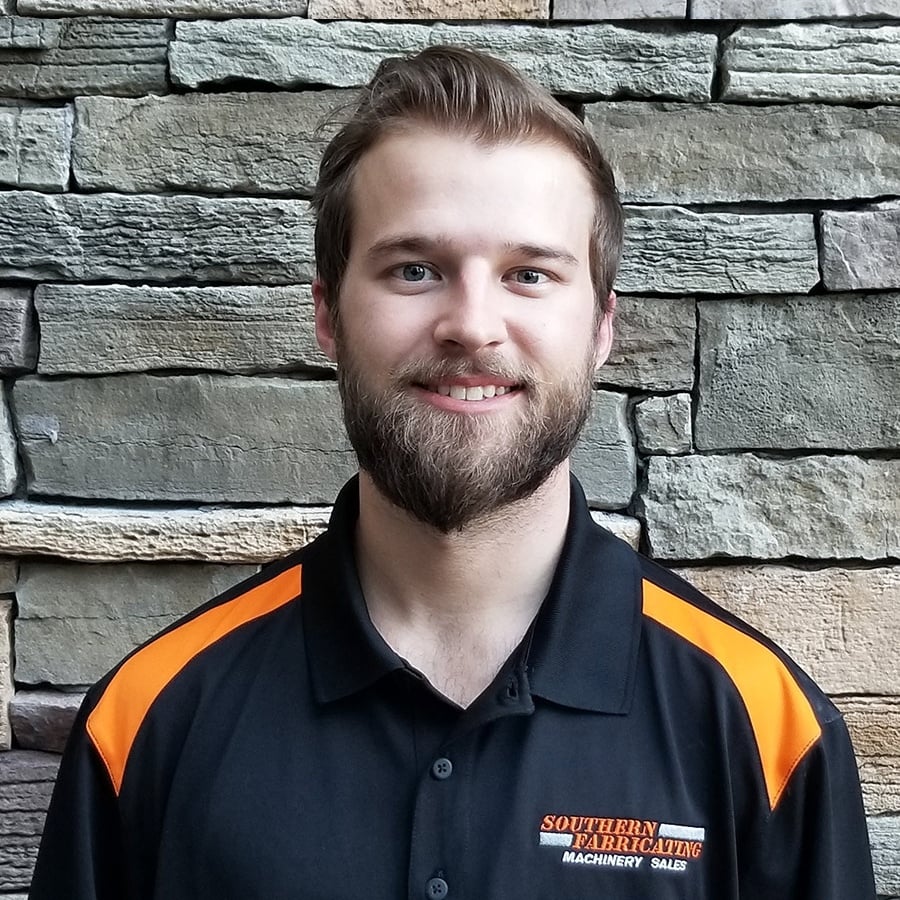
Posted By: Dylan McCarty | Posted On: September 18, 2018
Best Machines to Make Blow Molding Products
In this article, we are going to put the process of blow molding for producing plastic parts under the magnifying glass and identify the best machines to use for this process. This piece is intended to help end users make the best decisions when in they’re in the market for a Blow Molding Machine based on the type and/or shape of the product they’re making.
How Blow Molding Works
First, let's review the blow molding process as a whole. Blow molding is a specific process by which hollow plastic parts are formed. Much like blowing up a balloon, plastic materials are heated and then filled with air to force them to conform to the shape of a mold. Hollow glass products like bottles are also formed this way, but let's just stick to plastic for now.
The process usually begins by injection molding: melting down the plastic and forming it in a mold, what is called a “preform.” After preforming the part, it is transferred to a blow molder wherein the part is mounted in another mold or “injection case,” heated to soften the material again, and then has air blown into it—pushing the now soft and elastic plastic outward to match the “mold.” The mold is basically the final shape of the desired part.
The two main types of machines that perform this process are extrusion blow molding machines and injection blow molding machines. They both operate in similar ways to create your product but have different advantages and disadvantages regarding production.
Extrusion Blow Molding Machines
Extrusion blow molders melt the plastic and “extrude” it into the injection case to then be clamped together by the platens and form the desired shape. Extrusion simply means to “squeeze” the melted plastic out. Think of your tube of toothpaste. When you squeeze out a portion, you are extruding the toothpaste out of the tube. Once the plastic is molded into the shape and cooled off sufficiently, the part is then ejected and your machine is ready to start the process over again. Examples of products made through this process include milk jugs, shampoo bottles, and various automotive parts like the air intake tubing on your truck.
Advantages of extrusion blow molding Machines include low tool and die cost, faster production rates, and the ability to mold complex parts with ease.
Disadvantages of this type of blow molding include low strength of your plastic products and the fact that it is limited to manufacturing hollow parts only.
Injection Blow Molding Machines
Injection blow molding machines utilize the barrel and screw assembly that melts the plastic and injects it into a heated cavity and core pin, which looks quite similar to a test tube. The cavity mold forms the outside shape of the product and is clamped around a core rod, forming the inside of the product. It is then inflated with compressed air to match the mold and cooled. Once the product is cooled, it is then ejected and your machine is ready to begin the process again. This process is primarily used to make small medical tubes and single serving bottles.
Advantages of injection blow molding is that the finished product is more accurate, hence the focus on producing items for the medical field.
Disadvantages are that this process only suitable only for small capacity bottles and handles cannot be made (like the handle on your milk jug).
Southern Fabricating Machinery Sales has many options for machinery that fall into these categories and can help your blow molding operation be successful. For more information on the machines currently in our inventory, give us a call or check out our website today to learn more about blow molding and many other manufacturing processes.
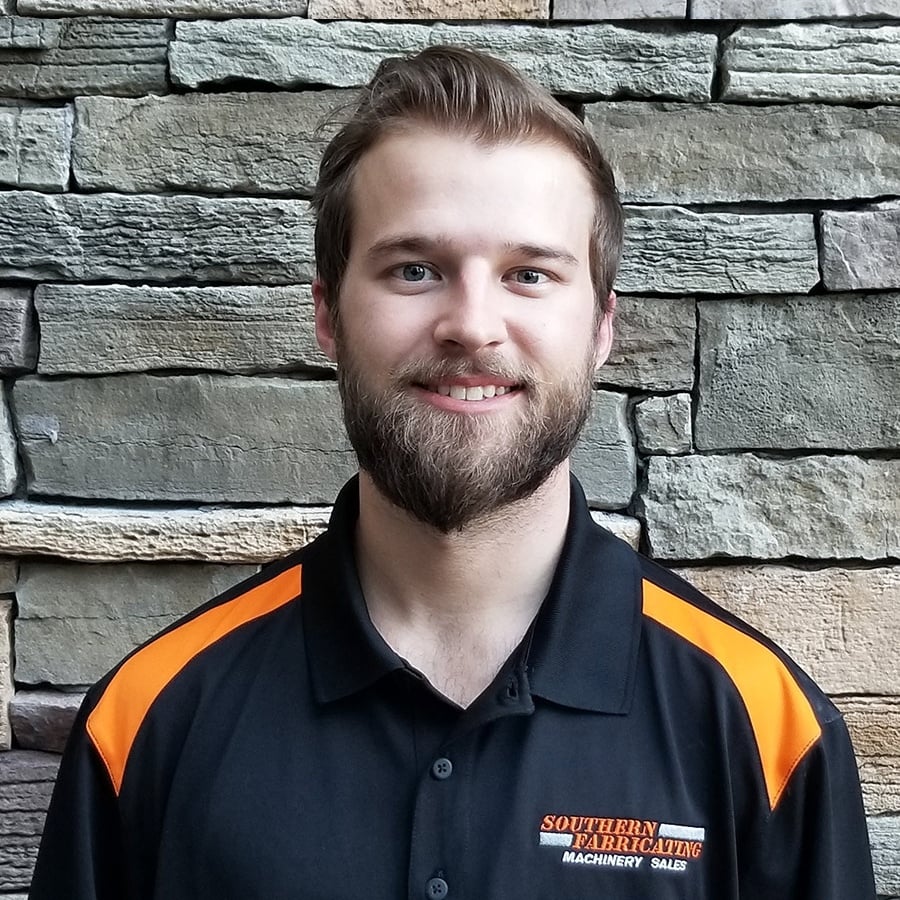
dylan@southernfabsales.com | 813-444-4555 x113