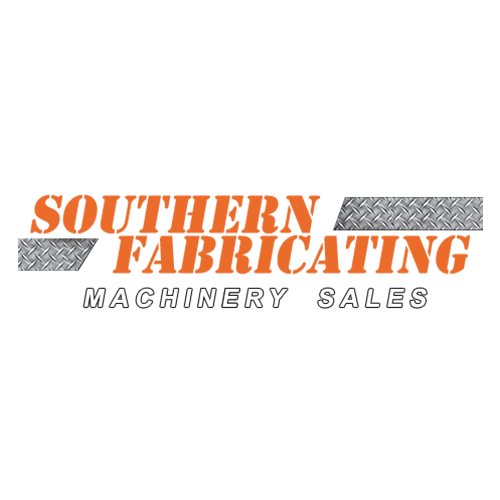
Posted By: Southern Fabricating Machinery Sales | Posted On: February 6, 2018
Waterjet Capabilities: Where Waterjets Fit
Think of the above as a balancing beam for your shape cutting process. On one side you have the CAPABILITY of waterjet. You can cut anything you can touch to tight and exacting tolerances, yet your operating cost will be in the $27-$30 per hour range and waterjet will likely be the slowest process of cutting your parts (provided they can be cut on another process). On the other end of the scale is CAPACITY or, in other words, mass production. This is where you need to make a lot of similar parts. On this side of the scale sits the processes of plasma, laser, and CNC Punching.
Breaking down these capabilities can help you decide which process is the right process for your shop and application. Waterjet may be the most capable for the shape cutting processes but sometimes it’s not the most feasible.
Waterjet
- System Cost: Medium (Typically under $200K new, $100K used)
- Process Type: Cold Grinding (Yes, AWJ is really a grinding process)
- Speed: Slow
- Finish Obtained: Similar to Sand Blasted
- Accuracy Obtained: Very Good
- Cost of Operation: High ($27-$30 p/hour avg.)
- Where this Process Excels: Alum & SS ½” and Over, Wide Variety of Materials from Plastics and Stone to Steel, Copper and Aluminum.
- Where this processes is easily beat: Mild Steel 1” and Under, ⅜” and Under SS and Aluminum.
Plasma
- System Cost: Low (Typically under $120K new, $50K used)
- Process Type: Thermal (Melting material to remove it)
- Speed: Fast
- Finish Obtained: Rough
- Accuracy Obtained: Poor (+/- 1/64th at best on average)
- Cost of Operation: Low (Standard Def $9-10 p/hour, MEDIUM if using Hi-Def $19-$21 p/hour avg.)
- Where this Process Excels: Steel from 10GA to 2”, SS to ½” (Rough Finishes)
- Where this processes is easily beat: Good Part Accuracies (Accuracy Needed Better then +/- 0.005”) Aluminum’s, and any Non Conductive/Non Thermally Yielding (Meltable) Materials.
Lasers
- System Cost: Low (Typically $85K - 250K new)
- Process Type: Thermal (Melting/Vaporizing material to remove it)
- Speed: Fast (Depends on wattage selected as well)
- Finish Obtained: Good to Excellent
- Accuracy Obtained: Very Good
- Cost of Operation: LOW ($9-$20 p/hour avg. using shop air)
- Where this Process Excels: MS to 7/8”, SS and AL to 1/4" (Depending on Power Chosen)
- Where this processes is easily beat: Mild Steel 1” and over, Alum and SS 1/4” and Over and any Materials that can catch fire (plastics).
CNC Punching
- System Cost: Medium (Typically $250K New, $100K Used)
- Process Type: Cold Punching
- Speed: Very Fast
- Finish Obtained: Sheared Edge
- Accuracy Obtained: Very Good
- Cost of Operation: Very Low ($7-$9 p/hour avg.)
- Where this Process Excels: Gage Materials (up to 10 Gage) and Part sizes under 4’ X 4’
- Where this processes is easily beat: Thicker materials (¼” & Heavier) , Stainless and other hard to punch/shear materials. Shapes with changing geometries where hard re-tooling is required
Where Waterjets Fit
Waterjet is often sought after as the most versatile (remember CAPABILITY) of the shape cutting processes, however, it can also be the most expensive method to make parts that could be easily be made acceptable or by a much more affordable method. Even though there are part and material requirements that do make waterjet a viable process for effective and accurate shape cutting, there are other affordable methods. Waterjet is CAPABILITY, but in most cases is not CAPACITY.
Whichever process you choose should be based on the minimum requirements of your part and budget or the 80/20 rule (buy for 80% of your needs and avoid trying to pigeonhole yourself into obtaining a machine capable of doing 100% as the cost will skyrocket very quickly). The team at Southern Fabricating Machinery Sales can assist you in selecting the right process for your needs AND budget. It's just another advantage of working with an experienced team of manufacturers just like you. Contact us today for more information.
To download a PDF version of this information, please click here.
The information contained herein is the express property of Southern Fabricating Machinery Sales or its partners and/or affiliates and shall not be reused without express consent in written form only! This information is provided as a courtesy to our customers for reference use only and we do not guarantee its accuracy for your application or use.
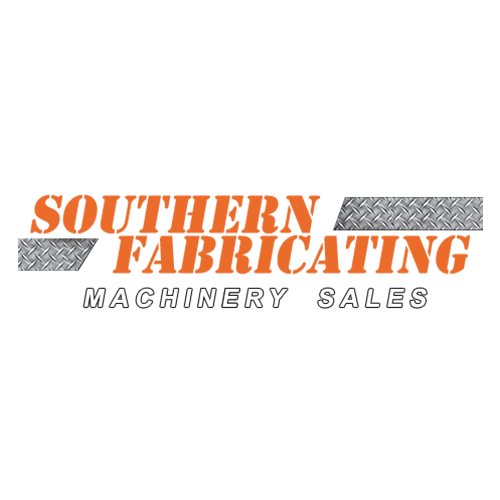