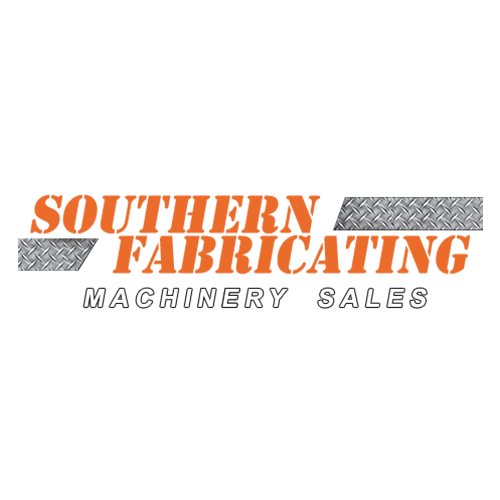
Posted By: Southern Fabricating Machinery Sales | Posted On: January 17, 2020
Press Brake Operation Basics
The science of press brake operation sounds like something out of a technical manual. All across the country, there are welding and fabricating companies bragging about their capabilities. An exceptional metal fabrication company can be accurately identified by the standard of work that they produce day-in and day-out. This is especially true for press brake operation. A press brake is a machine pressing tool for bending sheet and plate material, most commonly sheet metal. It forms predetermined bends by clamping the workpiece between a matching punch and die.
Brake forming is one of the oldest mechanical metal deformation processes. They may have been used for many years, they’re a vital piece of equipment in any fabrication shop. If you’ve never heard of it before, it’s easy to get confused and overwhelmed. Here’s a simple explanation of how they work.
How Press Brakes Work
Typically, two C-frames form the sides of the press brake (also called side-frames), connected to a table at the bottom and on a movable beam at the top. The bottom tool, or die, is mounted on the table, with the top tool, or punch, mounted on the upper beam.
“Brake forming can commonly form metals up to 10" thick and some machinery will form pieces as long as 20 feet,” according to Advantage Fabricated Metals.
By controlling the depth of the punch’s motion the bend angle can also be precisely controlled. Press brakes can be manual machines but are more and more likely to have a CNC Controller on them allowing for complex bending operations with ease.
Parts of a Press Brake Machine
There are various parts that make up a press brake machine. The frame of the press brake is welded by the left and right upright plates (or sideframes), worktable (or bed), and vertical moving ram. The ram is made from the whole steel plate and is connected to the hydraulic piston rods the left and right hydraulic oil cylinder (often referred to as Y1 & Y2). The ram uses the hydraulic forces to move it and the upper tool (punch) along a gibbed way system and either a mechanical stop for fine adjustment or the more accurate electronic scale feedback method that provide exact positioning and thus accurate angles of bend.
Some systems are equipped with a mechanical synchronization system consisting of torsion, swing arm, joint bearings, and more. It has a simple structure, stable and reliable performance through machine stiffness, as well as high precision synchronization.
The material being bent upwards is called the “Flange” and it is measured and controlled for accuracy through a device on the press brake mounted in the rear of the machine called the “backgauge”. The backgauge of the CNC press brake utilizes a motor driven gearbox or chain driven gaging system, to output a synchronous movement of two ball or lead screws which in turn move the gaging bar in and out to the exact position required. The position of the backgage is critical as it gages the length of every flange being formed and as such is controlled by the CNC controller. Through a program input by the operator, it controls the position of itself and the attached material stops, called “fingers” on the gage bar itself.
Press Brake Metal Forming Tips
The most important press brake bending tip you can follow is to be aware of the material grade you are forming. The harder the grade, the more springback you should expect. If you use softer material, you will experience far less springback as that material conforms much easier to the angle of the die it is being forced into.
It's also critical to watch out for cracking or spreading, especially with sharp bends. Bottoming out (or bottom bending) can make the material even more prone to fracturing but provide an exact bend through the process of "coining". However, the nearer you can get to a 1-1 radius between the material thickness and the inside bend, the less likely you’ll see cracking on the outside of the bend.
A final press brake metal forming tip is to not compensate for springback by bottom bending but rather by using the appropriate tooling. However when you’re bottom bending, you need to work with the 88-degree punch. Using an 85-degree punch will extend the bend too much, which means you won’t be able to achieve enough spring forward to get the bend back to a 90-degree angle.
At Southern Fabricating Machinery Sales, Inc. we are experts in press brake bending and machine operation and maintenance. We can assist you with selecting the right press brake, tooling and accessories for your needs and budget. Call us today at 1-813-444-4555 or visit us on the web at www.southernfabsales.com
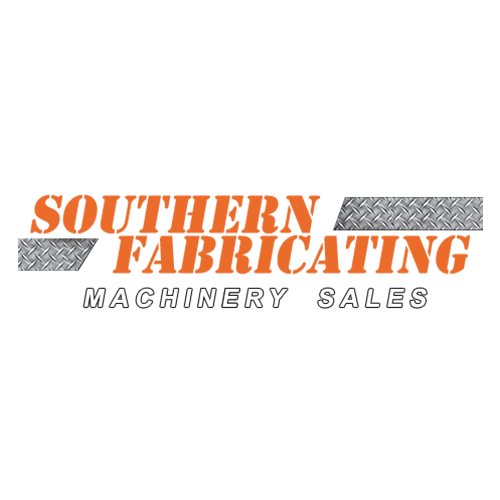