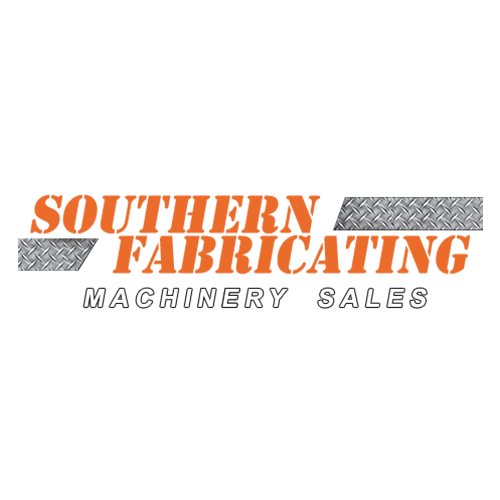
Posted By: Southern Fabricating Machinery Sales | Posted On: May 19, 2021
4 Reasons You Need a CNC Turning Center For Manufacturing
CNC turning centers can be a critical piece of equipment for many machine shops. These machines can enable machine shops to create intricately-detailed custom parts with a great degree of accuracy and repeatability. In this article, we’ll talk about what a CNC turning center is, and some of the reasons why your machine shop definitely needs one.
What is a CNC Turning Center?
A turning center is a machine that holds a part in place using a “chuck.” The chuck spins in place at varying speeds while the machine’s tool presses into it. The oldest manual version of this device is usually called a “lathe” and would be frequently used in the creation of wood products with vaguely cylindrical shapes.
A CNC turning center is an automated machine that uses a computer numerical control (CNC) system to control various factors of the machine’s operation, such as the chuck’s rotation speed, the movement and angle of the tool, and tool selection. CNC turning machines come in two basic varieties: vertical and horizontal. This distinction is based on how the machine holds the part—which can affect how much floor space the turning center needs (horizontal turning machines generally need more floor space, whereas vertical machines are taller but need less floor space).
One advantage of vertical machines that some operators have noted is that the weight of the held part helps to hold it in place.
CNC Turning Center vs. CNC Lathes?
Using a CNC turning machine offers several advantages over traditional, CNC Bed Type lathes, including:
- CNC Lathe Operations. CNC Bed Type Lathes are setup and controlled by the operator and are subject to a number of variable factors. This could create inconsistencies in part shape and quality from one workpiece to the next. Using a CNC machine ensures much more precise operations, allowing parts to meet stricter tolerances with better consistency.
- Automation of Turning Operations. Some CNC turning centers are designed with controls that make it possible to automate the production of certain parts. On these machines, you could program the rotation speed, tool selection, and tool movement ahead of time to minimize the need for an operator to manually control the turning operation.
- Production Speed. A CNC turning machine can run continuously without needing to take a break, whereas a CNC Lathe requires manual intervention for tool changes, scrap/waste cleanout and part changeover. This allows CNC turning centers to produce parts at a faster rate per day than manually-operated machines.
Also, once a program for making a particular part is created, it can be easily saved and uploaded again as needed. This reduces the reliance on expert labor for manufacturing specific parts.
Types of Turning Centers
CNC Lathes as we discussed above there are two main types of CNC turning centers, the horizontal and vertical machines. However there are other variants of turning machines that you should be aware of.
Swiss Type: These machines typically run smaller parts 1.25" and under and are known for higher production rates, faster cycle times and fully automated operation. These types of CNC Turning centers slide the material through a rotating collet where multiple tools approach the material at once performing a variety of operations. Commonly used in the medical, contact and gas consumable industry Swiss type CNC Lathes are an important production machine.
VTL's: VTL's are short for Vertical Turning Lathes and unlike a machine with a vertically suspended and moving chuck, which is used to pick up, machine and place parts, these machines are larger and used for turning things like valve housings, large gear rings etc.
What all these various types of machines have in common is that they turn the workpiece in order to perform the cutting and machining operation.
Benefits of Turning Center Machines
Higher Productivity: Once setup and qualified, these machines can run autonomous for many cycles. If equipped with the right automation they can produce quality parts for hours on end with minimal operator intervention.
Built in Automation: With the CNC Controller driving all functions of the machine, tool changes, coolant use, chip removal and part collection are all automated features.
4 Reasons You Need a CNC Turning Center
Lower Cost: Automating any process reduces the part cost by reducing the man hours required to produce it.
Increased Productivity: Adding the CNC Turning Center to your operation can add a capability you currently do not have or increase production rates to higher capacities with the same skilled staff level you currently possess.
Increased Accuracy: Once verified parts come off a CNC Turning Center consistent and repeatable. This increased accuracy adds value to your shop allowing for ever tighter and tighter tolerances to be achieved.
Reduced Waste: Once your CNC Turning Center is setup and producing parts you can count on accurate and usable components as a result. Less scrap means more dollars in your pocket.
New vs. Used CNC Turning Centers?
In the vast majority of cases, unless having a specific function that’s only available on a brand-new CNC turning machine is worth paying two to three times as much money, it’s usually a better idea to buy used rather than new.
Buying new doesn’t guarantee better precision, quality, or safety than buying used does. What it does guarantee is a higher asking price and a longer relationship with your creditor. So, when looking for a CNC turning center for sale, be sure to keep an eye out for used options as well as new ones.
Of course, if you buy used, be sure to thoroughly inspect the machine before you pay for it—or have an experienced used manufacturing machinery reseller appraise it for you. This way, you can avoid some of the potential pitfalls of private party sales and ensure that you get a high-quality used machine.
Need help finding the right CNC turning center for your machine shop’s needs? Contact the experts at SFMS today to get advice and assistance in your search for the perfect CNC turning machine!
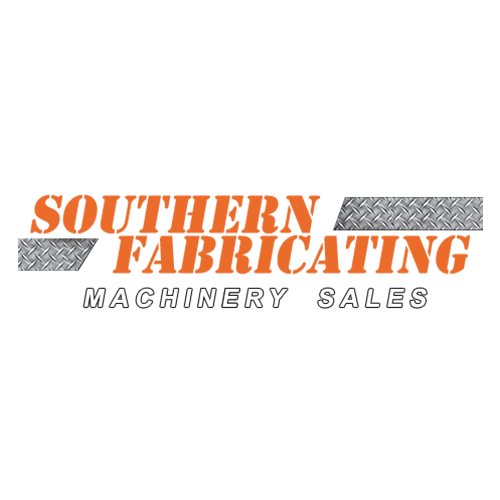