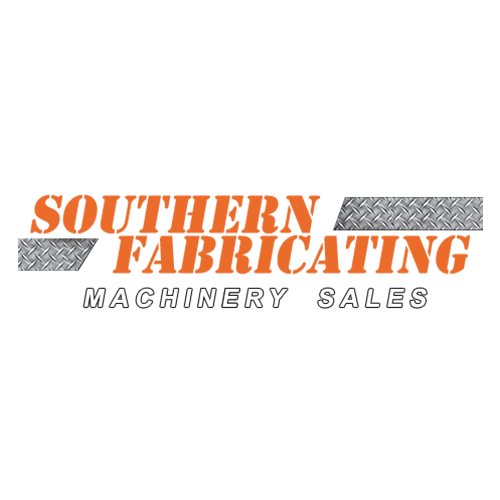
Posted By: Southern Fabricating Machinery Sales | Posted On: September 24, 2019
Plasma Cutting: 4 Reasons Why You Need a Plasma Table In Your Shop Now
In years past every fabrication shop wanted to grow their manufacturing abilities, and they did so by adding new capabilities and additional capacity like plasma cutting tables. As technology progressed in the following years, shops needed even more accuracy and leaned towards the affordable process of waterjet or the much more productive technology (albeit expensive) of laser cutting. Each of these alternative processes produced better accuracy and finish then CNC plasma cutting tables did but they did so at a cost. Waterjets where inherently much more expensive to run and lasers were much more expensive to buy, but either way the accuracy and finish was needed (In an article entitled Where Waterjets Fit we break down the processes and advantages of each of these shape cutting processes).
Throughout the years that followed, all of these technologies advanced and became more powerful, faster and more affordable. Although the often forgotten technologies of plasma cutting were growing too, many fabricators never gave them a second look. CNC Plasma Cutting Tables had become more accurate, provided better finishes and came at a lower investment cost than many other options available. However, now these Plasma Cutting manufacturers had added a new trick up their sleeve; Hi Definition Plasma.
Plasma Cutting Table Basics
Plasma cutting tables are a form of thermal cutting (cousin of the laser cutter). They literally vaporize metals into a powder form and remove them using a high stream of air or gasses from the cut zone. They are a natural progression from flame cutters (also called oxy/fuel) and a precursor to a waterjet or laser for production cutting. They are affordable to buy and inexpensive to run, producing quality fabricated parts that require little cleanup or post processing in order to go right into the next fabrication phase of welding or bending. What many fabricators haven't paid attention to as how advanced the technology, and thus how much better the part quality has become.
A plasma cutting table is typically a flat bedded surface comprised of steel slats spaced approximately 2-4” apart. These steel slats not only support the material being cut but also absorb the heat of the thermal cutting process. The plasma torch is suspended directly above and rides on a “bridge” over the material moving in conjunction with programs sent via the CNC control. The plasma torch and power supply are what provides the cutting capacity and cutting quality in Steel, Stainless Steels and Aluminum (the 3 main materials that can be processed). However, it is the design of the machine that provides the part accuracy, NOT the plasma power source, so it is imperative that a combination of a quality machine design and plasma power source be equal in order to produce the results your shop desires (In a recent article titled: The Burning Effects of Plasma and Oxy/Fuel we delve more into the basics of a plasma system).
Do I Need Hi-Def Plasma?
Plasma Cutting technology has taken great leaps and bounds forward (as have laser cutting, waterjet and the rest). These new advances in cutting have made the power sources more refined which in turn, produces a more accurate plasma stream. Coupled with better designed machinery the plasma torches are being positioned and moved with greater and greater accuracy. Combined these technologies are producing parts today that will appear just as good as laser cut parts from just a few years ago. Hi-Definition Plasma (Power Source Only) adds the proverbiale “icing on the cake”
Most applications for plasma cutting DO NOT require Hi-Definition (remember we have come a long way with Standard Plasma Too!) Therefore it is recommended if you are looking to add plasma cutting to your shop to look at part samples from standard plasma power sources as you can save many thousands of dollars choosing the right power source for what you need instead of the one you’ve heard about. All the power sources today produce much, much better parts
A Hi-Definition power source can be applied to ANY plasma cutting table. However, in order to get the benefits of that Hi-Definition capability, your machine needs to have a very accurate positioning system AND have a controller with the capability to use the power source correctly for features like Tru-Hole Technology (Read all about The Benefit of Plasma Using True Hole Technology here). In most cases a combined precision machine, controller and Hi-Definition Plasma Power source will be double or triple that of a like capable standard plasma system so the hunt for justification is a real one to be considered.
How To Use A Plasma Cutting Machine
While we can’t go into details in this article on how to operate a plasma cutting table in detail we can tell where you should be applying it to gain maximum effect and return on your investment. A plasma cutting table can be used to blank out simple steel, aluminum and stainless steel shapes to accuracies of greater than +/- 0.005” using today's technologies. Any steel parts that have accuracies of +/- 1/64” are great candidates for a plasma cutting table. Parts that require greater accuracies are likely better suited for a laser (steel) or waterjet (Aluminum and Stainless).
Benefits Of Using A Plasma Cutter
So what are the benefits of using a plasma cutting table in your shop or even in conjunction with other technologies for shape cutting such as Laser, Waterjet or even CNC Punching?
- Cost: Investment cost is low, operational costs is low
- Speed: Plasma processes material very quickly and efficiently.
- Simplicity: Setting up, Programming and Running a Plasma is a simple process.
- Capability: Making great parts, quickly and efficiently increases your chops capabilities.
At Southern Fabricating Machinery Sales, Inc our staff are Plasma Table Cutting Experts. We can guide you into the right new or used system to meet your needs. Matching the right machine to the right power source is a process we do every day. Contact us today at 1-813-444-4555 for immediate help or visit us on the web at www.southernfabsales.com
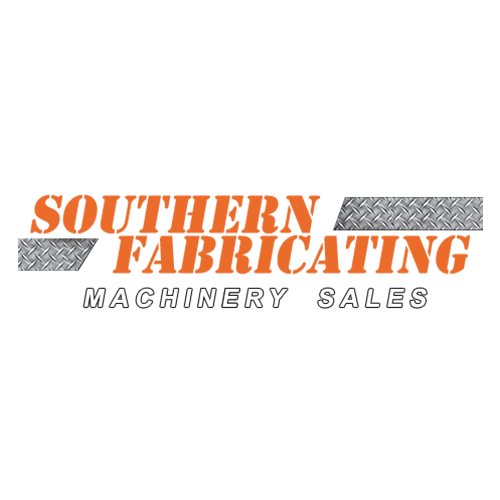