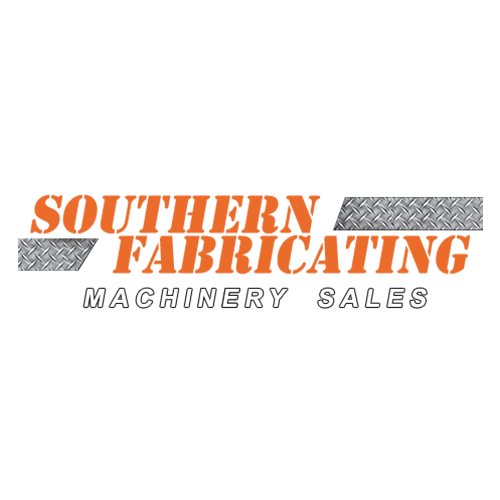
Posted By: Southern Fabricating Machinery Sales | Posted On: December 15, 2020
5 Benefits and Applications of Wire EDMs
For several decades now, electrical discharge machining (EDM) has been the solution for machining intricate parts and materials resistant to traditional machining methods or by necessity of design. This non-conventional process is one of the most efficient and cost-effective manufacturing methods since it delivers an extraordinary level of accuracy and unmatched precision. It works on parts that are electrically conductive, regardless of their hardness. EDM allows manufacturers to create complex shapes from hard materials such as titanium, stainless, steels, tool steel and other hardened alloys. There are three types of EDMs: Fast hole drilling EDM (Hole Poppers), Sinker EDM (Sinkers), and Wire EDM (Wires). However, for this article, we'll be looking in depth at Wire EDM.
What is Wire EDM?
Also known as spark eroding or spark machining, Wire EDM is a machining process where an electrically charged single strand wire is constantly fed within a dielectric fluid (usually deionized water) the resulting discharge when presented by the CNC in close proximity to the grounded workpiece is used to cut a conductive material. The wire is moved closer to the part being worked on to produce electric sparks that cut, or rather erode, through the metal. They are flushed and usually immersed in deionized water to get rid of the particles, cool the wire from breakage and control the sparks.
How the Wire EDM Process Works
The starts with the thin piece of electrically charged wire made of brass of any other material being held in position by the upper and lower guide. An electric discharge between the wire and the conductive material produces some sparks, which are precisely guided to cut through the material to achieve the desired cuts. When a piece is being worked on, it is submerged in deionized water to cool and flush out the debris produced.
When the wire is brought closer to the conductive metal rapid electrical discharges are produced. The discharges erode the metal on the focused areas, leaving no blemishes or deformations. The CNC controls the path the wire follows producing a contoured path bound only by the size of the wire itself (usually 0.,010” in diameter).
The Five Benefits of Using a Wire EDM
- Allows for the Formation of Complex Parts
The use of precisely focused electrical discharges makes it possible to make complex or intricate shapes and patterns. Wire EDM machines can make different shapes, such as contours and holes, even on the hardest and the most fragile materials.
- It Doesn't Need Mechanical Force.
Unlike a vast array of fabrication processes that use impact to cut through materials, Wire EDM leverages thermal discharges to cut through parts. This means that the end product will not be deformed, distorted, or have any side effects of deformation caused by brute force in material removal.
- Cost-Effectiveness
When you use Wire EDM, you'll not have to use a lot of energy to cut even the most rigid materials. Additionally, you'll reduce material wastage since the process only removes the targeted particles only. Your cutting kerf (cut width) is usually less then 0.015”. Also, you don't need other machines for post-processing since the method delivers precise and accurate cuts.
- Accuracy and Precision
The best part about Wire EDM is that your final product will not need to be passed through other processes for them to be complete such as grinding, honing etc. The method delivers high levels of accuracy and precision, especially on the smallest pieces.
- High Tolerance
The other benefit of Wire EDM is the fact that you can achieve high tolerance regardless of the material you’re working on. You can easily achieve tolerance of +/- 0.0005” with some machines that offer tolerances down to a few microns.
Pros and Cons of Wire EDMs
Pros
- The process allows machinists to create intricate shapes and patterns, which can be quite challenging with most conventional machining methods.
- Wire EDM can be used on both hard and relatively soft material without any deformation or distortions. This is mainly because there is no contact between the EDM machine and the material being worked on.
- The method leads to the production of parts with fine and smooth finishes compared to other fabrication techniques.
- Wire EDM machines require minimal fixturing requirements as compared to other conventional machines.
- Most Wire EDM machines are self-threading, meaning that if the wire breaks during the cutting process, the operation can progress almost immediately without any delays.
Cons
- While the Wire EDM machines are relatively easy to operate, they may require more attention than other conventional machines. Their consumables can be expensive, and experts to operate the machines may be scarce.
- Although Wire EDM machines can be integrated with CNC and Automatic Wire Threading (AWT) capabilities to improve the production speed, they are usually very slow compared to other conventional methods.
- This machining method can only be used on conductive materials.
Common Application of Wire EDMs
Since Wire EDM is ideal for creating small delicate items, its application is widely spread. However, it is mostly used in:
- Blanking punches and extrusion dies.
- Automotive and aerospace parts and components
- Implantable medical devices
- Prototypes proof of concept builds
- Small hole drilling on hard and soft materials
At Southern Fabricating Machinery Sales we are experts in EDM with several Toolmakers and Application Engineers on staff to assist in your Wire EDM decisions. Click below or call us today for more information on how to add the capability of Wire EDM in your shop.
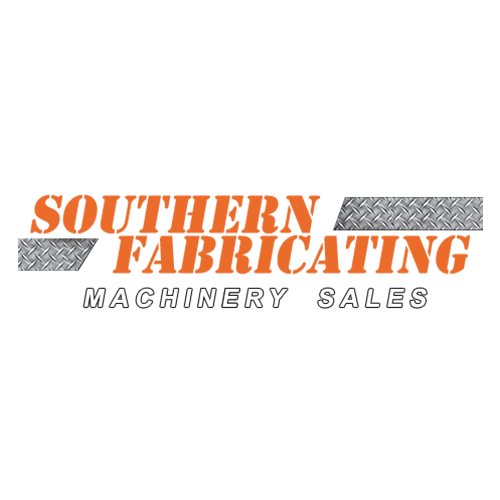