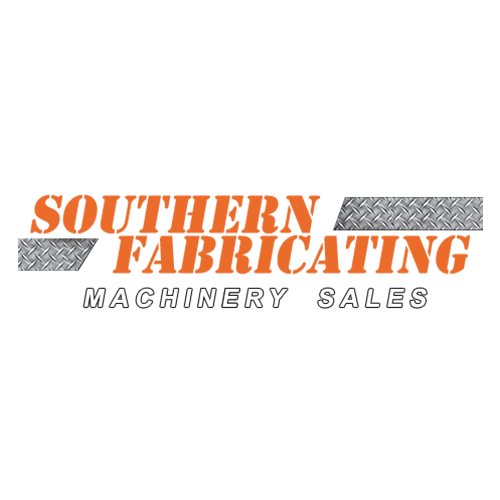
Posted By: Southern Fabricating Machinery Sales | Posted On: February 24, 2020
Press Brake Bending: Why You're Doing It All Wrong
As a machinery dealer offering a variety of used equipment, we are often asked about equipment to meet a specific budget a buyer has in mind, while rarely being asked about a buyer's potential application. While budgets are important, buying the right machine that will make your shop more productive and profitable ought to rank even higher on the scale of importance. You can buy the right machine 1 time but you can have the wrong machine on your floor every day for the next 10 years costing you money and frustration.
How Press Brake Bending Works
Before you can choose the right machine you should understand the basics of what a press brake is and how it works. Although you may know a little about forming on a press brake, quick review could never hurt.
- Press Brakes ARE NOT designated by material capacity (i.e. ¼” X 10’ brake). Although we hear this verbiage daily, it is simply wrong (although there were press brake manufacturers that rated their machines by bending capacity to sell to an unknowledgeable buyer). Press Brakes, in fact, are rated by Tonnage and it is that Tonnage applied over a specific Punch, Die, Material Type, Material Thickness and Material Length that determine WHAT a press brake can form.
- A Press Brake is made up of at least 1 important axis, The Ram (Y-Axis) moving Up/Down (or some machines are designed to move the bed up/down adversely). The positioning of the ram determines the ANGLE of the part being formed. The more accurately the ram can position and reposition the more accurately you theoretically (remember material plays a big part too) can form. A second, almost as critical axis is the Backgage (X) axis. The backgage provides the accuracy in length of the flange being formed (the lip being bent up).
- A press brake works by taking a punch under force and pressing the plate material into the curvature of the die. The deeper the punch pushes the material into the die, the greater the angle of the bend up to the angle of the die itself minus slight springback in the material.
- Multiple Axis added to a press brake can make more complex bending applications easy. Axis like R-Axis (backgauge gauge fingers moving up and down), Z-Axis (back gauge fingers moving side-side) and CNC Crowning are the most common additional press brake axis.
Common Press Brake Bending Mistakes
Some of the more common press brake bending mistakes can be caused by part design or by operation. Consider these common issues when designing parts for forming.
- Placing holes, slots, notches or any other features too close to bend radius.
- By placing cutouts too close to the forming edge the natural tendency is to stretch the opening where a once cleanly round cut hole becomes and oblong after forming. Design your part or manufacturing method to avoid cutouts close to the forming edges prior to the forming process.
- Requiring a flange that is too narrow.
- A press brake needs the material to remain completely across the surface of the die during the entire bending process in order for the bend and flange length to be accurate. If a flange is too short it may drop into the die during the forming operation causing a misalignment during forming. Short flanges that are required may be formed and then trimmed to size or formed over smaller V-Dies or special tooling if the press brake tonnage allows.
- Choosing a bend radius that is too tight for the material.
- If the bend radius you are using is too tight for the material being formed, extreme stress will occur at the radius. This usually results in the material fracturing at the point of forming.
- Forming offsets (jogs) too close to one another.
- Offset bends, common in making boxes, are by nature 2 bends that are close together these usually require a special offset punch and die combination to form but bends in the same operation but note, your press brake must have the available tonnage to use these double form, and thus, double tonnage tools.
Press Brake Bending Tips
Some of the best press brake bending tips are located in an article we wrote titled: How to Avoid The Top 4 Press Brake Bending Problems. In that article we described the best practices to avoid common forming problems. We also posted another article covering the 4 Press Brake Bending Basics You Need to Know. Together these can provide many press brake bending tips and strategies to ensure your successfully forming parts in your shop. Having the right press brake in the first place goes a long way to ensuring your doing it right when forming fabricated parts. Equipping that machine with the right Number of Axis, Options and Accessories is next in the importance for success.
If you are interested in more articles like this, please check out our Blog on Press Brakes Linked Here and sign up to be notified when these, or other articles are released. If you are in the market for or budgeting for a press brake CLICK HERE to visit our available press brakes pages. If you would like to submit articles for consideration or submit corrections please contact us HERE or by calling us directly at 813-444-4555 or via the web at www.southernfabsales.com
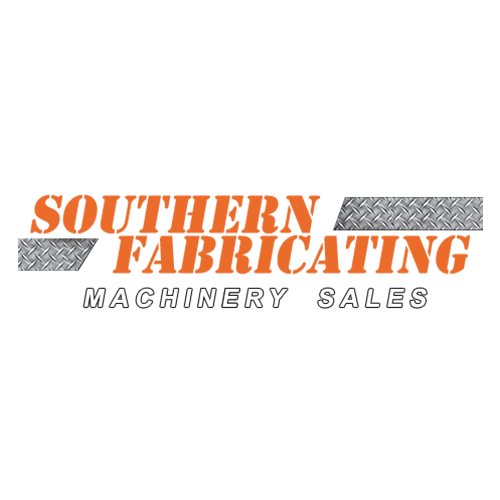