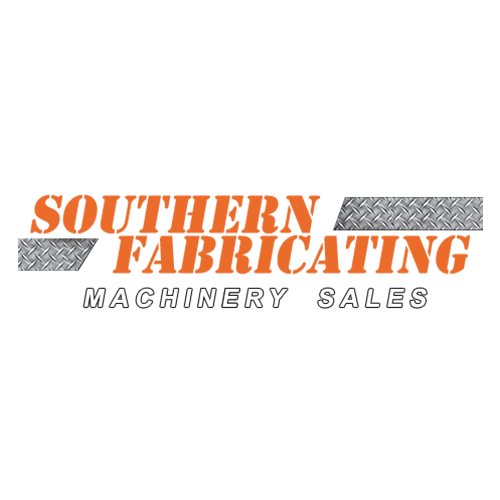
Posted By: Southern Fabricating Machinery Sales | Posted On: May 10, 2021
What Is the Optimal Waterjet Cutting Pressure?
In waterjet cutting the water cutting pressure is always talked about as one of the most important aspects of cutting efficiency, but is it really? Certain machine and pump manufacturers offer pressures in excess of 90 and even 100KPSI but what really is the optimal water jet cutting pressure for performance and reliability?
Understanding the Impact of Pressure and Velocity in Waterjet Cutting
As water cutting pressure increases cutting speed increases as well and if that were the only factor involved then 100KPSI Hyperpressure pumps would be the standard, but they are not as all the other factors involved make the game of waterjet cutting pressure vs cutting speed a tricky one. We have learned over the years that water pressure is important in cutting efficiency but also as important is water volume, the amount of water produced at a given pressure. As waterjet cutting pressure increases, the size of the orifice (which actually creates the jet stream) must decrease in order to allow the pump to keep up with that volume of water and pressure. By increasing the pressure you lose volume and thereby are limiting the value of that pressure.
Another misconception with waterjet cutting pressure is that you need more pressure to cut thicker. That is simply incorrect. An abrasive waterjet cutting system operating at 40KPSI can cut the same materials to the same thicknesses as a machine operating at 90KPSI+, it only does it slower.
Hyperpressure Vs. Normal Pressure
Normal pressure in waterjet cutting is still a very high waterjet cutting pressure. Normal pressure is defined in general as 50-60KPSI. With these lower pressures you will have far less wear and tear on not only the pump's internal components but also on the high pressure water delivery system of tubing. Often users find the increased cutting efficiency obtained by running these Hyperpressure pumps at maximum pressure is offset quite quickly by operational costs, lower consumable life and a much higher HP line, orifice, head, valve, fitting and joint failures. In general a system running 50-60KSI can run for 500-600 hours of operation without need for a pump rebuild (Direct Drive and Intensifier Pumps combined) whereas a Hyperpressure pump operating at the peak pressure often can only cut for 70-90 hours without need for a rebuild.
Waterjet Pressure and Productivity
Waterjet cutting pressure does indeed increase speed, but that is not productivity. Productivity is being able to rely on your machine consistently producing quality parts in a timely manner that are within acceptable quality ranges. Productivity is making sure your machine stays operational for the longest period, is down for maintenance only when expected or scheduled and otherwise runs consistently. Pressure does not equal productivity on a waterjet cutting system but it does have a big impact on it.
How Velocity Affects Efficiency
Pressure and Velocity, although similar, are not the same. Pressure is what the pump produces whereas velocity is the result of that pressure being released through the machine's orifice. Velocity is what carries the garnet through the focus tube/nozzle and into and through the material being cut. As the orifice size changes the velocity of the pressure being released changes as well. Typically the smaller the orifice the higher the velocity, but the stream is limited by that orifice size in how much garnet (which does the actual cutting) can be carried along with the jets stream.
Increasing Water Velocity by Increasing the Pressure
As waterjet cutting pressure increases, with all the other factors the same, the velocity of the stream leaving the nozzle increases as well. As the velocity increases the linear cutting speed increases as well cutting the same material to the same tolerances and finish.
Setting Your Equipment Up for Optimum Waterjet Cutting Pressure
The optimum pressure is the pressure your machine is most efficient and productive with . For some systems this may be 40K PSI whereas most hover around the 55KPSI range. Users with Hyperpressure pumps report their best efficiency is not at the 90KPSI range as stated but rather at the lower pressures of 65-68KPSI as at these pressures the pump seals and other internal components last much longer allowing the machine to cut quality parts without unplanned failures.
Waterjet cutting pressure is set one of 2 ways depending on the type of high pressure pump you are running. For those using a Direct Drive style pump, common on Omax machines and some Flow models, the pressure is set by simply controlling the RPM of the pump motor.
For intensifier style pumps, the water pressure is set by controlling the hydraulic oil pressure being created at a ratio of 20:1 (3KPSI of Hydraulic Oil Pressure = 60KPSI of Water Pressure). Simply dialing the hydraulic pressure control valve down or up controls the corresponding output water pressure.
Ready For A Waterjet?
If you're ready for a waterjet or waterjet accessories contact the team at Southern Fabricating Machinery Sales to guide you through the options and recommend the right machine and pump for your needs and budget. Our team of experts are well versed on waterjet systems and accessories and can be your guide through the muddy waters of waterjet cutting.
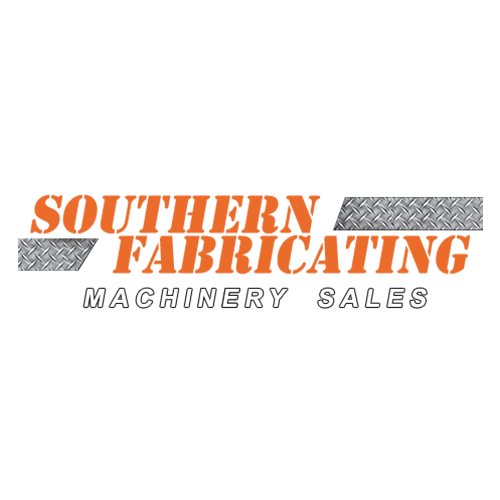