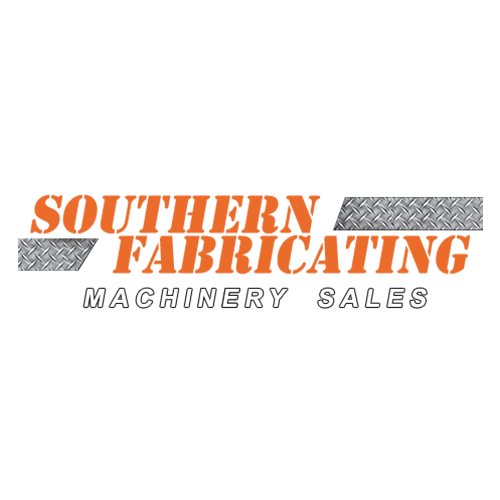
Posted By: Southern Fabricating Machinery Sales | Posted On: July 21, 2023
The 5 Most Critical Factors to Consider When Buying a Wire EDM Machine
Wire EDM (electrical discharge machining) is a CNC machining technology that uses a thin metal wire as an electrode to cut electrically conductive materials with high precision and accuracy. Wire EDM is ideal for creating small, intricate, and complex shapes that are difficult or impossible to achieve with other machining methods. Wire EDM can also cut hard materials, such as tungsten, stainless steel, and titanium, without affecting their mechanical properties or causing thermal distortion. As long as it's conductive, Wire EDM can cut it. Wire EDM is widely used in industries such as aerospace, medical, automotive, Tool & Die and Mold making.
However, buying a wire EDM machine is not a simple decision. There are many factors that affect the performance, quality, and efficiency of wire EDM machines. In this article, we will discuss the five most critical factors you need to consider when buying a wire EDM machine for your manufacturing needs.
Wire Type and Diameter
The wire type and diameter are important factors that determine the cutting speed, accuracy, surface finish, and cost of wire EDM machining. The most common wire types are brass, coated brass, zinc-coated brass, and stratified wire. Brass wire is the most economical and versatile option, suitable for general-purpose cutting. Coated brass wire has a thin layer of copper, zinc, or tungsten on the surface, which improves the conductivity and wear resistance of the wire. Zinc-coated brass wire has a higher melting point and lower resistivity than brass wire, which increases the cutting speed and reduces the wire consumption. Stratified wire has alternating layers of different metals, such as brass and copper or zinc and copper, which create sparks with different intensities and frequencies, resulting in a finer surface finish.
The wire diameter ranges from 0.002" - 0.013" (0.05 mm to 0.33 mm), depending on the application and material. The smaller the wire diameter, the higher the accuracy and surface finish, but the lower the cutting speed and stability. The larger the wire diameter, the higher the cutting speed and stability, but the lower the accuracy and surface finish. Therefore, you need to choose the right wire type and diameter according to your specific requirements.
Power Supply and Generator
The power supply and generator are essential components of a wire EDM machine that provide the electrical energy for the cutting process. The power supply converts the AC input voltage into DC output voltage, which is then modulated by the generator to create electrical pulses that generate sparks between the wire and the workpiece. The power supply and generator affect the cutting efficiency, quality, and reliability of wire EDM machining.
There are two main types of power supply and generator for wire EDM machines: transistor-controlled (TR) and capacitor-discharge (CD).
TR power supply and generator use transistors to switch on and off the electrical pulses, which can be adjusted in terms of pulse duration, frequency, peak current, gap voltage and duty cycle. The TR power supply and generator offer more flexibility and control over the cutting parameters, resulting in higher accuracy, surface finish,
and productivity.
CD power supply and generator use capacitors to store and release electrical energy in short bursts,which can be adjusted in terms of discharge energy, discharge time & discharge interval. CD power supplies and generators offer higher cutting speeds, power and stability but lower accuracy, surface finish and flexibility.
Axis Control and Motion System
The axis control and motion system are responsible for moving the wire and the workpiece along the desired cutting path with precision and accuracy. The axis control and motion system consist of servo motors, linear guides, ballscrews (or linear drives), encoders (or glass scales) and controllers that work together to ensure smooth, accurate, and consistent movement.
The axis control and motion system affect the cutting quality, complexity, and efficiency of wire EDM machining.
There are two main types of axis control and motion system for wire EDM machines: linear motor (LM) and ballscrew (BS). LM axis control and motion system use direct-drive linear motors to move the wire and the workpiece without any mechanical transmission components,such as ballscrews or belts. LM axis control and motion system offer higher speed,
acceleration, precision, repeatability and reliability but usually at a higher cost & power consumption.
BS axis control and motion system use ballscrews to convert rotary motion into linear motion, which are driven by servo motors through belts or gears. BS axis control and motion system offer lower cost and power consumption, but lower speed,
acceleration, precision, repeatability, and reliability (in general).
Wire Tensioning and Feeding System
The wire tensioning and feeding system are responsible for maintaining the optimal tension and feed rate of the wire during
the cutting process. The wire tensioning and feeding system consist of tension rollers, wire guides, wire choppers, wire spools and sensors that work together to ensure the wire is properly aligned, stretched and fed. The wire tensioning
and feeding system affect the cutting stability, accuracy and quality of wire EDM machining.
There are two main types of wire tensioning and feeding system for wire EDM machines: closed-loop (CL) and open-loop (OL). CL wire tensioning and feeding system use sensors to measure the actual tension and feed rate of the wire and adjust them accordingly using feedback control. CL wire tensioning and feeding system offer higher accuracy, stability and quality,
but higher complexity and cost.
OL wire tensioning and feeding system use preset values to control the tension and feed rate of the wire without any feedback or adjustment. OL wire tensioning and feeding system offer lower complexity and cost, but lower accuracy, stability and quality.
Dielectric Fluid and Filtration System
The dielectric fluid and filtration system are responsible for removing the debris and heat from the cutting zone. The dielectric fluid and filtration system consist of a tank, a pump, filters, a nozzle, and a chiller that work together to ensure the dielectric fluid is clean, cool, and circulated. The dielectric fluid and filtration system affect the cutting efficiency, quality, and safety of wire EDM machining.
There are two main types of dielectric fluid for wire EDM machines: water and oil. Water is the most common dielectric fluid for wire EDM machines, as it offers high conductivity, low viscosity, high flushing ability, low cost, and environmental friendliness. However, water also has some disadvantages, such as low lubricity, high evaporation, high corrosion, and high maintenance. Oil is an alternative dielectric fluid for wire EDM machines, as it offers low conductivity, high viscosity, high lubricity, low evaporation, low corrosion, and low maintenance. However, oil also has some disadvantages, such as low flushing ability, high cost, and environmental hazards and is used vary rarely in Wire EDM applications.
The filtration system for wire EDM machines can be either disposable or regenerative. Disposable filtration system use disposable filter cartridges or bags to trap the debris from the dielectric fluid and replace them when they are full. Disposable filtration system offer simple operation, low initial cost, and easy disposal. However, disposable filtration system also have high operating cost, high waste generation, and low filtration efficiency. Regenerative filtration system use reusable filter elements or media to trap the debris from the dielectric fluid and regenerate them by backwashing or cleaning. Regenerative filtration system offer high filtration efficiency, low operating cost, and low waste generation. However, regenerative filtration system also have high initial cost, complex operation, and difficult disposal.
Wire EDM machines are powerful and versatile CNC machining tools that can create precise and complex shapes with high quality and accuracy. However, buying a wire EDM machine is not a simple decision. You need to consider the five most critical factors: wire type and diameter, power supply and generator, axis control and motion system, wire tensioning and feeding system, and dielectric fluid and filtration system. By comparing the different options and features of these factors according to your specific needs and preferences, you can choose the best wire EDM machine for your manufacturing needs. Our experts at Southern Fabricating Machinery Sales can help you select the right Wire EDM machine for your needs. Call or click below today.
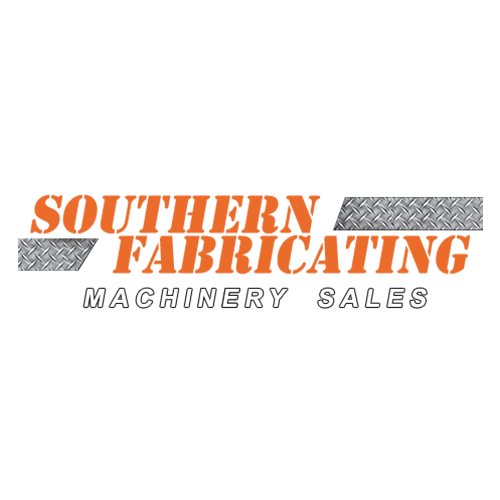