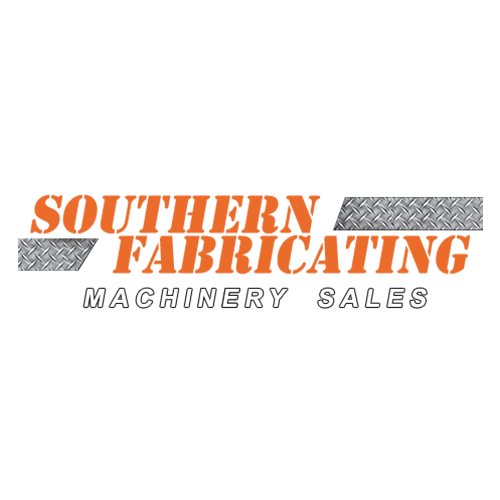
Posted By: Southern Fabricating Machinery Sales | Posted On: August 24, 2020
The CNC Turning Center vs. the CNC Lathe
If you don’t know the difference between a CNC turning center and a CNC lathe, you’re not alone. It’s a common mistake, even for people who work with them. They look very much like the same machine tool and they perform pretty much the same type of task. And although Lathes are one of the earliest tools known to man, Turning Centers are the upgrade.
CNC Lathe vs CNC Turning Center
Traditional lathes spin material while introducing a sharp tool bit moving in a linear pattern down the longitudinal axis of the material thus cutting material away to get the desired shape. In both processes a cutting tool cuts material away to create something circular. While the lathe was a manual machine performing these tasks by a skilled operator the addition of a CNC control helped to automate and provide simultaneous axis control. Both the CNC Lathe and the CNC Turning Center are capable of performing these tasks however the Turning Center takes the capability to the next level by adding automated tool changing, live rotating tools, efficient chip removal and the ability to add features that would allow many components to be completed in one setup.
What is a CNC Lathe Machine?
The CNC (Computer Numerical Control) is taking over many of the traditional tools and machines manufacturers use. The addition of the CNC control to a standard lathe allows for repetitive/production easily and multi axis control for creating angles, and radii on turned parts. Traditionally Lathes are of Flat Bed design with a powered gear driven headstock at one end and an adjustable tailstock at the other. In between the tool carriage rides on the bed carrying the tool mounted atop a cross (and sometimes compound) slide in order to perform the tasks of machining. CNC lathes are quickly replacing many of these older manual lathes including some systems that were semi-automated like the multi-spindle lathe. These CNC Flat Bed design lathes can be easily set up and operated, and because they still offer the manual controllability they are perfect for the toolroom, designer and lower production requirements.
These lathes can also be controlled by a coded file that is uploaded to the CNC Control or positioned manually and each position “remembered” for the controller to return to later in a sequence. The machine will produce the design repeatedly for what it was programmed to make. The limitation of these machines is they typically are not equipped with an automated tool changer nor are easily automated for material handling, such as a bar feeder.
What is a Turning Center Machine?
One of the first differences between a lathe and a turning center machine is CNC turning center is usually housed within a full machine enclosure to protect the operator and surrounding area from the chips and coolant used during the cutting process. These machines are also not a “Flat Bed” design but are a “Slant Bed” where the bed and way system is actually behind and at an angle to the center of part rotation. By utilizing this unique slant design the machine is much better able to control the chip flow allowing them to drop directly under the rotating part and be easily removed by ship conveyors or screw augers.
A CNC Turning Center also has a higher RPM capability and due to the robust design and innovative Carbide & Ceramic tooling has the ability for extremely high material removal rates. Further a CNC Turning Center can be fitted easily with “Live Tools” which gives the machine the capability to stop the spindle and let these rotating tools in the turret perform milling, drilling and tapping tasks across the turned profile. Coupled with the ability to automatically change tools within a programmed cycle and the ability to auto feed material through the spindle (or via a robotic loader) these CNC Turning Centers are production power houses.
There are two types of CNC turning centers: horizontal and vertical. Horizontal turning centers are the most common. With the horizontal turning center, the spindle is horizontally oriented, and the tools approach from above the rotating part. They cut across the workpiece using gravity to pull the chips away from the workpiece and down into the bed where they are easily removed by other methods along the machine to continue to cut for as long as material is fed into it.
Vertical Turning Centers are typically called a vertical turret lathe or VTL. This design simply uses the rotating chuck set flat on the ground to allow for the machine or larger pieces at lower RPMS. The tool turret or carriage approaches from the side. Other versions of this design “Hang” the spindle from a slide moving the headstock with the part firmly gripped, up and down across a moving tool for material removal. These type of inverted spindle lathes are excellent for small parts that require a second turning operation and are otherwise not easily automated (think castsings).
CNC Turning Center or CNC Lathe: Which is Right for Your Project?
There unfortunately, is not yet a machine that can do all the things you need it to in the cycle times you need them done in. When it comes to the difference between the CNC Lathe or CNC Turning Center, it comes down to the difference between prototyping and the production rate desired. The CNC Lathe is better at short production runs, simple parts like pins and bushings and quick repairs as it can easily be setup and raun from either a manual method or CNC program.
The CNC Turning Center is the choice for production and material removal. Although it is not as easy to setup and operates only via the CNC controller it performs many more automated tasks and repeats them at a much higher rate then a CNC Lathe could do. If you want a machine that can be programmed to complete several different tasks then the more flexibility it has, the better it is for your different projects. However, the CNC Turning Center with milling capability and multiple axis capabilities like Y-axis, sub spindle etc (also referred to as multitasking machines) simply provide an enormous advantage for production over a simple CNC Lathe.
Find The CNC Machine for Your Needs in Our Inventory
The advantage of any CNC machine is that they can be programmed to suit your every need. You can find great used equipment here, to help save costs and still get an excellent machine. Contact us or take a look through our inventory. If we don’t have what you need, we have the connections and can happily find it for you.
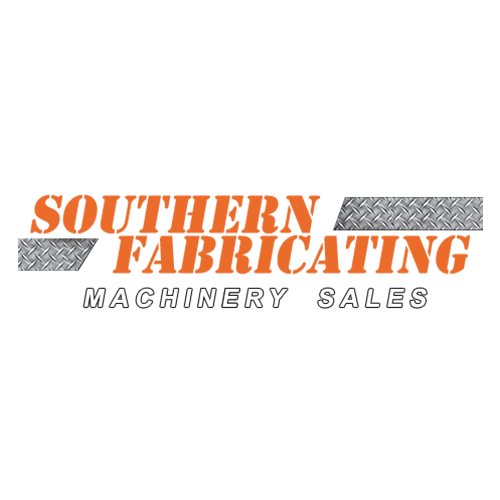