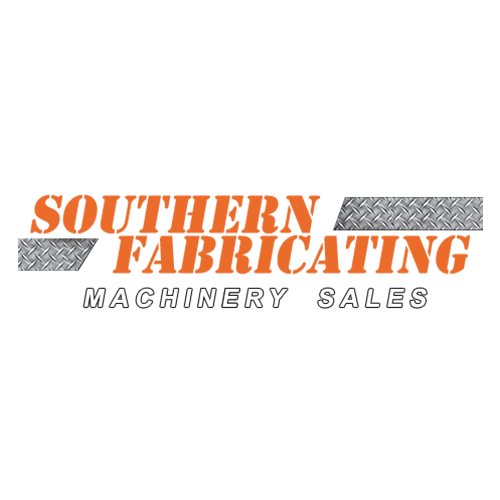
Posted By: Southern Fabricating Machinery Sales | Posted On: October 25, 2018
How to Improve Machine Accuracy
In many manufacturing applications, precision is of the utmost importance. The parts tolerance—the “margin for error” allowed in the dimensions of a given part—for certain applications can be incredibly minuscule. For example, in the aerospace industry, the parts tolerance for a particular component may be +/- 0.001” or less for safety reasons. In other industries, a variance of 0.01” may be enough to make it so the parts required to make a finished product don’t mesh properly.
Machine accuracy plays an enormous role in determining the parts tolerance of a completed product. Unfortunately, the accuracy of a machine may degrade over time as it is used—or an improperly-set up machine may create severely distorted parts. Because machine accuracy is so dependent on how manufacturers set up and run their machines, few (if any) fabrication machinery manufacturers will guarantee the accuracy of completed parts. Instead, they typically guarantee positioning accuracy, which is not the same thing.
Failing to meet parts tolerances can be a major problem—resulting in rejected orders and a loss of business as customers seek out alternative companies that can meet their parts tolerances.
The question is this: “How can you improve milling machine accuracy so your completed parts can meet tight tolerances?”
Here are a few things that you might want to keep in mind when trying to improve machine accuracy for your fabricating equipment:
Machine Epsilon and Rounded Calculations
One of the biggest issues in making a part is dealing with the math. Calculating irrational numbers, such as π (pi), and rounding real numbers for the computer calculations that run CNC machinery to ensure consistency in machine motions can be a tremendous headache, and difficult to accurately represent in a design document.
Machine epsilon is the mathematical term for the boundaries of the relative error that can be caused by rounding numbers in a calculation. For example, when calculating the circumference of a circle, many people round pi to the nearest hundredth place and leave off the rest of the irrational number. While easier to calculate, this makes the final calculation less than perfectly accurate, to say the least.
Machine epsilon helps notate and measure the effect of rounding errors, which can be invaluable for predicting the variance in round or cylindrical parts where π-based calculations are necessary. Learning about mathematical concepts such as machine epsilon is a must for manufacturing complex parts.
Maximum Work Envelope
Trying to work with parts that are at the extreme edge of a machine’s capacity can have an adverse effect on CNC machine accuracy. As noted in one Modern Machine Shop article, a machine may be “able to hold tolerances within a specific area of the work envelope, but when the machine is cutting at the outer reaches of this area, features in this vicinity on the large part are not produced to tolerance.”
This could be caused by flaws in the “volumetric accuracy” of a machine that are not noticeable when working on small parts but are more obvious when the machine is stretched to the limits of its work envelope.
Discovering the edges of this safe work envelope may require some experimentation with your milling machine, with the manufacture of parts at different positions throughout its manufacturer-approved work envelope to see what, if any, changes there are in part accuracy.
Tool Positioning and Deflection
Another reason that milling machine accuracy may suffer is that the tooling used to shape a part may deflect when it comes into contact with the workpiece. This may happen if the tooling isn’t properly secured, or if the apparatus holding the tool is extended too far from its anchor.
For example, operators of boring mill machines often keep the spindle short so it doesn’t project too far from the headstock. This increases the stability of the spindle, making it less likely to deflect when the tool comes into contact with the workpiece.
Keeping an eye on how a tool is positioned, and reworking the positioning of a tool, can help you improve milling machine accuracy on future projects as you become more familiar with the limits of a machine before tool deflection becomes an issue.
Machine Accuracy and Maintenance
Maintenance has an enormous impact on CNC machine accuracy. After all, a tool with rusty joints that haven’t been maintained cannot complete smooth motions consistently. A lack of lubricant for cutting tools can lead to tooling and parts overheating—creating irregularities in a cut. If the grit lines on a waterjet cutting machine are clogged, the grit may not flow properly into the cutting stream, which may leave a cut unfinished.
When investigating the cause of reduced machine accuracy, be sure to conduct a thorough inspection of the machine. In fact, such inspections are also useful when buying used machinery since they help you verify that you’re getting a quality machine tool.
Need help finding a top-quality piece of manufacturing equipment for your shop floor—one that will meet your parts tolerance requirements? Contact the experts at SFMS today to leverage our extensive network of contacts and put yourself one step closer to finding the ideal machine for your shop floor.
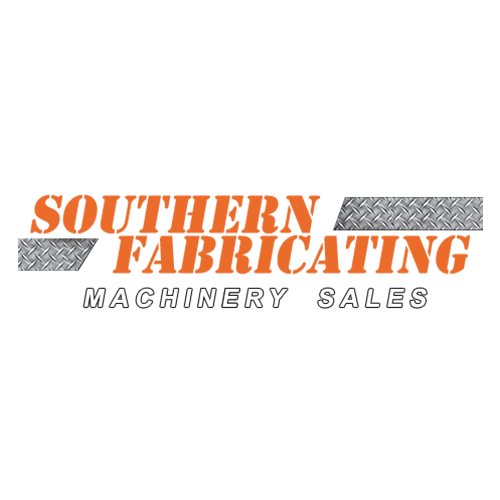