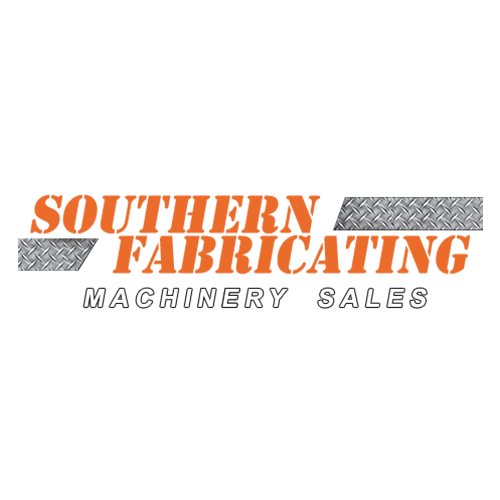
Posted By: Southern Fabricating Machinery Sales | Posted On: December 27, 2019
5 Things You Need to Know Before Buying a Waterjet
What do you need to know before buying a waterjet cutting machine? Well there's quite a lot actually. First off DON'T automatically expect the large brands to have the right solution for you. Second, DON’T get oversold on options and features you don't need. Third DO make sure you discuss and decide what you need BEFORE you set out looking for a machine. Knowing these basic DO’s and DON’TS can save your tens of thousands of dollars and years of frustrations.
So what do you really need to know before taking the plunge (pun intended) into waterjet?
- It’s Messy - Waterjet cutting uses an abrasive media (Garnet) Mixed with High pressure water to grind through material. The result? Garnet particles + metal grindings + water = a sandy muddy mess. But….
- It’s Easy - Throw material on the table, position the nozzle and start the cut. Any material, any thickness. But….
- It’s Expensive - At an operating cost of roughly $30 per hour waterjet is at the upper echelon of the shape cutting machining processes (see: Waterjet Capabilities: Where Waterjets Fit). But….
- It’s Versatile - Waterjets can cut any material to close tolerances with minimal setup and little to no program expertise easily offsetting that operating costs with profits in the $150 per hour and + range.
What Size Machine Do You Need?
Choosing the waterjet size you need is a little but tougher than it seems. Often we choose a machine based on systems price, floor space available or the part sizes we currently make, but don't consider the fact that the material must all be purchased in larger sheets or we have to pay a premium for the material to be sheared down to size. Deciding from the start that a 2X4 or 4X4 machine is the way to go may be a tragic mistake very early on as most users really need a 5' X 10' machine or bigger.
Consider this: Manufacturing a machine tool requires a system of controls, drives, servos, rails, gearboxes etc. These components are all very much the same on a 2’ X 4’ machine as they are on a 6’ X 12’ system. In fact, building a larger system costs only a few thousand more in materials and labor compared to a smaller system (if you are comparing systems like cheap imports vs quality domestic produced systems your not considering the same quality). Although manufacturers list these larger machines at much higher prices they also have much more profit, and thus room to negotiate in them as well.
Conclusion: Choose the right system for your parts, supplied material AND growth potential. Remember too that a finance plans can allow for the right machine and still meet your budget. Typically a 5’ X 10’ or a 6’ X 12’ machine are the best choices.
Do I need that Taper Compensation Head?
Taper compensation is one of the biggest misnomers out there in waterjet. Does it work, yes, by tilting the jet stream prior to entering the material the slight taper in the waterjet edges can be shifted into the scrap material leaving a straight edge on the part surface. However the same can be achieved by slowing the cutting speed down which also improves the surface finish which is very likely also a desired quality and eliminates a very costly and heavily maintained option.
In order for taper compensation to work correctly the material needs to be absolutely flat (think trigonometry …..jet stream entering the material at an angle, correct part size etc.). Further you now have to build a complex secondary motion system around the cutting head allowing for tilt, rotation and lift as well as a surface probing system in order to accurately measure the material surface prior to cutting (remember that trigonometry thing?). These additional 3 axis (plus the probe) add complexity to the machine design and add sensitive motion components directly in the cutting zone. Damage often occurs to these Taper Compensating heads from material tip ups or inadvertent operator errors causing costly downtime and expensive repairs likely when you least need it. Also components are often damaged by the operating condition inherent to waterjet. Over time it is not uncommon to see Frozen Probes and Axis overload errors due to the corrosion and build up of abrasive waste material.
Conclusion: Taper compensating heads should be considered ONLY if your have a steady type of work that requires the feature and NOT just as an added benefit your sales rep offered.
What about these Ultra High Pressure Pump Systems Are they Worth it?
Waterjet technology has significantly increased over the years like many things. Buoyed by new engineering, new materials and years of testing, pump pressures are now exceeding the 100KPSI mark. While these ultra high pressures DO provide a considerable increase in cutting speed they, as with anything else, do so at a cost. First the cost of these ultra high pressure pumps can be significantly higher, 50-100% or more. Second the components required to deliver that high pressure to the cutting head all have to be of much higher quality and as such, higher cost. Lastly the maintenance required is much more frequent as components wear down, or simply fail without warning in a fraction of the time at these ultra high pressure.
In real world applications we find many users dial these Ultra-High Pressure pumps back to manageable pressures in the 60-70K range mostly to prevent premature damage to internal components but also to extend seal life. As we see time and again these pumps being operated in the same manner a 60KPSI unit, it is clear that the users were oversold on the Ultra-High Pressure without taking all things into consideration. Although pressure does indeed increase speed, Horsepower does as well and in abrasive applications the more HP you can throw at the nozzle the better performance you'll receive in cut speed, performance AND longevity of components.
Conclusion: Choosing an Ultra High Pressure Pump should be a carefully thought out choice over just a higher HP 60KPSI option that is a proven performer. Determining the maximum power you have available for your waterjets pump first can be the best way to determine how much HP you can efficiently run.
Do I need to Recycle the Water?
Water Recycling Systems have been oversold in many cases. While they do provide for the ability to have a ZERO discharge system they do so at a cost of anywhere between $7-9 per hour quickly negating any water usage savings (Note: water is the cheapest component of waterjet cutting). These systems have Several Pumps, Weir Tanks, Staged Filtration, DI Resin Containers and a Chiller all which must be maintained and in peak performance in order to get the waterjet operational.
Many times we see these systems offered used after just a few months operating on a machine as they are much more maintenance heavy and provided little advantage or benefit to the user then were initially disclosed. They are often packaged in with a waterjet system and the novice buyer is unaware of the overall operational costs and maintenance required. As these can be added onto the system at anytime
Conclusion: Choose a water recycling system ONLY if your County/City require you too as these can ALWAYS be added in later at no additional cost.
Can I Recycle the Abrasive?
Yes absolutely the abrasive can be recycled, right to the landfill, and your knowledgeable sales rep will encourage you to do so. Fun aside, there are Abrasive recycling systems available on the market that promise to recapture 30-40% of your spent abrasive or more. As the abrasive is your most expensive consumable these systems may be attractive, initially. Just like the water recycling systems they also come at an enormous operating cost (think heaters, filters, pumps, weir tanks, dust collector, etc, etc) and are heavy on maintenance (shaking all that grit down wears out the internals quickly). Lastly these systems seem to only provide value where multiple waterjets exist and many times even in those scenarios we see them often set aside very shortly after initially purchased.
Conclusion: Abrasive Recycling Systems never are warranted as their initial system cost, operating and maintenance expenses far outweigh the cost of fresh abrasive.
Should I get an Abrasive Removal System?
Abrasive Removal Systems promise hours, even months of unattended operation. There are mobile systems that can vacuum out the tank through a suction tube moved around and there are systems that are built right into the machine tank. Either of these types of abrasive removal systems can keep the system relatively free of abrasive BUT do not prevent at least an annual tank cleanout. Scrap parts, drops, and miscellaneous material drops into the tank and do not get removed by these abrasive systems at some point will need to be cleared out by hand.
Like the water recycling systems these can be added at anytime during the operation of your machine without any additional investment other than your time to plumb in the connections. While they can be a great addition to any waterjet system it is recommended that you take the “wait and see” approach before dropping an additional 15-30K or moire into a complete closed loop abrasive system.
Conclusion: If you know you need an abrasive removal system there are many available both aftermarket and from your machines OEM. Take a look at what's available BEFORE deciding on an expensive in-tank dedicated system.
In Summary:
- Choose the right system for your parts, supplied material AND growth potential. Remember too that a finance plans can allow for the right machine and still meet your budget. Typically a 5’ X 10’ or a 6’ X 12’ machine are the best choices.
- Taper compensating heads should be considered ONLY if your have a steady type of work that requires the feature and NOT just as an added benefit your sales rep offered.
- Abrasive Recycling Systems almost never are warranted as they system cost, operating and maintenance cost far outweigh the cost of fresh abrasive.
- Choosing an Ultra High Pressure Pump should be a carefully thought out choice over just a higher HP 60KPSI option that is a proven performer. Determining the maximum power you have available for your waterjets pump first can be the best way to determine how much HP you can efficiently run.
- If you know you need an abrasive removal system there are many available both aftermarket and from your machines OEM. Take a look at what's available BEFORE deciding on an expensive in-tank dedicated system.
At Southern Fabricating Machinery Sales, Inc we pride ourselves in having the best working knowledge of waterjet machines and all the accessories and systems associated with them. We can help you make the right decision the first time on your waterjet system, options and accessories whether you're buying a new or a great repurposed machine with us. Visit us on the web to learn more about the waterjet systems we offer or call us directly at 813-444-4555 to discuss your needs in detail.
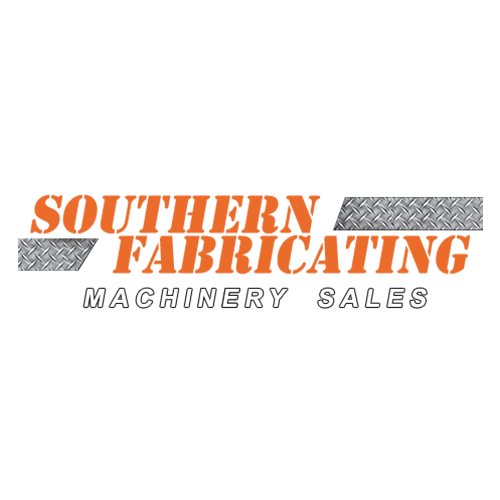