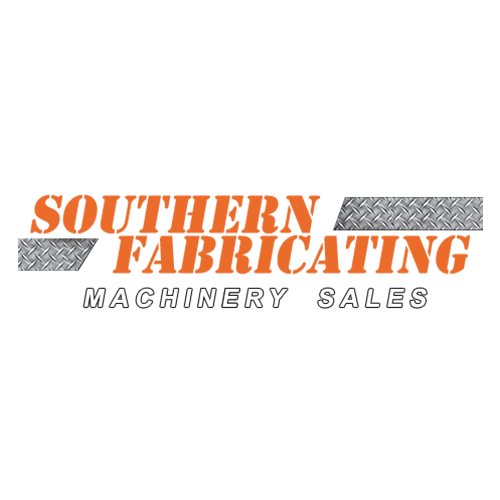
Posted By: Southern Fabricating Machinery Sales | Posted On: April 8, 2020
The Best Tips for Fabrication Machinery Maintenance
Fabrication shops rely on various types of machines to deliver top-quality products and although these pieces of equipment are built to be robust and durable, they still require frequent maintenance to stay in pristine condition and prevent serious accidents. Regular maintenance preserves the value of the equipment, extends its longevity, and keeps operators safe.
What is Fabrication Machinery Maintenance?
Fabrication machinery maintenance involves anticipating any mechanical changes, wear and tear, troubleshooting your equipment and taking corrective actions to ascertain reliability and performance. It is all about creating a plan and scheduling maintenance whether it is preventive, predictive or restorative maintenance. Successful fabrication machinery maintenance helps you extend the life of your equipment, minimize unscheduled downtime, and save you hundreds of dollars you would’ve spent in repairs or replacements.
Preventative/Preventive Maintenance vs Corrective/Restorative Maintenance
Though there is a little bit of confusion about the terms ‘preventative’ and ‘preventive’, they refer to the same thing. Preventative/preventive maintenance is planned in advance to avoid catastrophic breakdowns later. It helps to keep fabrication machines at peak performance by detecting problems early and restoring them to their pristine condition before any failure occurs.
On the other hand, corrective maintenance is done as soon as a problem is detected. You don't plan or anticipate a problem, but it is rectified once it occurs.
There is also the predictive maintenance, which is the same as preventive maintenance in the sense that the problems are anticipated long before they occur. However, this kind of support is not based on a schedule per se but involves the use of technologies or instruments to gather data that can be used to determine what accessories or parts need repair or change.
Lastly there is Restorative maintenance which refers to maintenance scheduled during down time to replace or repair non critical functions of the machine such as tool changers, doors, guarding, etc. These items generally do not prevent a machine from operation but provide overall value and safety for it.
Best Practices for Machinery Repairs and Maintenance
- Check, Test, and Change Lubrication Regularly
Fabrication machines involve a lot of moving parts and thus rely on lubricants for better functioning. Since lubricants help reduce wear and tear, as well as keep the interiors of equipment clean, it is vitally essential to inspect and change the lubrication levels regularly. Ensure lubrication lines remain un-crimped and unclogged providing free flow of lubricant throughout the critical moving components of your machine. Check the quality of lubrication oil ensuring it is not contaminated with coolants or water.
- Clean Your Equipment Thoroughly
Although this might seem like an obvious thing, it’s one practice that’s often overlooked. If you want your pieces of equipment to run at maximum capacity and last longer, clean them daily and thoroughly weekly. Often during the cleaning process you will note items like broken switches, clamps, cracked or missing guarding etc that can all be added to the next planned restorative maintenance time.
- Utilize Preventive Maintenance Software
Since most of the fabrication tools use technology they have preventive maintenance functions directly on their controller. If they do not you can integrate them with robust preventive maintenance external software systems. These will help you monitor operating conditions and provide you with alerts when parts are due for maintenance or replacement.
- Document Operations and Maintenance Performed
Since most wear and breakdowns happen by unskilled handling, keeping records to help monitor operations so that you can know when and where a problem occurs. It is also vitally essential to document maintenance and repairs so that you can pinpoint areas that are prone to wear and breakage in the future as well as create a specialized maintenance program to prevent unexpected downtime later.
- Don’t Exceed Performance Specifications
All fabrication machines come with a set of specific performance limitations such as predefined range of temperature and pressure, as well the maximum working time. Shop owners must ensure that they check the operator’s manual to familiarize themselves with their machines limitations. Using equipment beyond the recommended performance level increases wear and tear, compromises efficiency, and can lead to accidents.
At Southern Fabricating Machinery Sales we provide resources to maintain and inspect your machinery. Click on the link below for an in depth inspection checklist for your current or future machinery.
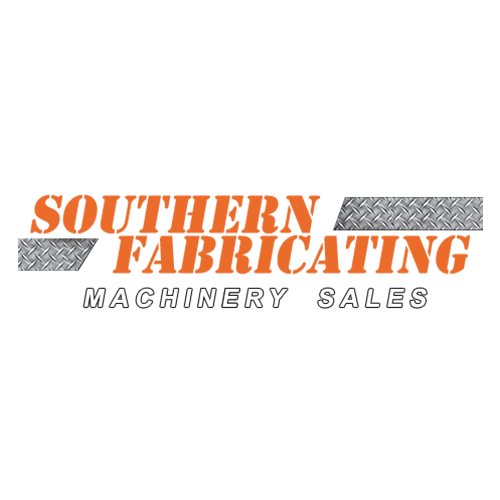