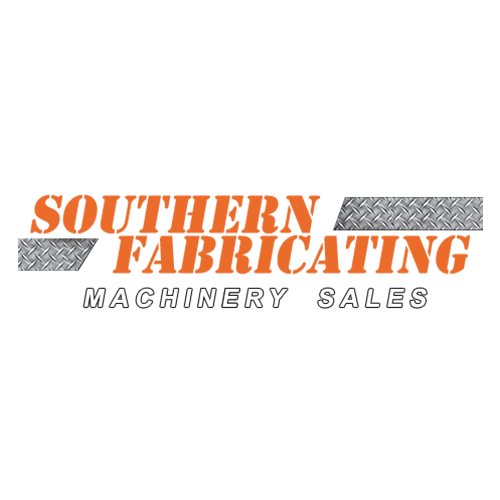
Posted By: Southern Fabricating Machinery Sales | Posted On: June 21, 2021
Improving the Accuracy and Performance of Your Waterjet Cutting Machine
In waterjet cutting, accuracy is one of the most important characteristics of the parts produced, but what causes accuracy or more importantly, the loss of accuracy on a waterjet? What can you do to improve accuracy and for that matter, overall performance as well? In a past article entitled Everything You Need to Know About Waterjet Accuracy for Precision Cutting we looked at accuracy characteristics. In this article we will look into what systems and components directly relate to the accuracy achieved and look into how to maintain these systems critical to waterjet cutting accuracy.
With a few simple trips you can keep your machining running accurately and efficiently providing better value for your money and more profit for your pocket.
Water Jet Machine Components
Before we can get too far on this topic it’s important to understand the main components of the waterjet cutting machine.
Water Jet Pump
The pump is utilized to increase the pressure of the incoming water from 4-50PSI coming from a normal wall faucet to 40, 50 or even over 90,000 PSI. There are two main styles of pumps available for waterjet cutting, Direct Drive and the Intensifier Style. These two designs serve the same purpose to increase the water pressure. Working with plungers, seals & hi pressure valving these pumps need to be maintained to perform properly and to prevent abnormal failure.
Water Jet Cutting Head
Another critical component of the waterjet cutting machine is the cutting head as it is here that the high pressure water is delivered, metered out and mixed with the abrasive garnet material before being dispensed through the nozzle. The cutting head holds the all important jeweled orifice that should be sized specifically for the pump horsepower and pressure the machine is operating at. The cutting head also holds the focus tube, or nozzle which directs the abrasive mixed stream towards the part.
CNC Machine
Of course any waterjet cutting system is not complete without the CNC Machine tool to drive the cutting head accurately and smoothly over the workpieces. This system of motion should be accurate and be able to position and repeat within a small margin of error (+/- 0.015” over a 6’ X 12’ surface in most cases). The accuracy of your part relies mostly on the accuracy at which your machine tool positions the cutting head.
Improving Your Water Jet Cutting Appearance
With an understanding of the basic components of the waterjet cutting machine we now need to look at a few variables of waterjet cutting that also affect accuracy & performance.
Determining Type of Cut and Setting Up the Cutting Head
Fortunately in waterjet cutting there aren't too many changes needed to the cutting head in order to cut a wide variety of parts and thicknesses (straight water cutting aside). However ensuring you have a correctly sized orifice and focus tube will eliminate many cut quality issues.
Cutting Speed Versus Cut Quality
Waterjet machines utilized speed to determine cut quality. As the abrasive waterjet process itself is actually a grinding operation, the slower the cutting speed the more material is ground away and thus the smoother the cut edge is. However speed should be used to not only make the part edge smother when needed, but to also increase efficiency and cut speed when edge quality is not as important. As an example, if you were waterjet cutting several holes that were high tolerance (of just a few thousands of an inch in size allowed), you would cut these on a high quality setting, which in turn slows down the motion of the waterjet. Adversely if you were cutting an edge that later is joined via a weld, then that edge quality likely is irrelevant and top cutting speed can be used.
Knowing how cutting speed affects the part quality is a very important part of efficient waterjet operation. Knowing when to apply different cutting speeds to maintain maximum performance and accuracy is the knowledge gained and applied by the waterjet owner.
How the Pump Pressure Affects Cutting Rate
Pump pressure is an important aspect for any waterjet machine as theoretically the ‘higher the pressure, the faster the cut’. However it does not mean that ‘the higher the pressure, the more efficient the cut’. Waterjet pressure can increase cutting speed but it does so at a cost (we detailed that in What Is the Optimal Waterjet Cutting Pressure?) as pressure increases 2 major effects happen. First water cutting volume is decreased which helps flow the abrasive through the material. Secondly consumable breakdown increases creating more downtime and repair expenses.
Pump Maintenance
Waterjet pump maintenance is important to keep your machine operating at peak performance while maintaining accuracy. As Pressure+Volume+Abrasive+Motion Speed = Quality of Cut desired a change to any of these aspects can drastically affect the result. On direct drive pump systems pressure is controlled by RPM of the electric motor. As the RPM increases the Pressure increases but so does the wear of the critical internal pump components. As such, most Direct drive pump systems are equipped with a High Pressure Gauge visible from the operator's position. Maintaining correct pressure via increasing or decreasing the pump motors RPM is critical to a quality part.
In intensifier pump systems the pressure produced is a constant and is not affected by the motor RPM thus the cut quality is easier to maintain. However knowing that pressure being output AND The volume of water produced at that pressure is critical to the operator in ensuring he has the correct orifice/nozzle/abrasive combination.
High-Velocity Pressure, Pump Life, and Cut Accuracy
In cases of Ultra High Pressure (87KPSI and more) there is a remarked decrease in pump and consumable life. While the immediate result is faster cutting speeds, the end result is the pump needs to be maintained at 2-3X more than the pumps operating in the 50-60KPSI range while producing only 30-50% faster cutting speeds. Cut accuracy is also affected by pump pressure, as pressure decreases there needs to be a calculated equal amount of speed reduction from the operator to ensure the part quality does not suffer.
Cutting Head Set Up
Having the correct setup on your cutting head can greatly affect accuracy and performance.
Varying Cut Head Set Up for Different Materials
While there are not too many variations for the cutting head setup (the cutting head is matched to the HP, Volume & Pressure of the pumps output) there is an important one when cutting with straight water (foams, carpet, cardboard, rubber etc). Removing the abrasive cutting head and mounting an orifice only setup can greatly improve the quality and efficiency of these softer materials. The orifice size will be reduced greatly (usually by 50%) and as such the pump will only need to produce at 50% equally making the cutting process more efficient.
Should I Use Single or Multiple Cutting Heads?
Using multiple cutting heads on a waterjet cutting system depends on several factors but in itself can increase efficiency without loss of quality by 40% or more.
The factors to consider are:
- Part size: Are the nozzles able to be spaced far enough apart.
- Pump HP: Does my pump have enough HP to feed multiple cutting heads?
- Material Consistency” Will my part move, twist or lift if I am cutting with 2 heads?
Knowing the answer to these questions can help you understand if adding 1 or more cutting heads to your machine will benefit your performance.
The Orifice and Nozzle
The orifice and nozzle are the last pint of the water/abrasive systems joining together to produce an accurate and quality jet stream. They are critically important to ensuring both accuracy and performance of your waterjet.
Orifice Quality Affects Cut Quality
The orifice is the hardened jewel sized precisely for the pump you are running. Over time the jewel’s surface can wear or may be damaged by particulates. A damaged or worn orifice allows too much water to flow past and moves the stream off the center adding wear to the nozzle below. Also ensuring you have the correct size orifice is critical to maintaining efficiency as using an orifice too small means you are limiting the speed output of your machine. Use an orifice too large and your pump cannot keep up the pressure and your cut quality suffers for your pump shuts down due to over-stroking attempting to reach pressure.
Orifices normally last approximately 40 Hours for ruby/sapphire models and 500-100 hours for diamond jewels.
When to Replace Nozzles
The nozzle sits directly below the orifice and is also called the ‘focus’ tube or ‘mixing’ tube as through this part the abrasive and high pressure jet stream are mixed and focused towards your material. Nozzles can be easily damaged and are highly brittle as they are hardened against the wear of the abrasive. Under normal conditions these nozzles wear fairly evenly over time and the hole grows approximately 0.001” in diameter every 10 hours of use. As the nozzle diameter grows so does the jet stream causing more material to be removed than necessary from the part. Ideally nozzles should be replaced after 100 hour of use AND rotated every 10 hours to ensure even wear.
Minimizing Abrasive Consumption
One of the important aspects of waterjet cutting efficiency is minimizing the amount of abrasive fed into the cutting head. As abrasive is approximately 70% of the waterjets operating cost it is important to use as little as possible while maintaining a quality and fast cut. Use too much abrasive and you needlessly waste it, excessively wear out the abrasive mixing chamber and nozzle in the cutting head and fill your water jets tank up faster requiring more cleanout downtime. Use too little abrasive and you likely are not cutting all the way through the material or leaving a poor quality edge.
Abrasive is metered out on every machine through a system designed and chosen by the machine manufacturer to provide an accurate flow of abrasive. Over time these abrasive metering devices themselves wear out and begin increasing, or dumping too much abrasive into the mixing chamber in the cutting head. Knowing your abrasive delivery system’s wear items (they may be wheels or sized orifices) is important to keeping them well maintained. Also verifying the output of your abrasive delivery system by physically measuring it with a cup and scale is important to proper adjustment and performance.
Eliminate Part Movement
Another important aspect of accurate waterjet cutting is eliminating part movement. Smaller parts can easily float up with water splashes. Larger parts may be moved by the cutting head after a part tip up. Consider clamping your workpieces to the table or within a fixture and tabbing smaller parts/drops when necessary to eliminate part movement.
Utilizing some simple steps can help you achieve better part accuracy and increase your performance on your waterjet cutting system. At Southern Fabricating Machinery Sales we know waterjets and waterjet cutting and can help you select the right machine for your needs and budget. Visit us on the web at WWW.SOUTHERNFABSALES.COM or better yet, call us for immediate help at 813-444-4555
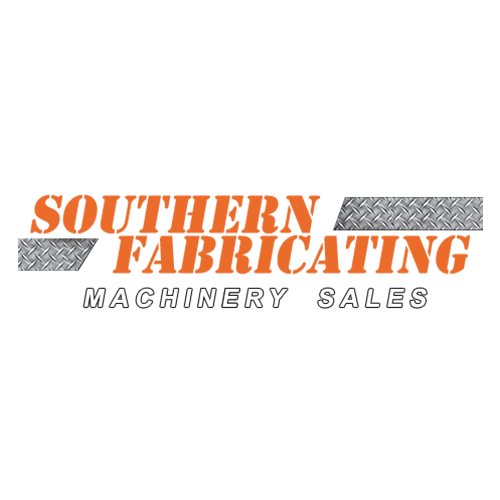