Wire electrical discharge machining (EDM) can cut amazing shapes with precision accuracy and very fine finishes. There are many wire choices, with each having their own advantages and disadvantages. Do you need to hold two-tenths or are you looking to go as fast as possible? Here is an easy explanation of the two basic wire types.
Coated Wires
If you are looking for just flat-out speed to hog out a section of your material to put back on the shelf for another job, large diameter .012”-.014” coated wire is your choice. Coated wires have a core of copper or brass, which is highly conductive, and a thin coating of a combination of zinc and copper. This outer coating protects the inner core, allowing high power settings with increased “on-times” for faster material removal rates.
Another advantage of using coated wires is less wire breakage compared to the same generator settings with plain brass wire. Coated wires come in various “types” from A-D. Each type provides certain benefits for each application. Although speed is the biggest advantage coated wires have over plain brass wire, some coated wires are better for accuracy, finish, poor flushing conditions, and materials like carbide.
With all that said, there is a cost factor to consider, too. Although coated wires can achieve cutting speeds that are 20-30% faster than plain brass wire, you will need to determine if the higher cost factor is justifiable.
Plain Brass Wire
The number one advantage for plain brass wire is its cost. If your application is not time sensitive and your flushing conditions are good, plain brass wire will be your best and most economical choice.
There are also cutting conditions where plain brass wire is your best choice! Do you need to cut tapers greater than 15 degrees? Then a super-soft (390 N/mm) plain brass wire is the best. Large tapers require the wire to bend immediately at the guides to create the proper angle. A harder wire will resist this bending, causing the cut path to be incorrect with a failure to achieve opening size at the top, bottom, angle, or all three.
Plain brass wires come in different diameters and, mainly, three tensile strengths or levels of wire hardness:
- Soft, like I just noted for steep taper cutting;
- Half hard for tapers from 5 to 15 degrees; and
- Hard for tapers less than 5 degrees and straight cutting.
The harder the wire, the more tension you can apply to create straighter cuts—most notably in roughing and corners. For ultra-precision tolerances of .0001” or less, a final skim cut with plain brass wire is also the best choice. Although minuscule, the zinc coating on the coated wires will vaporize faster than the core material. You will not experience this issue with plain brass wire.
It’s important to keep in mind that there are many other wire choices than these two. Smaller wires under .004” diameters may have steel cores or other combinations of materials. For most shops and applications, having a supply of .010” diameter coated and plain brass wire will be the best solution for your wire EDM applications.
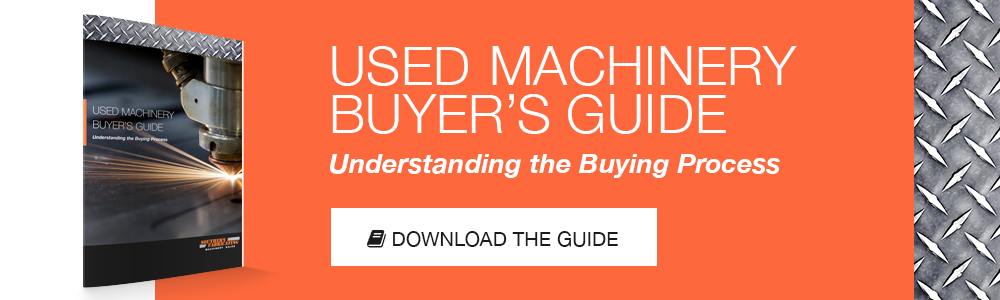