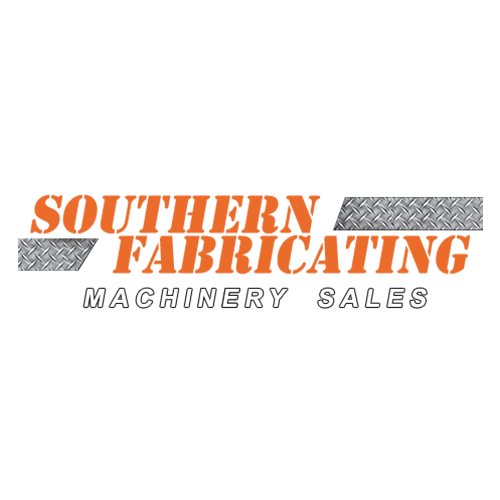
Posted By: Southern Fabricating Machinery Sales | Posted On: October 16, 2018
Everything You Need to Know About Waterjet Accuracy for Precision Cutting
In many machine shops, the accuracy of a process can be vital for ensuring the functionality of a completed part or product. For example, manufacturers supplying aerospace companies often have to meet parts tolerances as precise as +/- 0.005” to avoid creating a fatal flaw in an aircraft. If such tolerances aren’t met, then the part will have to be rejected—and, if a manufacturer can’t meet part tolerances consistently, then their clients will have to look elsewhere for their high-precision parts.
So, to retain customers and grow revenues, many machine shops have to find the most accurate methods for cutting and shaping parts. With this in mind, many machine shops take a look at numerous cutting processes, such as lasers, CNC punches, plasma torches, and waterjet cutting.
How accurate is water jet cutting? And, what affects waterjet cutting accuracy? Here’s what you need to know about waterjet accuracy for manufacturing shops.
What is the Base Accuracy of the Waterjet Cutting Process?
Relatively speaking, a water jet cutting process is highly accurate. Once the cutting starts (meaning that the initial through hole is complete), a waterjet cutting machine can achieve a parts tolerance of +/- 0.001” with consistency. This makes the waterjet cutting process highly desirable for cutting precision parts. However, there are a few different factors that can affect the accuracy of a cut made with a waterjet machine.
Workpiece Thickness and Waterjet Accuracy
The thicker a workpiece is, the harder it will be to cut accurately with a waterjet cutting machine. For materials thicker than an inch, it is common for the waterjet’s cutting accuracy to drop to 0.1”—a major decrease. Part of the reason for this is that for the waterjet to start cutting accurately, a hole first needs to be drilled into the workpiece.
The initial hole made by a waterjet cutting machine is often somewhat irregular. The thicker the workpiece, the more irregular the hole will be because of the extra work involved in making that initial cut. Once cut through, however, the rest of the cutting line should be incredibly accurate. Some manufacturers may notice a small warp in a workpiece near where the cut began and ended because of this, with the rest of the cut being virtually perfect.
One idea for improving waterjet cutting accuracy on thicker workpieces is to pre-drill pilot holes into the workpiece with electric discharge machining (EDM) or other cutting methods, then switch over to waterjet cutting. However, this increases production complexity, and it may be better to use a different cutting process such as laser cutting or CNC punching—unless the type of cut needed demands a minimal heat affected zone (HAZ) or if the cut would be impossible to do with a CNC punch.
Controls and Part Accuracy in Waterjet Cutting
The control system for the waterjet cutting machine plays a major part in determining the machine’s cutting accuracy. A more precise controller will, naturally, result in more precise and regular cuts. However, with the wide range of manufacturers and issues of machine maintenance affecting controller accuracy, it can be hard to generalize about the accuracy of specific controllers.
Some waterjet cutting machines feature a fifth axis of motion to allow the machine to make angled cuts in various workpieces. This can greatly expand the complexity of parts that can be made with a waterjet cutting process.
Waterjet Cutting and Parts Tolerances
One factor that is easy to forget about when considering the accuracy of a waterjet cutting machine compared to other high-precision cutting methods (such as laser cutting) is the generation of heat in the cutting process. Lasers are an oft-considered alternative to waterjet cutting because of their ultra-precise cutting methods and ability to leave a smooth edge.
However, unlike waterjet cutting, lasers transfer enormous amounts of heat into a workpiece as they cut it. This results in a large HAZ that extends out from the site of the cut—potentially affecting the physical properties of the workpiece as if it was being heat treated. This could have an adverse effect on the final product.
Because waterjet cutting doesn’t transfer nearly as much thermal energy, it is ideal for avoiding issues related to HAZ. If such issues are a concern for ensuring that the workpiece meets its parts tolerances, then waterjet cutting would be an ideal parts cutting solution.
Waterjet Cutting Accuracy and Etching/Partial Cutting
One weakness of waterjet cutting compared to EDM cutting or CNC punching is that it is not very accurate at making cuts to a specific depth. To achieve the best possible accuracy, the waterjet cutting machine needs to cut all the way through a workpiece. Also, it can be hard to control the timing of a waterjet cutting machine’s motion to achieve a consistent depth in an engraving.
For these types of processes, EDM or CNC punches are generally more consistent and efficient.
Overall, waterjet cutting machines are an incredibly useful and versatile machine tool for cutting parts with a great deal of accuracy. With the proper maintenance for its critical components, abrasive waterjet cutting machines will provide an incredibly accurate cut in almost any material.
Need help finding the right waterjet cutting machine for your shop floor? Contact the experts at SFMS—we have years of experience in pairing machine shops with the right manufacturing tools for their needs, and an extensive network of contacts who might have the perfect machine for your shop floor!
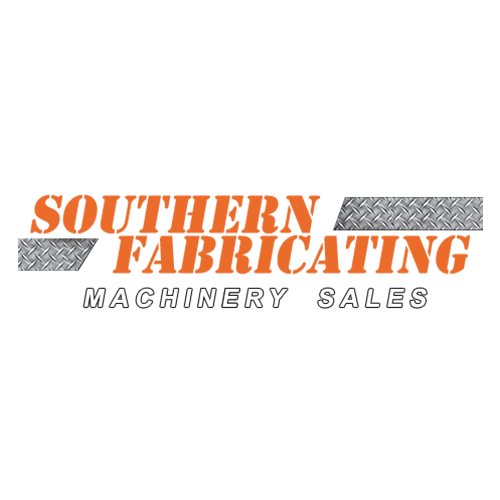