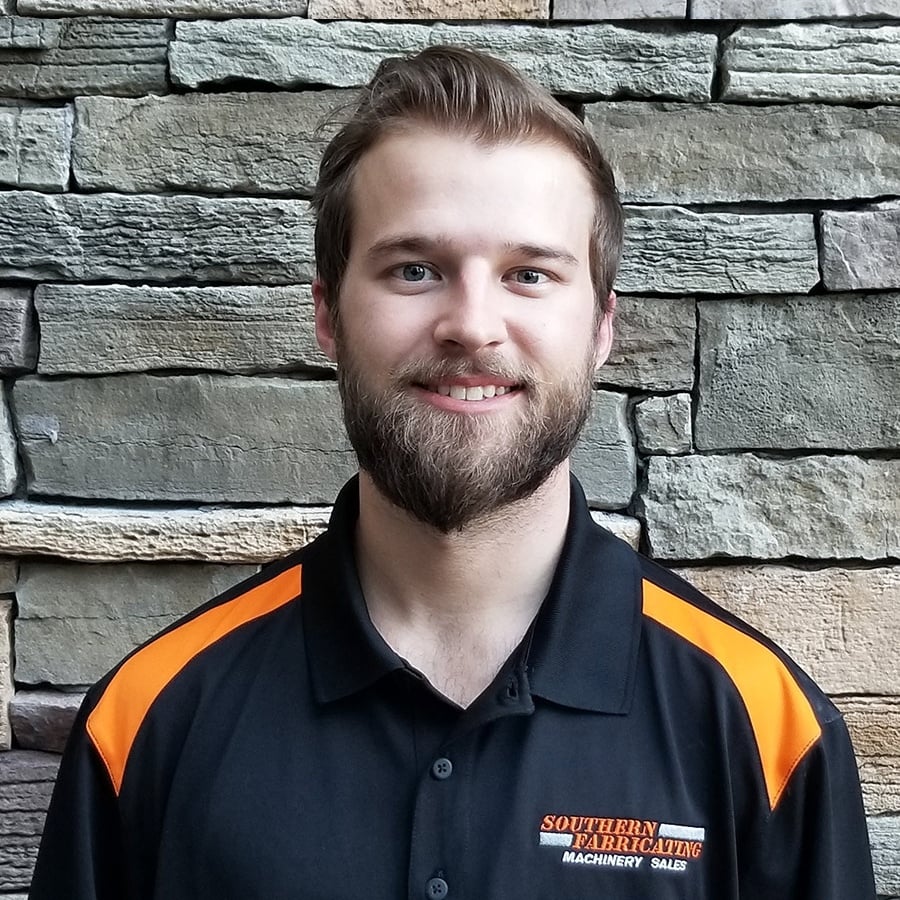
Posted By: Dylan McCarty | Posted On: April 5, 2018
A Look into the Different Types of Fabrication Machinery
Let's start off by saying that I understand that you, as the reader, likely do not want to read a 20-page blog covering every individual type of fabrication machine out there. On our website alone, there are 14 types of machines under our “Fabrication Machinery” tab in the “Machinery for Sale” section. It would be overkill to touch on each one individually.
If you are running a machine shop, you probably don't have that kind of spare time available. As such, I’ve decided to write about the five most commonly used types of fabrication machines found in almost every machine shop today:
- Waterjets,
- Press brakes,
- Laser systems,
- Plasma systems, and
- Shears.
Waterjets
Waterjets are, by far, the most useful and cost-efficient method of cutting a variety of materials. These industrial machine tools use a combination of water and an abrasive substance to cut virtually anything, including:
- Stainless steel,
- Carbon steel,
- Aluminum,
- Titanium,
- Plastics,
- Copper,
- Brass,
- Rubber,
- Glass,
- Ceramics, and
- Stones like granite and quartz.
These machines are so versatile because almost no heat is generated to the workpiece — unless, of course, you’re cutting steel that is at least two inches thick, which can cause temperatures to reach 120 degrees F.
Waterjets work by using high-pressure pumps, which reach speeds of anywhere from 30hp to 100+ hp, to force water out through the nozzle (commonly referred to as the “head”) to cut your material. Almost all jets have an “abrasive hopper system.” This feature incorporates a metered flow of granular abrasive, usually garnet, to aid in cutting the aforementioned materials.
Whether you are considering opening your own machine shop, or you’re looking for that perfect machine to give you an edge to help your existing business grow, a waterjet is the best and most versatile machine to invest in.
Press Brakes
“Old Reliable” should be stenciled on the side of every press brake in the world. Press brakes are, without a doubt, the sturdiest, strongest, and most dependable bulls in the pasture. It is common when searching for used press brakes to find many of the top brands like Amada and Cincinnati with vintages from the 60s and 70s still kicking and in great condition. This is because press brakes have only one function: bending metals.
Press brakes have a simple operation: Secure the workpiece on the bed and the ram will descend upon it, using its tonnage to accurately bend the metal to the specified degree. The different types of metals commonly fabricated by these machines include steel, aluminum, brass, and sheet metal. Press brakes are rated by their pressing capacity (tonnage) and the bed length, which dictates the overall length of your workpiece that can fit in the bending zone. Tonnage capabilities range anywhere from 25 tons all the way up to 1,000 tons. The smallest bed lengths start at four feet, whereas the longest beds can reach a length of almost 30 feet.
There are four types of press brakes:
- Mechanical,
- Hydraulic,
- Pneumatic, and
- Servo-electric.
The two most common brakes used in nearly all contemporary machine shops are mechanical and hydraulic. Mechanical brakes dominated the industry until the 1950s when advances in technology introduced computer controls. This made the hydraulic brakes much more popular and user-friendly.
If you have lower tonnage requirements, mechanical brakes should be at the top of your list of machines to invest in because they are simple to maintain and will not break the bank. If your shop is bending very thick metal, you will need higher tonnage capabilities. In this case, go with a hydraulic press brake. It’s the most powerful and efficient type of machine for larger jobs using thicker metals.
Laser Systems
Laser cutting systems are quite advanced. The most common applications that lasers can be used for includes:
- Cutting,
- Welding,
- Marking, and
- Surface treatment.
Industries with high demand for these operations are usually ones that require high precision for cutting complex parts. These include parts for automotive, shipbuilding, aerospace, steel, electronics, and medical industries.
Laser systems work by using thermal energy to remove material from the workpiece by melting, vaporizing, burning, or blowing it away. This leaves a high-quality surface finish that is critical to the success of the finished product as a whole. During operation, Computer Numerical Control (CNC) technology directs the laser head to move about the workpiece, cutting the desired shapes with an accuracy of up to 10 micrometers on newer machines. This cutting process maintains very tight tolerances — often within .001 of an inch.
If you are on the machining side of any of the previously mentioned industries, you know there is zero room for error. These machines make that level of precision possible.
Plasma Systems
While it might seem fictional, plasma is actually a common and widespread method of cutting certain materials. But, unlike some of the aforementioned cutting methods, the “certain materials” that can be cut using plasma must be electrically conductive — such as steel, aluminum, brass, and copper.
Plasma cutting systems use an accelerated jet of extremely hot, electrically ionized gas (plasma) to form an electric channel from the cutting head through the workpiece, and then back to the cutting head. These fabrication machines can be found in a number of different operations because they are fast, precise with their cuts, and are relatively inexpensive to operate.
Companies that benefit the most from this particular cutting process tend to vary from large industrial manufacturers that need to make the same cut hundreds of times to small hobbyist shops that create metal art from recycled pieces.
Shears
Shears are one of the cheapest, simplest, and most common machines on our list. These machines do exactly what you think they do: cut metal. Typically used for cutting sheet metal and aluminum, shears can also be found in places other than machine shops that cut paper, plastic, and wood.
With regard to metal thickness, shearing capabilities can range anywhere from the smallest gauges (thinnest material) all the way up to workpieces that are an inch thick. Whenever machine shops place an order for more material — whether it be mild steel, aluminum, brass, etc. — it will usually arrive in sheets. You can bet that wherever that shipment came from, those sheets were formed by a shearing machine. Shears are the backbone of the metal forming world.
There are many more types of fabrication machines out there that are crucial to certain industries and have capabilities that the machines on this list cannot perform. However, you can bet that wherever one of those unnamed machines is being used, there also is a waterjet, press brake, laser, plasma or shear in the same shop sitting nearby.
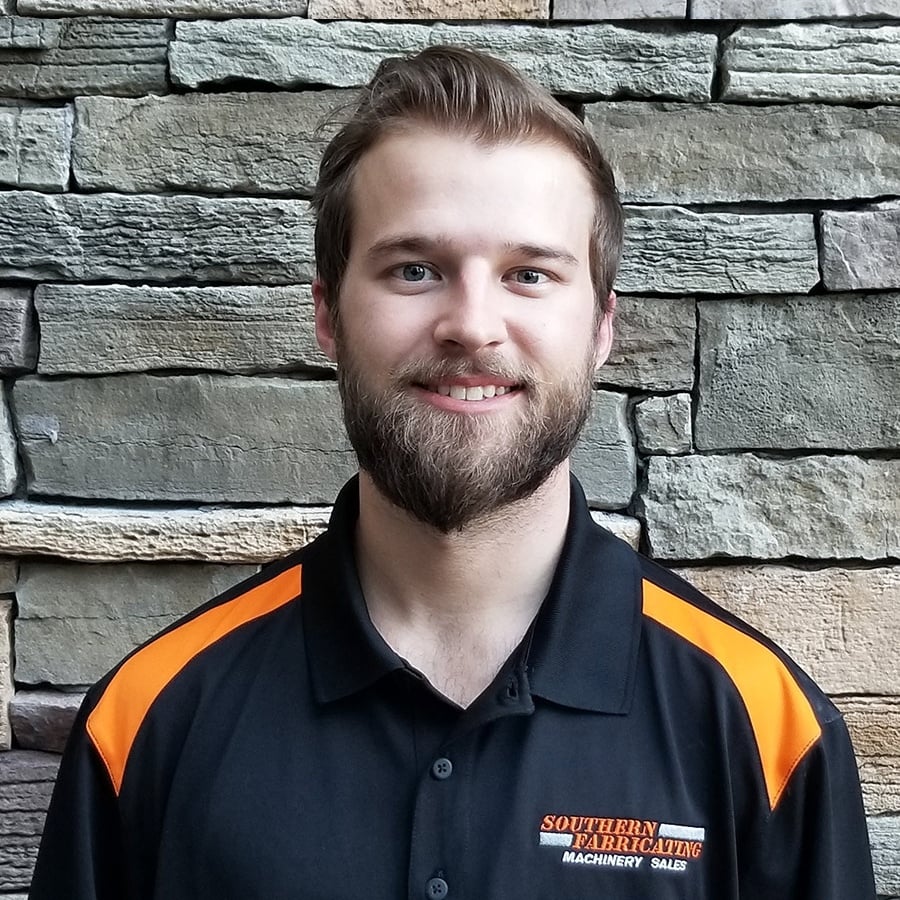
dylan@southernfabsales.com | 813-444-4555 x113