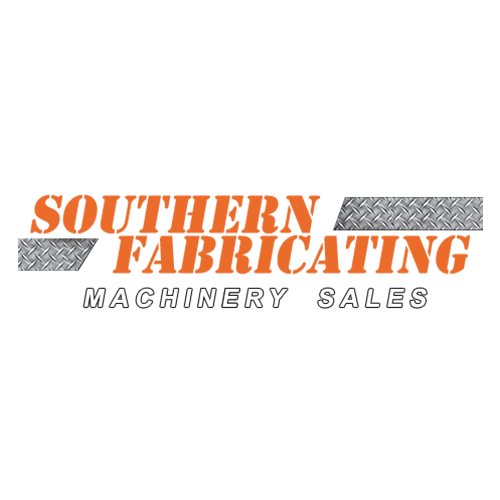
Posted By: Southern Fabricating Machinery Sales | Posted On: December 20, 2019
Plasma vs. Laser: What Is The Right Technology For You?
In metal fabricating today there is a wide range of shape cutting processes available. Laser Cutting, Turret Punch’s, Waterjets, Plasma and Oxy Fuel systems can all be vital processes in today’s shop, but which process is right for you? In a previous article titled “Waterjet Capabilities: Where Waterjets Fit” we explored the basics of each of these processes but we often find that the two most compared processes are laser and plasma cutting, specifically Hi-Definition Plasma cutting. So which of these two processes are best? Which is best suited for your application AND budget?
In this article, we shine a light on these two processes by explaining each type of cutting machine, the budgetary buy numbers for both new and used and provide you the process capabilities both good and bad to help you select the system that’s right for your needs.
THE SIMILARITIES
First off we need to cover the similarities between these two processes before we can define their differences. Both Plasma and Laser are thermal cutting processes that use intense heat to vaporize (not melt, think hotter, much hotter) metals into dust. Both processes use high pressure gas such as Nitrogen (NO2), Oxygen (O2) and Compressed Shop Air to assist in the material removal and finished edge of the process (it is recommended to have a large screw compressor available for each of these processes as they use a good amount of HP air). Both processes require some sort of fume collection system/dust collector to prevent the vaporized particles from coating every article in your plant ( in the case of plasma, a water table can suffice). Both processes use a certain set of consumables in the cutting head, such as nozzles to maintain the correct gas flow. Both systems use a large work area (typically 5’ X 10’) where the cutting heads are CNC controlled and pass over a stationary workpiece (although there are variations to this design the most common machines available today utilize this concept).
This is what the two processes share in common, but next is where we differentiate the two based on capability, operating costs, difficulty of the process and of course, the investment estimate whether your shopping for a new or used system.
PLASMA CUTTING
The basics of Plasma Cutting uses electrical current displaced through a conductive material such as Steel, Aluminum, Stainless Steel etc. in order to generate an intense electric field that we term the “Plasma” field. Inside the Plasma field temperatures reach in excess of 20,0000°F At that temperature range the metals (as previously mentioned) surpass the molten point and quickly are vaporized. These plasma systems can be hand held, track/mechanized mounted or computer controlled to provide for accurate shape cutting. Our comparison will focus on the CNC, or Mechanized mounted systems for this comparison, however previously we went in depth into the introduction of Plasma in a document linked here and entitled: Introduction to Burning and Plasma Tables
For cutting metals plasma systems are hard to beat for efficiency, price and speed. They provide relatively smooth cut edges, fairly good accuracy and consistent repeatability. It is however important to denote that a plasma cutting system is made up of 3 distinctly different components that must be tuned to work together to achieve the optimum results: The Plasma Power Source, The Plasma Cutting Torch and The Motion control System (i.e. the machine).
Plasma Power Sources: Plasma power sources can come in a variety of sizes and types and are defined in capacity by their “Amperage” Usually noted in the model name such as XPR-300 (300 AMPS). The amperage indicates the power supplies cutting capability and as detailed in a previous article: The Burning Effects of Plasma and Oxy/Fuel “Typically plasma power sources are rated at 1⁄2 their amperage for the overall cutting capacity in steels. As an example a 100 AMP power supply is typically rated to both pierce and cut 1/2” thick of steel and can cut from an existing hole or part edge up to 5/8” – 3/4” . Whereas a 200 AMP Plasma Power Source is rated to both pierce and cut up to 1” thick of steel continuously and can be used from a start hole at thicknesses up to 1-7/8”
Plasma power sources can be also defined as standard or AIR PLASMA sources or as HI-DEF (High Definition) Power sources which are the bulk of systems we see on mechanized machinery over 80K today. Air Plasma systems are usually most common in handheld plasma cutting applications.
Plasma Cutting Torches: Combined with the Plasma Power Source, the Plasma Torch Head is a key component in making precise and accurate cuts. The Plasma Cutting head is made up of several components but most importantly are the consumable components: the Shield Cap, Retaining Cap, Electrode, Swirl Ring and a Nozzle. These consumables, and their quality are directly responsible for the accuracy and cleanliness of your cut and parts finish. They have an expected life based on number of cutting hours used and the number of pierces (starts) achieved.
Plasma Cutting Machines (The Mechanized Part)The plasma cutting power source and the plasma cutting torch head can only provide a greater degree of precision on the cut edge of a material. While these components are critical to having a clean and straight cut they do not, in any way allow for overall part accuracy as that is purely a function of the table, or motion systems design.
Plasma Advantages:
- Systems investment costs are relatively low (starting at under 20K New)
- System operating costs are low ($5-7 p/hour on shop air)
- Accuracy is good (0.015”-0.020” at best)
- Bevel Cutting is easily performed
- Myriad of Power Sources available and easily adaptable/replaceable/upgradeable
- More "forgivable" process
Plasma Disadvantages:
- Thermal Process (Heat can warp thin materials)
- Conductivity in material Required
- Part Cleanup Required
- Accurate Part Stand-off Required
- Aluminum and Stainless Steels are difficult to achieve quality finishes.
- Automation is generally not available.
LASER CUTTING
In order to understand the basics of Laser Cutting it is important to note as previously explained, that like plasma Lasers use an intense heat source to vaporize material. However unlike Plasma that uses an electrical current to achieve this heat source, laser systems use Amplified Light to achieve the goal. In order to understand the process and its advantages or disadvantages it is important to know the basics. Laser stands for LIGHT AMPLIFICATION STIMULATED by EMITTED RADIATION or in other words a system that uses radiation to split and thereby multiply the ions of light creating more and more intensity and thus, heat.
Like Plasma cutting systems, lasers are made up of 3 very important and yet distinct systems; The power source or Resonator, The Cutting Head and the Motion System or table.
Resonators:
In past laser designs this was achieved through the CO2 resonator whereby a myriad of mirrors, hi-velocity pressurized gasses and RF Frequency generators were all used in conjunction to greatly split and amplify the ions of light sending that light through a complex "beam delivery systems". Today these power sources are mostly digital, have few moving or consumable parts within them and use a variety of fiber optics cables to transmit the amplified beam to the cutting head. WHile the original style CO2 machines are still made currently, their design is being phased out as the fiber optic and solid state designs become more refined and are far less expensive to build, maintain and operate.
Cutting Heads:
The cutting head is the final point where the laser beam is focused into the most intense dot of heat as well as where it is supplied with the required additional cutting gasses that shield that intense heat and assist in the vaporization process as well as the removal of that vaporized material. These cutting heads can be simple manually focused heads providing for simplicity in cutting and setup in a short range of materials to Auto Focused heads controlled via the CNC controller allowing for a wider range of automated material changes. It is paramount on a laser to keep these heads clean & cool as the intense heat created by the laster can easily be deflected by any dust particle leading to rapid heat buildup and thereby quick damage to lenses and internal head components.
Motions System:
Just like the plasma cutting system the laser machine needs a precise motion system in order to provide for accuracy. These motion control systems are typically not only accurate, but also very fast allowing for acceleration factors of 3G and beyond as well as rapid speeds in excess of 4,000 Inches Per Minute.
Disadvantages of Laser:
- Investment Costs (240K and up)
- Limited Material Range
- Cleanliness & Cooling of cutting head a priority
Advantages of Laser:
- Precision (0.005" in piece parts and 0.025" over full travel typical)
- Very Fast Process Times in Select Materials and Thicknesses
- Easily Automated
- Superior edge quality
- Slag eliminated
DECIDING BETWEEN PLASMA & LASER
Below is a great chart provided by our supplier of both plasma and laser cutting systems, Piranha Fab. This chart details the investment cost of basic to advanced systems along with their expected throughput and investment cost. While the chart isn't a rule, it is a great resource and guide to assist you in making the right decision between plasma or laser cutting for your shop and application.
At Southern Fabricating Machinery Sales Inc we know plasma and laser cutting systems and can assist you in deciding and obtaining the right system for your needs. Whether your looking to buy your first or tenth system we can help make sure your getting the best value for your part, process, application and budget. Check out our available LASER and PLASMA systems now or call us today at 813-444-4555 or visit us on the web at www.southernfabsales.com
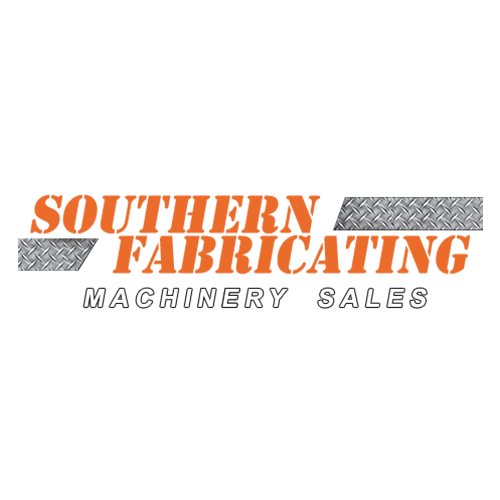