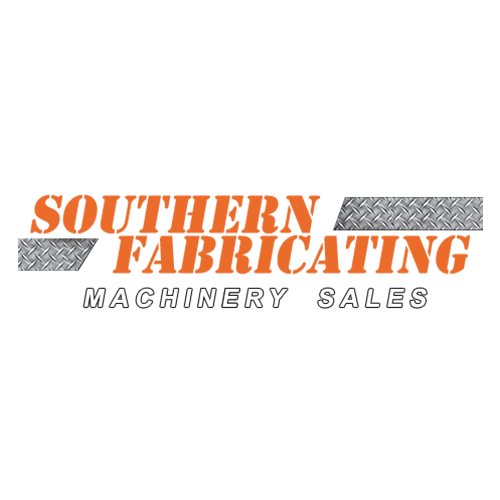
Posted By: Southern Fabricating Machinery Sales | Posted On: January 28, 2021
Why Outdated Manufacturing Equipment Maintenance Is Costing You Money
If you’ve been relying on the same old outdated manufacturing equipment for years and have stubbornly held on to it instead of upgrading to new equipment because you want to save money, you’re not alone. As it turns out, if that old machinery has been costing you more money in maintenance costs than you saved by keeping it, you’re also not alone. While it’s not uncommon to find people clinging to old equipment in hopes of saving a few bucks, it’s even more common to find that those same people end up losing more money in maintenance costs than they hoped to save.
How Does Manufacturing Equipment Get Outdated?
So how does manufacturing equipment get outdated? Just like anything else really. Gradual improvements over the years result in machinery that is more efficient, more productive, and ultimately less costly to maintain.
Holding on to old, outdated manufacturing equipment might save you some money in the short-term, but it’s going to burn up your profits in the long-term. No matter how you slice it, it’s just not worth it. Would you rather spend thousands of dollars a month to maintain some outdated machinery or spend a few grand on a piece of new equipment that will actually help you make more money?
How Maintenance Costs More With Outdated Equipment
Maintaining outdated equipment actually tends to cost more than maintaining newer equipment. Equipment maintenance becomes more expensive on outdated factory equipment over time. The reasons for this are multivariate. For starters, whether you like it or not people stop producing parts for old factory equipment after that equipment has been outdated for many years. This means that when you commission maintenance or repairs on that machinery it will cost more to get the parts.
Whether you run a factory or a machine shop you'd do well to learn the pros and cons of reactive maintenance vs preventive maintenance. When it comes to reactive maintenance vs preventive maintenance, the latter beats the former in terms of cost-effectiveness every time.
That’s because when you are constantly performing reactive maintenance, you’ll lose money on the downtime when the machinery is out of commission until it’s repaired. By opting for preventive maintenance, you can keep up on repairs before the machine stops working altogether. The bottom line is, with reactive maintenance, you lose money, with preventive maintenance, you don’t lose as much money.
Nothing kills profits and brings them to a screeching halt than unplanned downtime. The longer a piece of equipment is down, the more money you lose. As you might have guessed, old factory equipment tends to have more downtime than newer equipment which is another reason why maintaining outdated manufacturing equipment actually costs more than just buying new machinery.
Check Out Our Wide Inventory of New and Used Machinery For Sale at Southern Fabricating Machinery Sales
When it comes to buying machinery choosing between new and used equipment is always a critical part of your purchasing decision. Now that you’ve discovered the fiscal perils of holding on to old outdated machinery you might not want to look at used equipment. Keep in mind, however, that even used equipment can be a smart buy as long as that equipment is still technically newer than what you have on hand.
For example, if the machinery you have is 35 years old and you find some used equipment that’s only 5 years old, you’d have a smart buy on your hands! Whether you want new or used manufacturing equipment, you can find it all in one place, at Southern Fabricating Machinery Sales.
Find the equipment you need for less, from Southern Fabricating Machinery Sales!
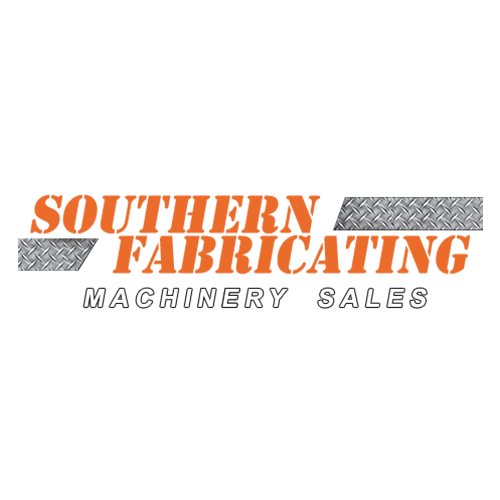