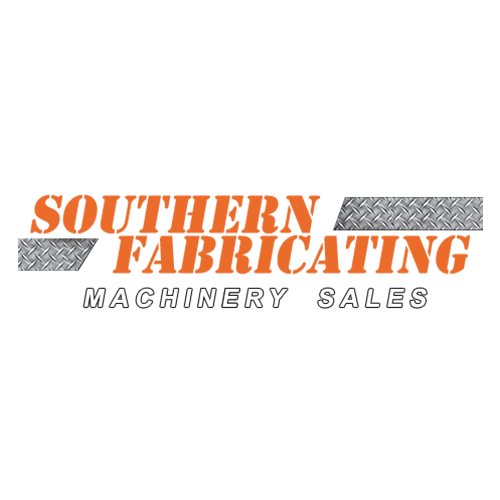
Posted By: Southern Fabricating Machinery Sales | Posted On: March 4, 2019
How to Get Ready for Your New Waterjet Machine
When you have made a decision to purchase a waterjet cutting machine you should be prepared in advance for a successful arrival and installation. These 4 simple steps can help ensure your successful arrival and delivery of your new (or new to you) waterjet cutting system.
Step 1 - Space
Seemingly simple enough but you need to ensure that not only do you have the space for the system allocated but account also for the accessories and additional components required. We suggest you take tape and mark off the location for each piece like the main waterjet machine, control, bulk abrasive hopper, pump and any other accessories such as chillers, abrasive removal systems, water recycling systems etc. Make sure in this step you not only mark the area required for the machine and the accessories but you also mark of electrical, air, water and drain connection points as well, as this will be helpful in having the facility pre-plumbed and wired for your new machine. Also ensure you allocate space for required maintenance around the systems.
By ensuring you have the proper space reserved for your system you can preplan not only the delivery, placement and power drops required but also ensure the order in which these items are brought into your facility. Also a special note of consideration should be taken to ensure all components can fit through the doorways into your facility as trying to move a 12’ machine through a 10’ door can be very problematic if not properly planned (i.e. skate it in sideways).
Once you have selected a space for your waterjet machine, visualize loading and unloading of large sheets of material in the method you will be using: .
-
Will you be using a forklift?
-
Overhead crane?
-
Jib Crane with Vacuum lifters?
-
Manually lifting sheets on?
All of these scenarios require space and special consideration to properly, and safely load and unload your machine. Make sure you have enough space for these items to operate safely and properly in the area you have allocated.
Step 2 - Power
Every waterjet cutting machine requires power, with most requiring 3 phase power but you must also account for the other system components and accessories that require power also. While laying out your system in Step 1 you will be noting the required power for the multiple components and the the electrical drops required. It is not uncommon to have a Pump requiring 460V 3 phase power and the machine controller requiring only 230 Volt Single phase. Add in the other components requiring power such as Abrasive Removal Systems, Chillers and Water Recirculating/Recycling Systems and you can see that proper planning of your electrical is critical in ensuring the success of your waterjet cutting systems delivery and installation
Step 3 - Water
A water supply is absolutely necessary for a waterjet cutting system, even if a closed-loop water recycling systems is used. Access to a clean water supply is imperative. Your waterjet cutting system needs anywhere from 1-4 GPM of water either supplied from your tap or via a recycling system. That water needs to be supplied at a pressure of between 35-50PSI (consult your machine/pump manufacturer for specifics) and should be cool (45°-60° preferred) clean and free of debris and contaminants (Here is a great article on Water Recycling and Water Quality). Plan in advance on a simple wall mounted filtration system and possibly adding a water softener system (as detailed in our above linked article) to ensure water quality meets your machine/pumps manufacturers requirements and guidelines.
Note: If your facility does not have enough water pressure, or if water pressure is inconsistent throughout the day (Multi-unit facilities are common for this), then an inexpensive water booster Pump can be added to increase the pressure required to your machine.
Step 4- Air
Air pressure is required on every waterjet system and you should not only be supplying a sufficient air pressure (usually 90+PSI) and quantity (8-10 CFM is common) but you should make sure you have clean and DRY air. As most machines use air pressure to feed the abrasive to the cutting head you should be aware that moisture in the airline can lead to the abrasive becoming clumpy and thus clogging the pathways leading to your abrasive waterjet cutting system turning abruptly into a straight water cutting machine. Also air-pressure is used to Open/Close the HP valves on the machine. Check with your specific machine manufacturer for air pressure and volume requirements and ask about an air dryer for your specific needs. A quality air dryer can be purchased for just a few hundred dollars on up depending on the size of the system required.
Step 4 - Drain
All that water has to go somewhere and even when a closed loop/recycling system is used on your waterjet cutting machine, access to a drain can greatly assist in cleaning out the machine for periodic maintenance. While a drain doesn't have to be in the floor, at the machine, it should be readily accessible even if extension drain hoses/lines and pumps are used.
If you follow these 4 simple steps you can avoid most every delay in getting your facility ready for your new waterjet cutting system. Combined with your machinery manufacturers requirements, you can also eliminate headaches and hassles along the way and getting your new waterjet up and running in your shop in a timely manner.
Do you want to discuss how a Waterjet Cutting Machine from Southern Fabricating Machinery Sales, Inc.can work for your application? Contact the experts at Southern Fabricating Machinery Sales today!
Ready to Shop for a New-To-You waterjet cutting system? Just click here for a shortcut to all our available systems.
Like this post? You’ll also enjoy:
Is a Water Recycling System Right For Your Waterjet?
Is 5-Axis Waterjet All Wet?
Waterjet - Intensifier Vs Direct Drive Which is Better?
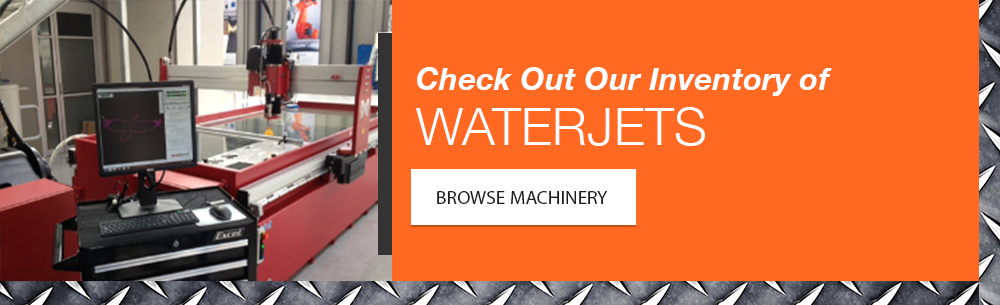
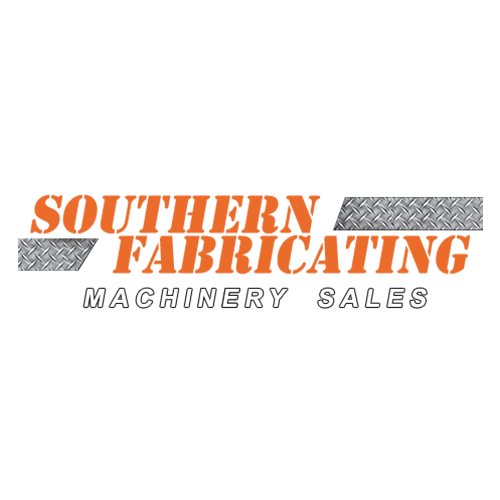