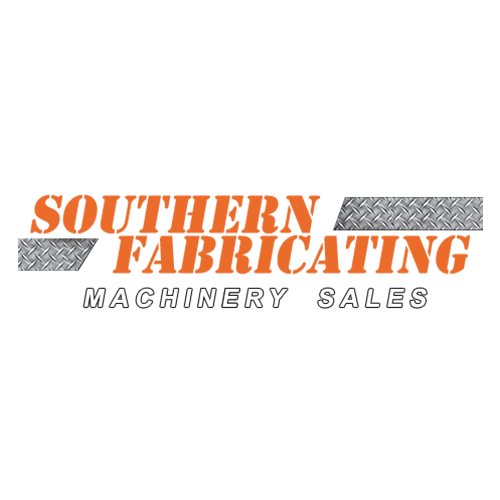
Posted By: Southern Fabricating Machinery Sales | Posted On: July 26, 2018
What You Need to Know About Press Brake Forming Technology
Press brakes are a key piece of metal forming equipment in many manufacturing machine shops. These devices apply tons of force to shape solid metal objects. The most common application is to bend sheet metal at a specific angle.
Over the years, press brake forming technology has undergone many changes. This can make it a bit difficult to generalize about these manufacturing machines. When you’re on the market for a new (or used) press brake machine, it’s important to have a solid grasp of how these machines work, and how they may vary from one model to the next.
To help you out with this, here is a list of a few of the basic things that everyone should know about press brake forming technology:
1) There Are Four Different Ways Press Brakes Apply Force
When you’re looking at a press brake, it’s important to know what kind of press brake you’re dealing with. Different machines will apply force to an object in different ways—meaning that they have different mechanisms which will require different maintenance methods.
Based on how they apply force to an object, there are four distinct kinds of press brakes:
- Mechanical. The oldest type of press brake technology. This variant would use a flywheel powered by an electric motor to supply the force for bending materials. Fast and accurate, but was largely supplanted by hydraulic presses because, as noted by The Fabricator, “precision work will take a craftsman, extra setup pieces, and a lot of production time.”
- Pneumatic. These press brakes utilize air pressure to move their rams up and down. These machines are similar to hydraulic presses, but they usually have a much lower tonnage limit.
- Hydraulic. Hydraulic fluids contained in one or more cylinders are used to force the ram of the press brake down onto the workpiece being shaped—though some models move the bed up instead. Hydraulic controls are generally more accurate than mechanical ones and can be adjusted for individual bend depths.
- Servo-Electric. Servo-electric press brakes use an electric motor to drive the motion of the ram. While very fast and efficient compared to other press brake technologies, they are limited to low-tonnage work. One benefit of these machines, as noted in another Fabricator article, is that “Having no hydraulic oil or associated seals simplifies maintenance.”
Most of the time, when talking about press brakes, people are generally thinking about either the mechanical or the hydraulic drive systems, as these are the most commonly known. The decision on which type of press brake you should use will depend on your application—if you have a lot of forming to do that doesn’t require high tonnages, a servo-electric machine might work for you. If you need to bend very thick pieces of steel, a hydraulic machine might be better.
2) Parts of a Press Brake
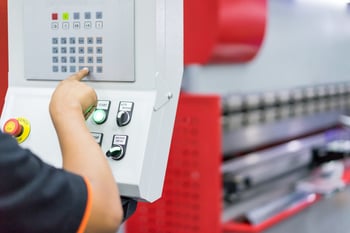
The components of a press brake can vary from one machine to the next depending on what type of drive system it uses.
The basic structure of a press brake will typically include:
- A bed to rest the workpiece on;
- A ram to push down on the piece (or for the piece to be pushed up into);
- Dies for the brake’s bed to aid in shaping metal;
- A backgauge to help ensure the bend is in the right spot; and
- A CNC (computer numerical control) system—some older machines may not have this, but it is very common for press brakes made in the last couple of decades.
The biggest difference between machines is usually the drive system used to move the ram. Another difference between machines can include the different axes of control that the machine may have.
3) Axes of Control
A press brake can have numerous control axes depending on the model. When looking at a press brake, be sure to check which of the following control axes it has:
- Y Axis. The standard up/down motion every press brake should have. This is the typical control axis for a single cylinder hydraulic and most mechanical brakes.
- Y1/Y2 Axis. A machine with a Y1/Y2 axis designation can control up and down motion for either side of the machine—sometimes allowing it to compensate for worn tooling.
- X Axis. This typically refers to the machine’s backgage or motion stop that is used to keep a part in place for a bend. Allows the backgage to move forward and back as needed.
- X1/X2 Axis. Some brakes may have different “fingers” to act as backgages that are independently controllable—typically useful for complex part flanging.
- R Axis. Refers to a backgage that can be moved up and down. Useful for forming parts with downward-formed flanges.
- R1/R2 Axis. If a backgage consisting of multiple “fingers” has up/down motion, this is how that will be marked.
- Z Axis. Marks a backgage that can move left and right in addition to other movement axes.
- Z1/Z2 Axis. If individual fingers can move left/right, this is how that movement is labeled.
- CNC Crowning. A machine with a CNC system can control or “pre-bend” the bed of the machine to correct for worn tooling or flexing of the press brake.
- Sheet Lifters. Additional mechanical support for holding large, heavy sheets of metal in place during the down stroke of the press brake’s ram. This lets a single person operate the press brake when bending large or heavy pieces of sheet metal.
- Robotic Interfaces. Robotic loading, operation, and unloading systems for a press brake that may allow it to operate almost completely unattended in some circumstances.
The specific axes of control that you’ll want in your press brake will vary depending on just how complicated the parts you’re making are. If you have a lot of highly-complicated parts that you need to make, having extra axes of control—such as the X, Z, and R axes—will be more important than if you just need to make simpler bends that only require the Y axis of motion to pull off.
4) Types of Bending Operations
Generally speaking, there are two types of bending operations performed on a press brake: air bending and bottoming.
Bottoming operations basically force the material being bent all the way to the bottom of the die—ensuring that it conforms precisely to the die’s shape. In a way, this could be considered a type of coining operation.
The advantage of bottoming is that a brake doesn’t have to be very precise to get accurate bends here—the accuracy of the bend is entirely dependent on the shape of the die. However, this also requires much greater force than air bending does (usually about three to four times as much force), so it’s usually only an option for higher-tonnage press brakes.
Air bending simply pushes the material being bent just far enough into the die that it achieves the desired shape and angle (while accounting for potential “spring back” once the pressure is released). The material is never pressed to the bottom of the die, leaving a small pocket of air there (hence the name “air bending”).
Here, the die only needs to change if the material’s thickness changes significantly. Also, this usually requires much less force than bottoming, so it can work with lower-capacity presses. However, this does require much more precision than bottoming—but the widespread availability of CNC systems makes controlling air bending simple for most machine shops.
5) Pits or No Pits for Your Press Brake?
Bigger press brakes with larger beds and heavier tonnages may require a pit when you put them into your machine shop. This is because as the tonnage or overall size of a press brake increases, the bed has to be made bigger, which raises its height—making it harder to operate.
Building a pit allows you to sink the press brake a bit, putting the bed at a height that is more comfortable (and safe) for your employees to work with.
So, when inspecting a press brake, be sure to double-check the height of the bed and be ready to prepare a pit in your machine shop for that press brake. This will require a lot of work and care, but it’s a necessity for maximizing quality and safety with larger brakes.
If you have any questions about how to find the right press brake for your machine shop, be sure to contact the SFMS team for more information. We’ll go over your machine shop’s requirements to help you find the right machine for your needs. Or, check out some of the used machinery we have for sale right now.
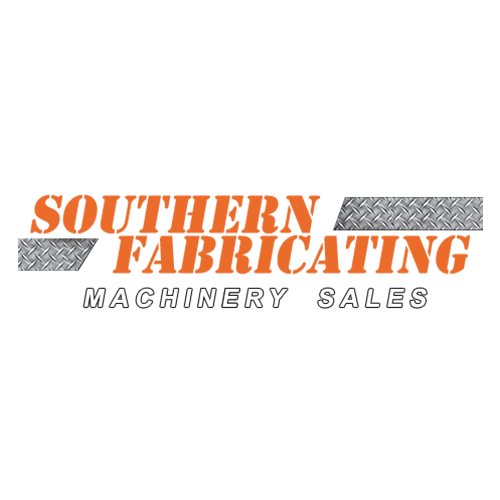