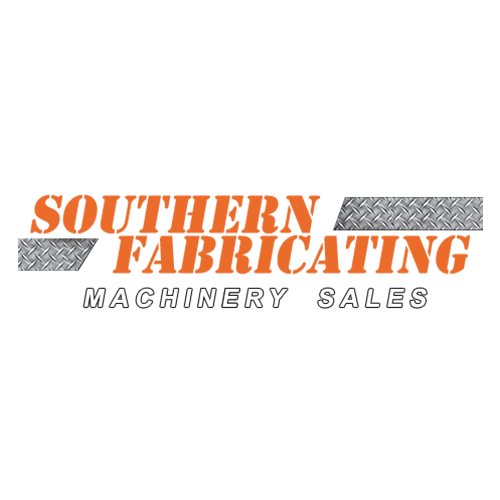
Posted By: Southern Fabricating Machinery Sales | Posted On: February 21, 2020
Tube Processing: Why Cutting & Forming Integration is Critical
Processed tubes are an essential component for most of the things we utilize in our daily lives. Whether you are plowing a field, working out at the gym, or relaxing on your couch, you are probably using some form of tubing. Processed tubes and profiles are utilized in various industries, including architecture, automotive, furniture design, and commercial vehicle
construction, among others. However, do you know how tubes are made to assume various shapes and sizes? This is achieved through the process known as 'tube processing'.
What is Tube Processing?
Tube processing is a general term used to refer to all the operations that occur after tubes are formed or rolled. The processes may include everything from specialized procedures such as swaging or some typical activities that you may be aware of, such as cutting, trimming, punching, and bending. This process is also responsible for the manufacturing of
complementary parts that go with tubes, including pipe sections, spacer sleeves, wire-end ferrules, rivets, crimp sleeves, and straight-length tubing material.
Traditionally, tube processing was done in various steps using methods such as roller extrusion, gas welding cutting, abrasive wheel cutting, hand saw cutting, and sawing machine cutting, among others. However, with the advancement in science, technology, and industrial manufacturing, many stakeholders have adopted new tube processing techniques such as laser-assisted processing of tubes and profiles.
Laser-assisted tube cutting involves the use of an energy emission device to focus concentrated streams of photons onto a tube to curve and cut out precise designs. Since lasers are computer-controlled, they provide an almost unlimited manufacturing spectrum for tube components and unique design possibilities.
A tube laser system is one of the newest fabricating processing machinery, which helps manufacturers make all types of cuts, whether it is rectangular, extruded, round, square, structural, or roll-formed shapes.
Advantages of Laser Cutting for Tube Processing
1. Efficiency
The use of laser cutting in tube processing helps eliminate the need for several downstream manufacturing steps and engineering jobs. This is accomplished through the simplification of welding setups and operations. This makes laser cutting more cost-effective, reliable, and less prone to errors.
2. Unmatched Precision and Edge Quality
Laser cutting provides outstanding precision levels and top-notch edge quality, more than plasma cutting and other traditional cutting methods. And since computer programs control laser processing machines, they can cut with accuracy and ease around and through the radius of any tube. This is one thing that is impossible to achieve with traditional cutting pieces of equipment.
3. Speed and Cost-Effectiveness
Unlike other techniques, laser technology allows manufacturers to cut complex shapes without the need for tooling, and at a quicker rate than ever. The laser technology delivers speed and accuracy required to meet projected output and quality standards. Research indicates that laser tube cutting can save up to 49% of the time needed by traditional methods. It also lowers expenses by up to 30% when compared with conventionally welded parts. Its ability to make complex contours, perforations, and cut desired strengths in simplified steps helps eliminate the costs associated with operations such as storage, toll changes, and parts handling.
4. Makes Parts Assembly-Ready
Laser cutting machines can create holes, tabs, and grooves that allow the cut stock to be assembled by bending it into the appropriate shape. This helps eradicate the need to have a complicated jig in place to join the various separate pieces into one final part. It ensures that manufacturers deliver self-aligned parts that are ready for use.
5. Cuts a Wide Range of Materials
Laser cutting technology can cut tubes made from different materials, including rubber, plastic, and metals. They can also be optimized and designed to cut through thick plates. Some of the latest laser fiber machines can cut through thick materials.
Integrating Tube Processing Steps In many cases, tube processing involves a myriad of steps. And even though laser technology has helped reduce some of these steps, more integration is needed. For starters, the merging of the laser cutting system with computer numerical control software can lead to the creation of an efficient automation machine. This will open a new path to improved efficiency, high quality, and low-cost processing.
Therefore, for improved efficiency, manufacturers should opt for a laser cutting automatic production line. For manufacturers to achieve an automatic product line, the laser beam must be focused in a way that it runs synchronously with the tubes. This means that the laser beam will be moving together with the pipe being cut.
As we look ahead, new developments in tube processing integration will likely involve simplified assembly steps. It is unlikely that manufacturers will try to tie together complex assembly operations. However, there is a possibility that these operations will continue to occur in an integrated work-cell. Integrating tube processing steps will allow for maximized throughput and ensure that the only human intervention will be in handling incoming and outgoing materials.
At Southern Fabricating Machinery Sales, Inc we know Tube Cutting and Tube Forming. Call us at 1-813-444-4555 to discuss your application, or contact us via the link below for more information on how we can assist you in your Tube Processing needs.
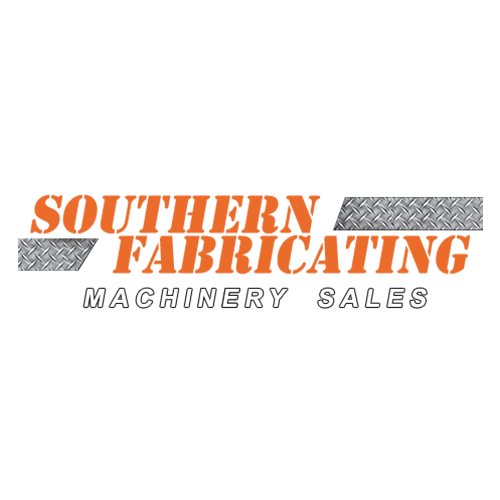