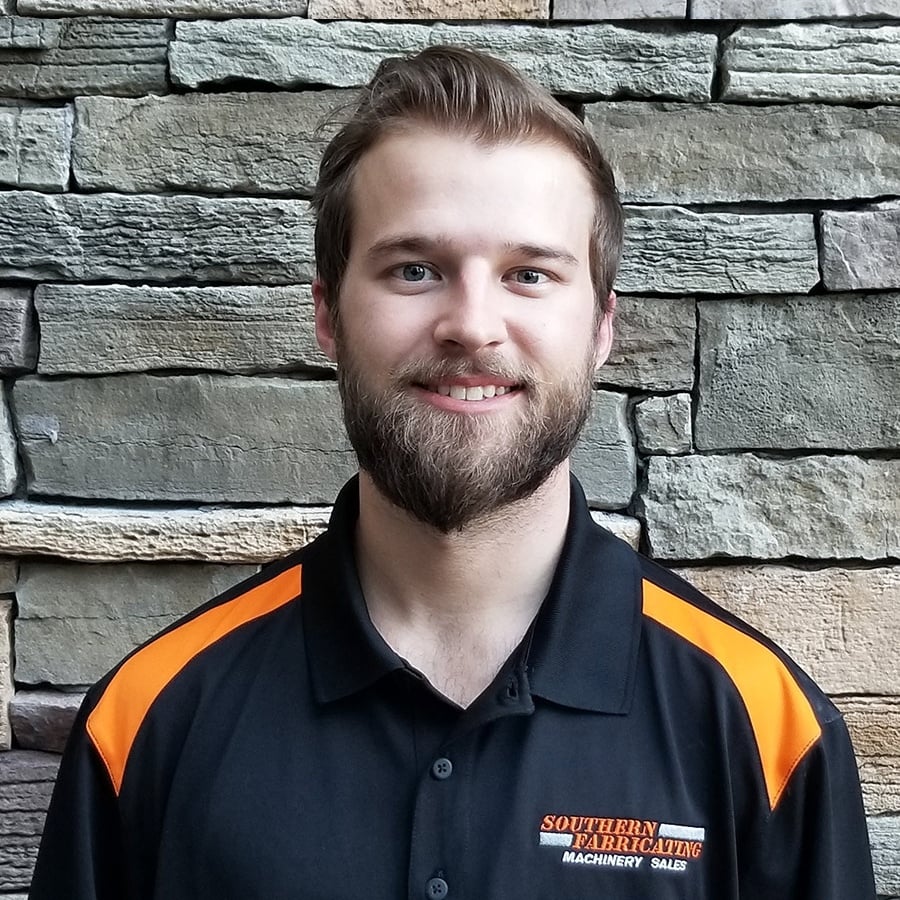
Posted By: Dylan McCarty | Posted On: February 27, 2018
5 Factors to Consider When Buying Plastic Injection Molding Machinery
As many of us in the machine industry are aware, Plastic Injection Molding is just as relevant and important as any other machining process. There are many things to consider when considering purchasing plastic injection molding equipment, such as: Shot Size, Tie Bar Spacing, Ejector Stroke, Platen Size, and Tonnage.
Shot Size
Shot size is best defined as the maximum amount of plastic that the injection molding machinery is capable of injecting into the molding cavity during one molding cycle. The amount is rated in ounces of “general purpose polystyrene” (GPPS) for U.S. machines, and cm3 for European and Asian machines.
When searching for a machine, it's always a best practice to look for a machine that is capable of producing 30-40% greater shot sizes than what your parts require.
Tonnage
In this case, I mean “clamp tonnage or clamping pressure.” This could be considered the same concept as when you're examining press brakes. With press brakes, tonnage capabilities are measured by how many tons of downforce the machine is capable of directing towards a workpiece. However, with plastic injection molding machines, tonnage is measured by how many tons with which the machine is capable of pressing together the platens, which hold the mold cavity and form the plastic that is injected into said cavity to produce the desired part.
Platen Size
The platen is the "table" or tool that holds the mold cavity. Spaced apart, the mold is inserted and clamped securely to the platens. Once the two platens come together and are held under the pressure of tonnage, the plastic is heated, injected under pressure, and then allowed to cool through a molding cooling cycle. Here, the plastic takes on its hardened, final shape while continuing to be kept in place with many tons of pressure to retain the desired shape.
Tie Bar Spacing
Tie Bar Spacing is defined as the space between the horizontal tie-bars on an injection molding machine. Basically, this measurement, along with the platen max spacing, determines the maximum size of molds that can be placed in the molding machine.
Ejector Stroke
Simply put, Ejector Stroke is the action of the machine pushing out (ejecting) the final workpiece from the platens using ejector pins. The ejector in the molding machine pushes against an ejector plate on the mold, Ejector "Pins" or rods are attached to this plate and perform a pushing operation on the molded part after the plastic has hardened and the mold has opened.
Once the action of molding the workpiece is completed, the mold opens and then the ejector pins slowly extend outwards, pushing (or ejecting) the finished part out of the mold cavity. Pin movement is timed with the mold opening—because pins that move too quickly could impact the plastic workpiece and damage the final product and pins that move too slowly may not fully eject the molded part.
At Southern Fabricating Machinery Sales, Inc. we have many Plastic Injection Molding Systems available and can assist you in selecting the right system for your part or application. Also, with equipment appraisers on staff we can help you evaluate and sell any excess plastics machinery you may have. Please call me directly at 813-444-4555 X113 to discuss your machinery needs.
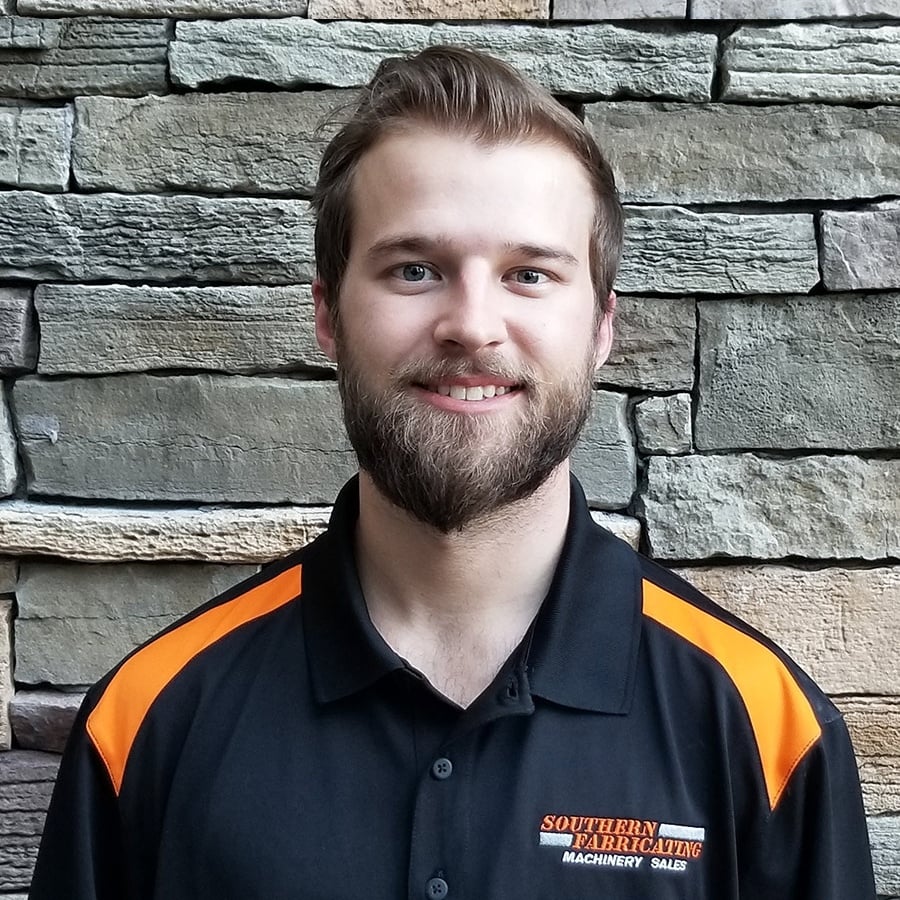
dylan@southernfabsales.com | 813-444-4555 x113