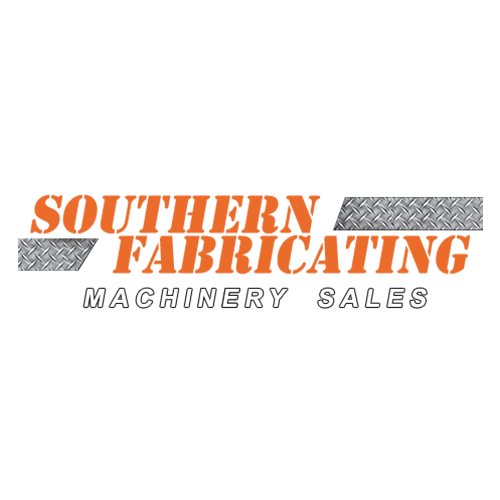
Posted By: Southern Fabricating Machinery Sales | Posted On: October 30, 2020
5 Things to Look for When Buying Used Plate Rolls
When you are deciding what type of plate rolling machine to get, there are certainly plenty of choices. You have different machines, brands, designs, and extra features. You also may be wondering if you should get new or used equipment. Truthfully, buying used equipment can not only save you a lot of money, but you can still get the exact piece of equipment you need.
New vs Used Plate Rolls: How to Identify Which is Right for Your Needs
There certainly be advantages to buying new or used plate rollers. There are many different things that will need to be considered.
Budget
Of course, your budget needs to be considered when you are looking at buying plate rolls for your fabrication shop but don’t arbitrarily set your budget without first considering the needs you have of capacity, formed shape and the best machine design that you will need. Buying used equipment can actually save you a lot of money over a new machine.
Function
Technology is ever-advancing. Depending on what you need the machine to actually do will play a large role in what type is the best suited for you to buy. If you need it to do something extremely complicated, you may have difficulty finding that in a used machine but consulting with rolling exports like the team at Southern Fab is a great way to ensure you are covering the bases.
5 Things to Consider When Purchasing a Used Plate Rolling Machine
Fabrication machines are continually advancing due to the demand for certain types of products and the technology of controller and programming systems. Machines can do more, and make more, faster and easier then ever before so it is well worth your time to investigate what is new and whether or not it applies to your individual needs. .
1) Can It Do What I Need it To?
Obviously the most important aspect of purchasing any machinery is making sure it can actually do the work you are budgeting and justifying it for. Purchasing a machine that's under capacity because it meets your budget will not do any good in the long run of manufacturing, rather it will be a hindrance to your growth. In plate rolling this means you need to ensure it can roll AND prebend the material you are working with over the full length of the roll or part..
Further you need to make sure the machine will be able to keep up with the demand for the production and accuracy you need within a reasonable timeframe. You also will want to know if there are extra features that come with it or can be added. Items like cone rolling, side supports and overhead support options are always important in plate rolling. In this case used equipment can be state-of-the-art and still not perform all the tricks you need it to however you may still be able to customize it to meet your specific needs.
2) Number of Rolls
Two, three, or four roller plate rolls can make a huge difference in what types of accuracy you will achieve and the production rate you will achieve that accuracy at.
- Two roll machines are fairly rare and limited to thin sheets and high production. Items like filter canisters, cans etc are suited for two roll machines. Often these systems are provided with auto loading and unloading features.
- Three roll plate rolling machines are the most common with several varieties of these available from initial pinch to variable angle style. These rolls offer flexibility in use and lower investment but require more material handling and careful operation to ensure the plate does not slip during the rolling or setup process.
- Four Roll Plate Rolling machines are by far more flexible and accurate at rolling just about every shape imaginable. And because they can pre-bend on both ends of the plate, there is less material handling required and that material stays fully clamped between the center rolls during the entire process providing for a more assured outcome.
Each of these designs of plate rolling machines will have their own advantages and disadvantages but whenever possible you should try to find a 4 roll machine as in the end they are much better at maintaining accuracy and reducing material handling.
Buying these used might mean you can buy more than one or find one that is programmable to do many tasks. But with technology, you can likely find a great used machine to perform all the jobs you need it to.
3) Inspect That Roll
Getting a used machine for a great deal is great but make sure there isn’t something you need to know about the machine’s history. You can check the serial number on the equipment with the manufacturer to find out some information, but often the manufacturer won’t be able to tell you much. Manufacturers don't know how the roll was used, what repairs were made (only parts ordered from them) and the overall condition of the machine.
But the good news is you have access to a great resource of materials from Southern Fab in inspection forms to perform your own inspection and reports where available. With the right resources (like the plate roll inspection form) and working knowledge, you can inspect the machine yourself. Look for the obvious; bent rolls, damaged rolls, hydraulic leaks, patches and repairs to roll ends. These could indicate the machine has had a hard life already and may not be up to the tasks and drills you plan on putting it through.
You should also consider buying from a dealership rather than directly from a shop or individual as machinery dealers know the questions to ask and the most common issues to watch out for with used plate rolls. Often shops haven't run excess equipment in years or purchased it with the building and know little about its former use or capabilities leaving you the buyer to take a huge risk.
4) Sheet Thickness and Minimum Diameter
Plate Rolling 101 suggests the basics of plate rolling is that you cannot roll any diameter to less than 1.5X the top roll in one pass. Multiple passes can get you down as tight as 1.1X the diameter (but don’t count on it, 1.3X is more likely) working with the right material. The tighter the diameter you are rolling the sheet into, the more roll pressure is needed and the smaller the top roll needs to be, however that also equates to a weaker top roll that will flex more under stress.
Plate Rolling 101 again notes that plate rolls come in “ranges” of capability and unlike other bending machinery such as a press brake, plate rolls cannot bend everything. You likely will have a plate roll sized for ¼” - ⅜” material but that same roll is useless on 1” plate. Adversely the 1” plate roll may be very ineffective on 10 gage material as well. Choosing a roll based on your mean requirements is important.
5) Service & Parts
Is there going to be any kind of warranty or service involved if you need it? Is there service available if needed? Are parts available? Fortunately on plate rolls they are very “user serviceable” unlike other fabricating machinery (Lasers etc.) so the maintenance and repairs can be easily performed by the owners. When you buy from a reputable dealer, you can ask them about serviceability and parts availability. Often, even if the manufacturer is no longer in existence you’ll find aftermarket support.
Browse the SFMS Inventory of Used Plate Rolls!
At Southern Fabricating Machinery Sales, we have a wide range of new and used machinery. We have new equipment arriving daily, so check back often to find the perfect fit for your fabrication shop. If you don’t see what you are looking for, just ask one of our professional sales staff. We network all over and can find you the perfect machine to complete all your production jobs the way you need them.
With an extensive working knowledge of manufacturing systems, going back with a combined experience of over 100 years our representatives can best assist you in locating and securing the best machinery for your application.
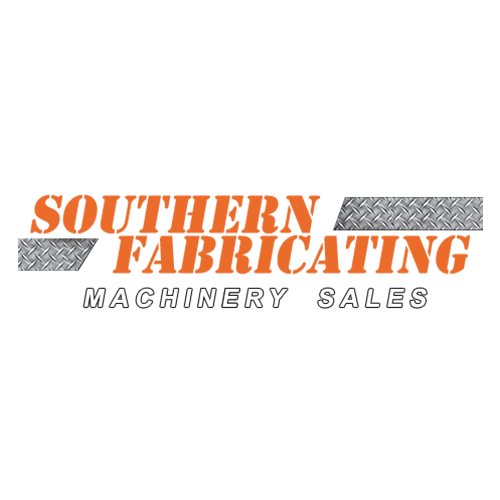