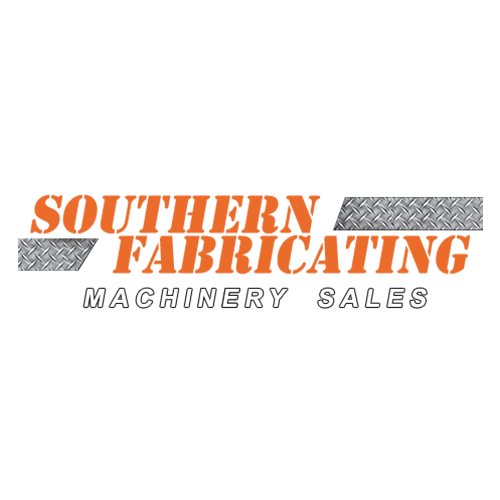
Posted By: Southern Fabricating Machinery Sales | Posted On: April 12, 2019
In Press Brakes It’s the Tonnage that Counts!
Press Brakes used to be classified by their bending capacity in steel. It was common in years past to have a customer looking for a; ¼” Brake, and although some may still refer to them in that manner, they were wrong then, and they are wrong now. Press brakes are “sized” by tonnage and bed length (overall bending length) and the correct nomenclature for a press brake is: Tonnage X Bed Length (ex. 175 Ton X 10’) or similar. The Tonnage dictates the operating capability of the press brake NOT the material being formed.
It’s All About Leverage!
Imagine taking a piece of ¾” Rebar 10’ long and clamping the end of it securely in a benchtop vise. Now imagine grabbing that rebar 6” from the vise and attempting to bend it at 90°. Did you imagine it would be very hard? Perhaps impossible to bend using only your own strength? Your right.
Now imagine grabbing the bar at the other free end of its 10’ length and pulling it backward. Can you imagine how much easier it would be to bend? Well using this example is exactly how press brakes work too the leverage their tonnage over an opening in a V-Die. The wider the opening, the less tonnage required, the smaller the opening the more tonnage required. .
The Math
Bending ¼” A36 over a 2” V-Die Opening takes 19.7 Tons of force per foot of material to bend which equates to roughly 197 Tons over 10’ of force. Using this tonnage calculation in the past the assumption was made that a 200 Ton X 10’ press brake was classed as a ¼” machine BUT here's where things go awry….
…..Using a 3” die opening the tonnage required to bend the very same 1⁄4” X 10’ A36 material drops to only 139 Tons which is well under the capacity of a 150 ton press brake. Adversely using a 1.5” V-Die would require 300 Tons of force to bend the same 10’ section of 1/4 “ material. So in actuality it’s NOT capacity that defines a press brake at all, but rather tonnage (or force).
But Wait There's More….
there are precautions that need to be considered. Just as your press brake has a Tonnage limit so does the design of your tooling. Straight punches over solid v-dies can take the heaviest loads whereas Acute Angled Tooling (highly angled punches, see photo at right) can take considerably less (there's less
material to stiffen it). On the “be very careful” end of the tonnage scale is the “Gooseneck” type of tools (See Image Left) that require careful consideration of their use due to their design. Because they have a “relief” are for reverse bends they are inherently much weaker then straight punches and special consideration should be used when using these forming tools as not to “over-tonnage” them and thus deforming a very expensive tool (HERE is a link to a full Catalog of Press Brake Tooling).
It is also important to note that you should never apply full tonnage over an area less than 60 percent of the distance between the side frames of your press brake. If your machine has 10’ between the side frames, full tonnage should only be used in bends of 6 feet or more. Using full tonnage over a shorter length would cause a section of your machine to be overloaded, resulting in some degree of deformation to the bed, ram, and/or tooling (i.e. PERMANENT DAMAGE).
Checkout THIS handy Tonnage Calculator (courtesy of Accurpress America) to try out different material combinations against varying Die Openings. This and many other useful tools can be found in our Helpful Info section of our website.
At Southern Fabricating Machinery Sales, Inc. we have the resources to help you select the right press brake for your material AND your part requirements. Call us today at 813-444-4555 or visit us on the web at www.southernfabsales.com to find out more about we can help you make the right press brake choice the first time.
If You Enjoyed This Article You'll Also Like:
Down-Acting Versus Up-Acting Press Brakes: Which is Better?
13 Steps to Inspecting a Press Brake
What You Need to Know About Press Brake Forming Technology
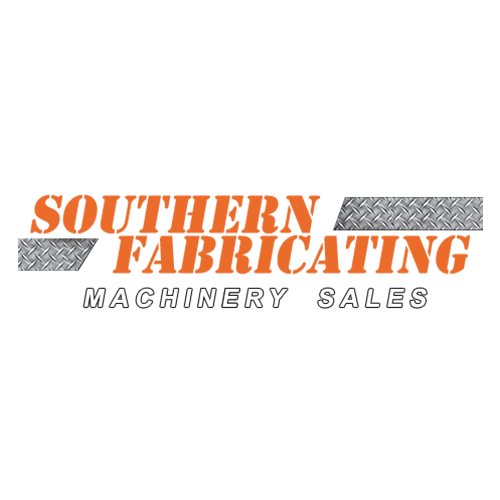