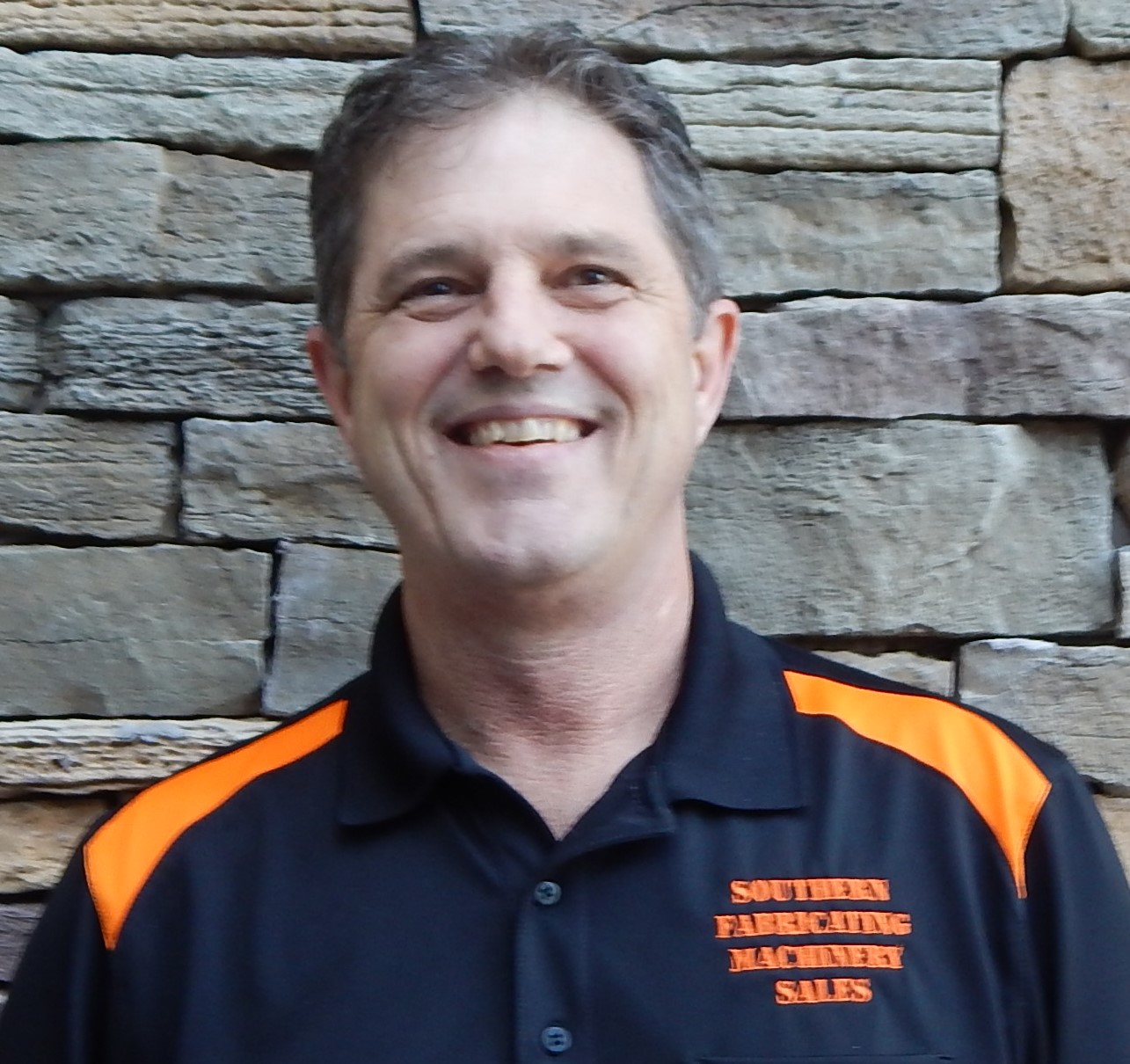
Posted By: Dave Wearing | Posted On: February 13, 2018
5 Tips to Keeping Your Electrical Discharge Machining (EDM) Center Running Properly
Keeping your shop's equipment working at peak condition is a must for maximizing productivity and minimizing disruptions. Electrical Discharge Machining (EDM) is one process that can be kept running quite efficiently if you follow a few simple tips.
1) Check and Clean the Dielectric Probe
The conductivity of your deionized water, known as dielectric, is very critical in the EDM process. Each of the generator settings used in the EDM process requires rapid electrical discharges from the wire to the part being cut. The “gap” between the wire and part is maintained by a controlled spark that erodes a small section of the workpiece causing it to melt and then resolidify in a small sphere that is flushed away. This process is repeated thousands of times in a second.
When the conductivity of the dielectric is too high or low, this will cause the gap to be inconsistent; which will affect precision and, in some cases, cause wire breakage. By checking your dielectric probe and keeping it clean, you can keep your machine's conductivity control system working properly. This should be done every 500 hours and be double-checked with a separate conductivity meter.
2) Replace Power Feed Cables
You ran your self-diagnosis and your generator is running at peak performance, but you are still not getting the speed and cut quality that you had when new! Other than your contacts it most likely can be your power cables. Not only do they supply the energy for cutting but also return information back to the generator to better control the cutting conditions. If you have a submerged cutting system, the dielectric can cause a breakdown in the integrity of the cables even sooner. Unlike a power board failure that instantly shuts your system down, power cables will lose performance gradually over time—and many are amazed at the improvement of the machines cutting process after replacement.
3) Check All the Air Filters
Your generator cabinet is one of the most expensive components on your EDM center. There are many boards with many smaller electrical elements and circuits; and they all depend on a cool and clean flow of air for optimum performance and longevity. All generator cabinets have openings, usually in the door, that holds a small filter that collects dirt and other small particles.
All shops are different—with some having a temperature control room for their EDM and others in a cell or production configuration on the shop floor. You may need to replace them monthly or yearly but, they must be replaced with new ones. Also, be sure to check the air flow direction on the filters because some have a two-part system for catching larger debris then smaller debris.
4) Check Cooling Fans
Cooling fans provide air circulation in your generator cabinet that keeps boards and other components from overheating and experienced stressed conditions that will eventually lead to failure. For example, solder joints can become brittle from too much heat, then cool off when shut down, creating micro-cracks that ultimately reduce the performance of the board and its components. By checking these fans daily on startup, you will measurably extend the life of the CNC and power supply of your EDM system.
5) Clean and Inspect Your Dielectric Tank
Last but not least is a job that is not very much fun but needs to be done at least once a year. All EDM systems have a clean tank and a dirty tank. The dirty tank collects most of the contamination before it is sent to the filtration system and then on to the clean tank. It is very important to keep the clean tank as clean as possible since this is the source of dielectric that is delivered to the cutting process and other components like your threading jet. Many small pieces of debris will, in time, find their way to the clean tank from dirty filters and/or the filter change-out procedure.
So, there you have it, 5 easy ways to keep your EDM system performing at its best and increasing your machine's efficiency and shop’s profitability.
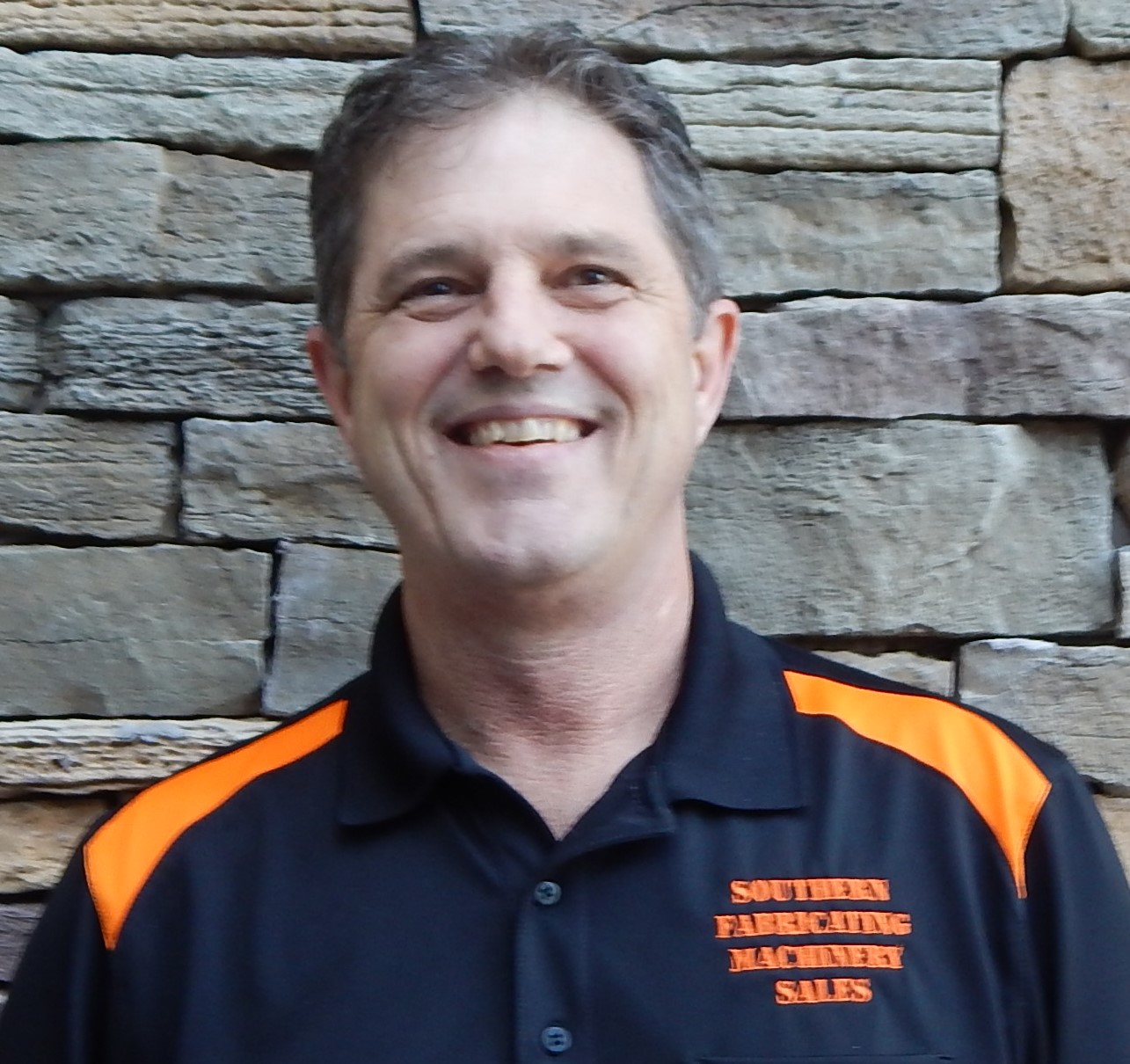
dave@southernfabsales.com | 813-444-4555 x108