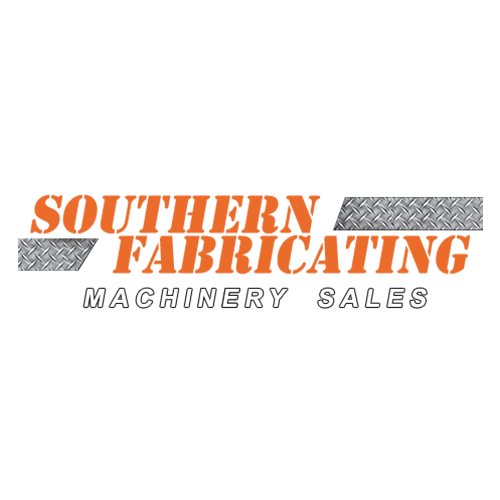
Posted By: Southern Fabricating Machinery Sales | Posted On: May 7, 2020
The Best Ways to Prepare your Fabrication Shop for A New Machine
One sign of growth when operating a fabrication shop is the need for new equipment. When you want to furnish your workshop with a new fabrication tool, you enter into a period of thorough deliberation, trying to decide the type of machinery you wish to add to your portfolio. Some individuals feel relieved after making this purchasing decision. However, they forget that for the device to be functional, it needs to be delivered and installed in your fab shop.
Preparation for the arrival of a new machine in a shop calls for lots of planning if you want to ensure that it is delivered and installed smoothly, efficiently, and as soon as possible. Prior planning prevents various issues such as reduced performance, chronic downtime of your production line, and high operating costs. Whether you're purchasing used or new machinery, there are few essential things that you need to do to prep your fabrication shop for new machines to save time and money.
Preparing For Machinery Installation
The Installation of Fabrication Machinery is not your usual cup of tea. It is a process that requires comprehensive planning if you want to address any installation concerns. These include doorway access, electrical capability, foundation requirements, and a plethora of other crucial things that help keep the process simple and safe for you and your employees as well as to reduce or eliminate any surprises.
Powering Your New Fabrication Equipment
Fabrication machines require power to operate. Therefore, the first thing you should do as a fabrication shop owner is to check the machine’s voltage, current, and power rating before you install new equipment. Armed with this information, you can now check your shop’s electrical capabilities to ascertain that it can handle the kind of load that will be brought by the new machinery. A handy tool is this Motor Amperage Requirements by Horse Power chart. Make sure that you factor in the energy requirements of other accessories that will be accompanying the new fabrication tool such as chillers, dust collectors etc. Evaluating the electrical requirements of a new piece of equipment helps you understand whether you need to upgrade the electrical system in the area of installation or bring another source from the outside power grid.
Meeting Foundational Requirement in Your Fabrication Shop
Another vital element that you should consider before machine installation is the foundation. Your new fabrication tool will need a robust and sturdy foundation that can support its weight, vibration, movements, and operational loads. It also needs to be balanced, leveled and properly aligned. Check the stability, leveling, and alignment of your fabrication shop's floor prior to equipment installation to ensure that you adjust it accordingly if it doesn’t meet the required threshold. When you determine that the floor in your workshop is not up to the task, you can reinforce it with a anchor’s, pour new concrete to add to its capability and thickness or sometimes just use a plate of steel as a pad to support the machine.
Inspecting Your Fab Shop
Atop the physical preparation of the shop, you also need to do a few things that are in the machinery inspection checklist. The purpose of machinery inspection is to determine whether the new fabrication machine can operate and adjust accordingly without posing risks to workers or affecting the operation of other tools in your shop. The kind of machine inspection you conduct will depend on the type of equipment you want to install, whether it is new or used, and the condition it is will be exposed to. The best checklist for your workshop should be tailored to the type of machine you want to install. It may include:
- Transportation checks. Based on the type of fabrication machine you’ve purchased, there are several shipping options that you can choose. From flatbeds to box trailers, there are several means of shipping your machinery safely, carefully, and affordably.
- Environmental checks. This helps to identify whether there are enough resources and space to allow seamless operations after the machine is installed. This also details entry procedures and emergency exit in case of fire.
- Lighting checks. You also need to ensure that there is adequate lighting to enhance safety and comfort during installation and later, when employees are working on the machine.
- Functional checks. These are done to ensure that all tools and accessories are in place and working as required. This includes the machine accessories, tooling, manuals, gauges and controllers in the case of CNC machinery.
At Southern Fabricating Machinery Sales, Inc. our staff are experienced in working with buyers of machinery to best help them be prepared for delivery of their new machinery all in order to help you get the most machine for the money. Call us today at 1-813-444-4555 or visit us on the web at www.southernfabsales.com for more info.
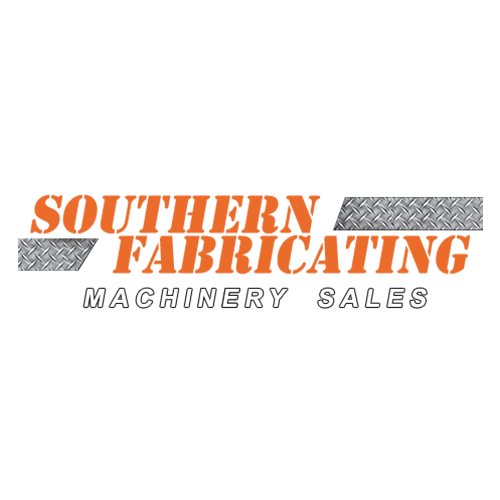