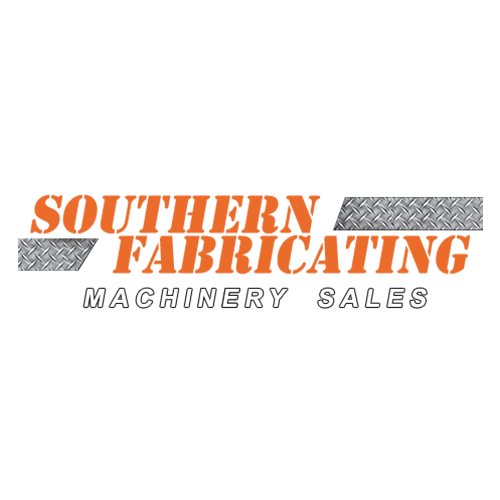
Posted By: Southern Fabricating Machinery Sales | Posted On: March 16, 2020
The Value of Using Precision Press Brake Tooling
A while back we published the article: The 4 Critical Things Every Press Brake Operator Should Know to point out the basic important items when operating a press brake In that article we discussed briefly the importance of press brake tooling but didn’t delve deep enough into what type of tooling is available, what makes it different and what matters most to you the press brake operator or fabrication shop owner. In this article we will discuss further what makes tooling so important to your new or new to you press brake and why used tooling could be the worst, yes worst thing you could put on it.
When purchasing a press brake consider first the type of tooling you will be using. We are not referring to planed, soft or hardened tooling, we are referring to the tool holder style as there are several types to choose from and for a variety of reasons you may choose each one. All of these tooling styles refer to how the tool (or punch) is held in the ram of the press brake. Some styles are quicker and easier to change whereas others are far more repeatable and accurate when changing tooling.
Press Brake Tooling Styles
- American Style: American Style tooling is by far the most common style in North America and although declining in popularity it is used on about 70% of the press brakes on the market today. American Style Press Brake Tooling is cheap to buy and easy to source making it a popular choice however it is the least accurate of all the tool holder styles when changing out tooling. It has a smaller reference and clamping surface (0.5” X 0.63”) to gauge the tool against. This tooling style is available in simple planed tooling to precision ground tooling
- European Style: European style press brake tooling offers a much larger and more generous surface area to clamp the tool to. This larger surface area provides for better locating and repeatability of the tool. European Tooling also puts the center of the ram in line with the cent of the punch thus avoiding any potential offset load.
- Wila /Trumpf/New Standard Style: The Wila/Trumpf Style or New Standard style press brake tooling takes the best of the European design, the larger clamping and locating surfaces and incorporates features that make it ideal for quick changes while repeating the accuracy that the tooling is known for.
%201995%20Amada%20RG-80%20CNC%20Hydraulic%20Press%20Brake/Wila%20New%20Standard%20Tooling.jpg?width=300&name=Wila%20New%20Standard%20Tooling.jpg)
What is Precision Press Brake Tooling?
Each of the above mentioned press brake tooling styles are available as “precision tooling” or standard cold planed tooling. The difference is Standard Cold Planed Press Brake tooling is manufactured on a planer, or planer mill (another type of shaper) by shaping the surfaces in. The material is soft and although it can be flame hardened to provide a wear resistant surface. Accuracy is poor at only about 0.0015” p/foot at the best considering today's press brake technology and capability for repeatability (typically in the 0.0004” range)..
Advantages Cold Planed Tooling
- Cost, cold planed press brake tooling is much cheaper
- Segmented as needed; Cold planed press brake tooling can be cut as needed
Disadvantages of Cold Planed Tooling
- Forming surfaces are soft (in the 32-34Rc range) and thus prone to denting or deforming
- Once segmented tools won't line up accurately
- Inaccuracy over the full length of the brake.
So what makes Press brake tooling “Precision” and why do you need it?
The precision in tooling comes from two things. The first being how the tool is manufactured and the repeatability and accuracy of the tool when it is mounted repeatedly in the press brake. Ideally you would like the tool tip to repeat its position as accurately as possible in the press brakes ram each and every time it is loaded thus assuring your bending depths are the same with each setup. The second is how the tool is made.
Like the above mentions cold planed press brake tools, precision press brake tooling takes it a few steps further by then being heat treated so that not only the wear surfaces but the gauging surfaces are hardened against wear and repeated use. Hardened upwards of 56-58 Rc, these tools provide for the best wear resistance and the longest useful life. Secondly the tool is then ground to precision providing for a linear accuracy approximately 10X better than cold planed tooling alone Often down to ±0.0005” in profile accuracy and in height. Lastly the tools are all pre-segmented and available in a variety of widths to accommodate a combination for any sizes when box forming.
Advantages Precision Press Brake Tooling
- Tooling life is 3-5X that of cold planed press brake tooling
- Repeatability is 10X better
- Replacing Damaged segments is cheaper than replacing cold planned full length tools
Disadvantage of Precision Press Brake Tooling
- Cost
Uses of Precision Press Brake Tooling
Many shops have a variety of press brake tooling in their shop which include a mixture of precision tools and standard tools. Often when custom one-off tools are needed they are purchased in a standard tool style as the precision style is simply too cost prohibitive for a simple application. However that is where the standard “cheaper” tooling advantage ends as the repeatability in tooling changeouts, speed in setup and repeatability ion parts far outweighs the precision tooling costs. Precision tooling is further enhanced by automatic hydraulic clamping systems which make tooling changeout quick and easy with just the push of a button while automatically clamping AND seating the tool eliminating the need to bottom the punch out in the die to remove any gap between the punch and the ram.
Press Brake Tips
There are many press brake tips that you can start using right now without adding a new machine or precision press brake tooling. Many of these tips can be found right HERE In our extensive technical articles on press brakes and bending. However the basic ones are:
- Know your material - Materials form differently due to hardness, springback etc.
- Know your machine - You may have to bottom-bend if your press brake ram is not repeatable enough for accurate parts.
- Know your tooling - The easiest way to eliminate press brake forming issues is to eliminate the most likely culprit, worn, damaged or inaccurate tooling.
In summary your press brake is a powerful and flexible machine that should allow for years of fabricating performance if quality tools are used. You can avoid setup frustration by using quality precision press brake tooling from the start.
Now Earlier in this article we said that ‘used tooling could be the worst, yes worst thing you could put on your new machine’ and we meant it. Imagine your newly purchased press brake as a high performance race car. It has the specifications and speed you need to win the race in fabricating accurate repeatable parts. Now imagine throwing old used worn out tires on that race car and heading to the track to compete. Those tires are the old worn out tools your shop likely has been using for years. Don't restrict your new machines performance with old worn out technology. Go the distance and tool it up right!
If you enjoyed this article on Precision Press Brake Tooling you can find more just like it HERE IN OUR BLOG SECTION on press brakes. There you can also sign up by entering your email and receive these articles when published. If you have questions, comments or corrections you can reach us at the CONTACT US section on our website. If your shopping for a press brake just click on the links below for available press brakes AND our press brake inspection form and remember you can call us anytime for help with your bending application at 1-813-444-4555
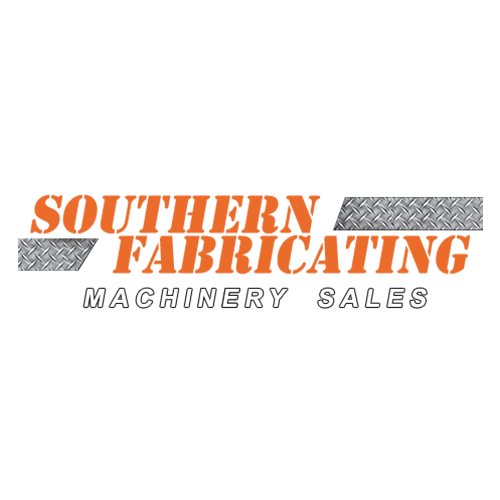