role. Press brake tooling includes dies and punches used with a press brake to form, bend or flatten sheet metal. They are used with a press brake to shape or bend metal. Usually made of steel themselves, they are what actually touches the metal to be bent and by utilizing a tool set of opposing features, force the material to conform to the bend desired.
How Press Brakes Work
A press brake is actually a bending machine. It bends a piece of sheet metal in specific areas by holding the workpiece between a matching punch and die. While most press brakes are computer programmed, they also come in basic NC and manually operated machines.
A press brakes tool set has two main parts. The top tool mounted in the ram is called the ‘punch.’ The bottom tool mounted on the bed or ‘die rail’ is called the ‘Die’. The force driving the punch into the die is a mechanism pushing the ram and can be mechanically, hydraulically or electrically (servo motor) driven. While the basic operation of all press brakes is the same, the mechanism used to exert the force on the ram that shapes the part is different.
Older style press brakes used an electric motor to drive a flywheel that when engaged by a clutch mechanism presses the ram down. These are called mechanical presses due to their mechanical design. For projects that need more controllability (most today), hydraulic presses use two paired hydraulic cylinders on either side of the press’s ram. These are safer to operate and are easily programmed to keep the ram parallel or slightly offset to compensate for worn tooling or varying degrees of bend angle.
Why Press Brake Tooling is Important
The type of tooling used for fabrication of your metal parts will determine how efficient or not that operation will be. Tooling both enables and limits production. If you make something unique you will almost always need special tooling. Otherwise most tool sets are available in a standard variety of configurations that can be assembled to any length your bending application requires.
Tooling and the brake’s interaction with tooling, is expanding equipment capabilities and making single-part bending much more affordable. The type of tooling you need will be different depending on the project you are working on but it’s highly recommended that you look at precision ground press brake tooling for the best results.
Features to Consider When Choosing Press Brake Tooling
When you are in the market for buying press brake tooling, there are a few things to consider.
What Are You Making
This will come down to the type of metal you are using. Different thicknesses will need different tools as the die opening, angle and punch radius will change. You also need to factor in the length of the sheet metal you are working with to determine how much tooling you need.
Also the Tensile Strength and Yield Strength of the metals come into play greatly as ¼” Aluminum is much easier to bend then ¼” carbon steel. Carbon steel, Stainless Steels, Aluminum, and mild steel sheet metals all have a different bending force and may require tooling adjustments to bend them correctly.
Angle
The angle you are forming also has a lot to do with choosing the right tooling. If you need to use a press brake with the lower than recommended tonnage, you will need to match it with a toolset with an increased die opening that will lower the tonnage required to form your material. Although there are 3 types of bending on a press brake, Air bending will also give you a longer life to the press brake without compromising quality as long as you again, use the right tool set.
Top and Bottom
Top tools are called punches and work together to make each product they also work differently with different bottom tolls, or dies. Top tooling comes in a wide variety of shapes and sizes. The correct punch you need will depend on the job at hand. There is a large range available, but they can be generally classified into these unique types, Standard Punch, Goose Neck Punch, Swan Neck Punch, and Acute Angle Punch.
Bottom Tools
Dies are the bottom tools and they are also available in different sizes and shapes to match the punch tooling and material thickness you are forming. From single Vee designs, Offset Tools, Flattening Dies and U bend and Z bend variants. Which you choose will depend on your fabrication needs and the parameters of your Press Brake.
New and Used
Whether you have a press brake already and need help selecting the right tooling or need to select the right press brake and tooling package, Southern Fabricating Machinery Sales team of experts can help. Our technical expertise matched with our large selection of used and new options in press brakes makes us the best stop for your metal bending needs.
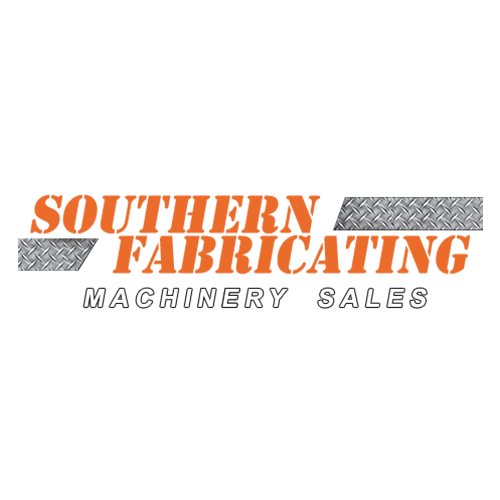