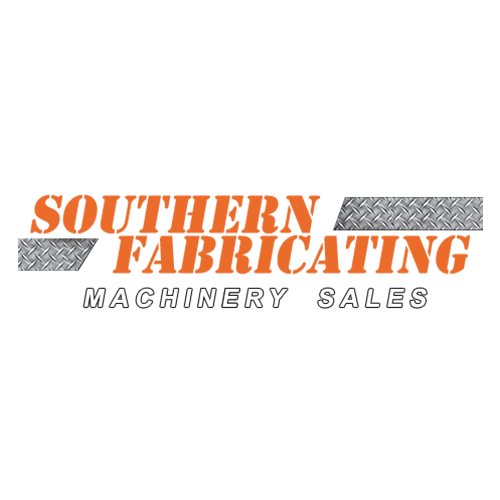
Posted By: Southern Fabricating Machinery Sales | Posted On: December 18, 2020
How to Choose the Right Tube Bender
Tube bending is one of the most fundamental functions of any fab shop. If you manage, own, or work in a fabricating shop you know just how important tube bending is. You’ll also know just how common tube bending is. Most fab shops engage in some manner of tube bending countless times per day. Here’s what you need to know about choosing the right tube bender.
What Is Tube Bending?
So what is tube bending? In concept, tube bending is pretty straightforward as it means about what you’d expect it to mean. That is to say, tube bending involves the bending of tubes or pipe. As basic as the concept might sound, tube bending is employed in a dizzying array of fabricating functions. Everything from saxophones to stair rails to roll cages require tube bending in their construction.
Tube bending is a rather generic term as often the material being formed is actually classified as “pipe”. The difference is subtle but important to know. Tubes can come in many different shapes from round to rectangular whereas pipe is always rounded. Also Tubing is usually thin walled meaning it is lighter and can hold less pressure whereas pipe walls are thicker and can hold internal pressures much greater. It's also most important when working with these materials to know that TUBING is designated by its external diameter where pipe sizes are designated by the flow capacity (i.e. NPS Schedule 40) meaning a 1” pipe and a 1” tube are not the same and require different tooling and forces to form.
Now that you know more about tube bending and the uses for it, it’s time to dive into some of the most compelling benefits of it.
Benefits of Tube Bending
The benefits of tube bending are as numerous as the potential applications and the number of resulting products that can be made. For example, tube bending is an essential part of the process of making such things as car exhaust pipes, musical instruments, and just about anything you can think of that has a tube that isn’t straight. Tube bending can greatly reduce sawing and welding operations for fabricators by making complex forms with simple bends as opposed to multiple sections welded together. Also formed tubing is much stronger then multi welded joints.
When you invest in tube bending equipment your fabricating shop will see a welcome spike in productivity. Tube bending equipment will make it possible to take on more work which means more money!
Types of Tube Bending
Naturally, some types of tube bending are more advantageous than others. Mandrel tube bending, for example, is one of the savviest and most beneficial tube bending techniques. Why is it so beneficial compared to other methods? Mandrel bending prevents tubes from developing kinks and flattening during the tube bending process by forcing the tube wall to stretch over the internal mandrel during the forming process.
Press bending is another tube bending method and a rather simple one at that. When using press bending to bend a tube you’ll need a press brake or an ironworker. This method is cost-effective and impressively versatile yet relies entirely on the outer wall not being of great concern for collapsing during the forming process..
Alternatively, you can use Angle Roll or Section Roller which pulls the tube through the rolls while applying pressure to create the desired bend.
Rotary draw bending is perhaps the most popular tube bending method of all as it is precise, easy to control, and offers the promise of repeatable results. With this method, a tube is clamped and bound to a die and subsequently drawn around the die. You can achieve this with hydraulic or electric equipment and this method can also be used with or without an internal mandrel.
Factors to Consider When Choosing the Right Tube Bender Machine
The key to the tube bending is to have the right equipment. The tools and machinery that you use play a big role in how successful and how efficient your tube bending efforts are. When you’re working in a fabricating shop, there’s no time to mess around which means that there is no time to spare for lack of proper tools. Consider the material you are working with, the accuracies you will need to form and the production quantity you need to make. These factors once considered, will go directly into selecting the right tube or pipe bending systems for you.
Learn More About Our Tube Cutting and Tube Forming Services Today!
Excited about diving into tube bending? Excellent! Then you’re going to need the right tools! There’s no better place to source tube bending machinery than Southern Fabricating Machinery Sales. We offer a massive variety of all manner of industrial, manufacturing, and fabricating equipment and machinery. You’ll find that our prices are refreshingly reasonable and that our customer service is unmatched.
Discover the efficiency and productivity of proper tube bending equipment, with Southern Fabricating Machinery Sales!
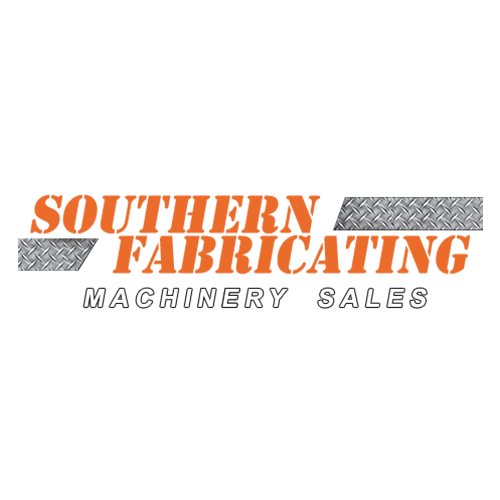