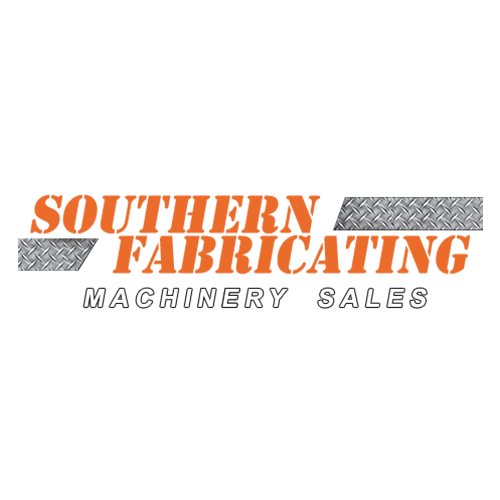
Posted By: Southern Fabricating Machinery Sales | Posted On: July 24, 2018
5 Things You Need to Know About Wire EDM Tolerances
Electrical discharge machining (EDM) is a critical tool for many modern manufacturing applications that has evolved over decades of use. One commonly used type of this machinery is wire EDM. This specific type of EDM uses a thin wire as an electrode to cut and shape solid metal pieces, and is often used for cutting solid steel.
To prevent the wire from wearing thin at the cutting point, it is usually continuously fed from a spool so the cutting surface is being constantly refreshed. The two types of EDM wire used in these machines are typically plain brass or zinc-coated copper or brass wires, depending on the application and whether you want greater service speed or lower cost.
One key issue with any piece of manufacturing equipment is the “tolerance” for that equipment—a measurement of how much the dimensions of a part made using that piece of equipment may vary from one work piece to the next. However, there are a few things that everyone should know about wire EDM tolerances in particular if they’re going to work with these specialized cutting systems.
1) The Effect of Dielectric Solution Purity On Wire EDM Tolerances
Most cutting systems rely on some form of directly applied physical force to achieve a cut in a material. Wire EDM tools are a bit different. Rather than using a sharp wire to cut materials, the wire in an EDM wire cutting machine is carrying an electrical current. A spark is carried between the wire and the workpiece by the dielectric solution in the wire EDM center’s tank, and that spark is what erodes a small section of the workpiece—creating a small bead of waste material that is then flushed away.
In a way, this process is like a highly localized version of electropolishing, which strips the surface layer of a metallic object placed in an electrolytic solution.
Variances in the conductivity of the dielectric fluid in the tank can adversely impact the precision of the cutting process. To maintain tight wire EDM cutting tolerances, it’s necessary to strictly monitor the purity of your dielectric solution and clean it regularly between cutting jobs. A good rule of thumb is to check the fluid at least once every 500 hours (20.83 days) and use two different electrometers for each test.
2) Power Feed Cables Can Affect Cutting Accuracy
If the dielectric solution in the cutting tank is pure, there may be another issue that could adversely affect your wire EDM tolerances: the power feed or grounding cables supplying the electricity for the cutting.
Over time (and especially in submerged-tank systems), the power feed and grounding cables supplying the electricity for your wire EDM cutting process can degrade. If your power cables or ground cables are worn out, replacing them can make for a major improvement in cutting performance and consistency for a wire EDM center.
3) Wire EDM Tolerances and Rust
While rust on the wire used as the cutting medium is rarely an issue for wire EDM machines (since the wire is being continuously replaced), other components in the machine can become rusted/pitted/corroded if not regularly maintained.
For example, the automatic wire feeding/threading system can develop rust if exposed to excessive amounts of iron particles without periodic cleaning. This could impact the alignment of the fed wire, reducing cutting accuracy or even making wire breakage more likely.
4) Pulleys, Belts, and Rollers
There are many moving parts on a wire EDM center that need frequent maintenance to ensure the machine is able to run at peak efficiency. Belts, rollers, and pulleys are some examples of critical components that may require frequent inspection and service. If one of these components becomes too worn, it can affect the accuracy of the EDM tool, and even make it unable to complete basic operations until the worn part is replaced.
This could be applied to any moving component in the EDM center that is used to move workpieces or the cutting wire, but pulleys, belts, and rollers are among the most common parts to need service.
5) Preventative Maintenance is the Key to Tight Wire EDM Tolerances
Like any tool in your manufacturing center, rigorous preventative maintenance can make a world of difference in the overall performance of your wire EDM center. A well-maintained EDM cutting machine can be an incredibly powerful, accurate, and reliable tool. A poorly-maintained wire EDM cutter, on the other hand, may put out inconsistent quality and require a lot of downtime to get it back up to standard—if it can be restored at all.
That’s why, if you’re looking to acquire a used wire EDM center, it is vital that you carefully inspect it and check its maintenance history before committing to a purchase. At the very least, you should have a trusted and licensed used machinery dealer or other expert carefully inspect the machine and investigate its maintenance history to verify that it’s in acceptable working order—and that there are no surprises attached (like equipment liens).
Need help finding the perfect Wire EDM center for your shop floor? Contact the used equipment specialists at SFMS today for help in finding (and vetting) the perfect piece of used machinery for your needs!
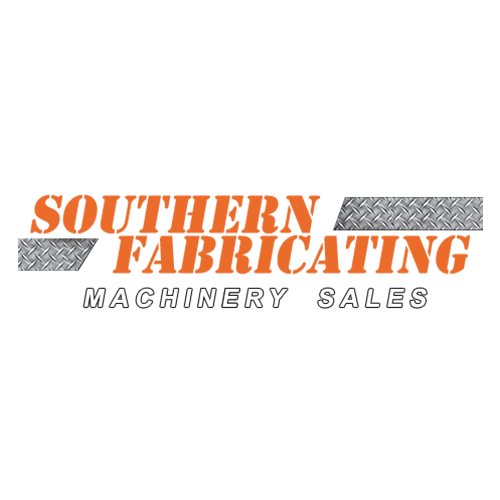