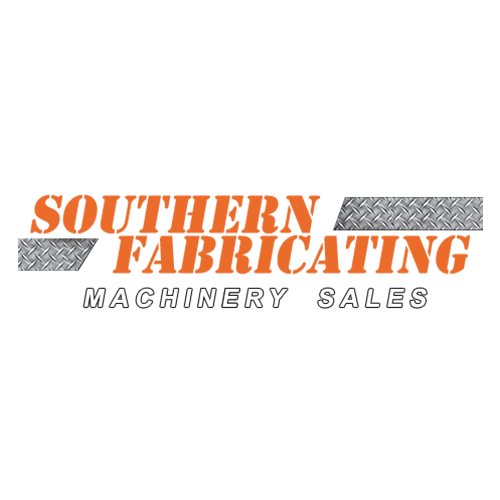
Posted By: Southern Fabricating Machinery Sales | Posted On: April 28, 2020
The Best Ways to Use Robotic Welding
In the world of manufacturing and fabrication, efficiency, quality, cost, and production are integral elements that influence decision making. As companies and shops (both small and large) are seeking to enhance their competitive advantage, they relentlessly look for ways to improve their output, minimize defects, and lower parts and labor costs. In a quest to achieve these goals, most of these companies are turning to robotics including robotic welding.
Although robotic welding has proved to be very productive for those completing high volume, repetitive welding activities, the decision to adopt a robotic weld cell calls for a thorough and deliberate study of your shop and processes. Fortunately, industries such as automotive, which pioneered the use of robotic welding, have set precedence with their impressive long-term benefits. However, before we delve into much into this topic, let's understand a few things about robotic welding.
What is Robotic Welding?
Robotic welding in the job shop is a fairly new application of robotics where programmable manipulators (robots) are used to automate the welding process from start to finish. It involves the use of an automated robot system that has various components, including an arm that can move in three dimensions, a welding power and gun source, fixturing and part manipulation as necessary and together working to fuse two metals together. This new application of robotics has helped fill the gap in the growing shortage of welding professionals.
Is Robotic Welding Better Than Manual Welding?
While both manual and robotic welding have their boons, Robotic Welding supersedes the manual when it comes to benefits. Robotic welding comes with several advantages over manual welding. For starters, it produces consistent welds of better quality in fast and repeatable cycles. Robotic welding also eliminates the number one cause of weld failures which surprisingly are not Bad Welds, but rather Missed Wledls that are commonly found in tresome, manually repetitive welding operations. It also lowers labor costs, minimizes material wastage, improves safety, offers superior performance accuracy, and yields higher output.
Benefits of Welding with Robots
Although robotic welding systems may need a hefty initial investment, it ultimately improves the bottom-line fabrication performance in due time. When used correctly, it boasts several benefits, including:
- Consistency and premium-quality welds
Robotic welding delivers top-class precision and uniform consistency that help minimize material distortion, thereby yielding high-quality end products. Additionally, using automated robots guarantees that you can repeat the welding process and achieve similar consistency every time. However, it is vitally essential to remember that the quality of the end product will highly depend on the type of robotic welding process and the kind of material you are working on.
- Improved Speed and Productivity
By streamlining the critical welding processes such as part handling, automated welding systems reduce the time required to complete a task. Conversely, robotic automation allows companies to work around the clock, thereby increasing the average production. It also enables employees to focus on mission-centric and high-level challenges, thus increasing yields all doing so without taking breaks or calling in sick.
- Less Rework and Reduced Wastage
Since robotic welding systems are consistent and ultra-precise, they reduce the risk of physical distortion and over-welding. Additionally, robotic welding allows you to regulate various elements, including power and pressure, thus helping you conserve energy. Having consistent weld quality and performance inherently reduces waste and rework.
- Cost Saving and Safety
Though the initial price can be substantial (compared to a manual welding setup), robotic systems help lower welding costs once they are in place. Manual welding requires skills and training, which can be expensive. Additionally, welding is a dangerous job since it leads to the emission of fumes, flash, and heat that can be detrimental to human health. Robotic welding helps improve safety by protecting workers from inhaling toxic fumes or suffering accidental heat injuries while performing their tasks over and over again, tirelessly repeating perfection.
What Should Robotic Welding be Used for?
Although robotic welding delivers outstanding ROI, the comprehensive system does not have to be an expensive system. As such, shop owners and companies should investigate Robotic Welding to ensure these systems can be used in areas where they are needed most. Generally, robotic welding is ideal for complex, high-skill, and routinely repeated tasks. They can be used in a variety of industries such as metalworking, general fabricating, packaging & handling, textile, automotive, and many more. To mitigate the initial cost factor, you can opt to go for used welding robots instead of new ones and although there are some essential things that you must put into consideration when deciding to purchase the robotic welding system. Robotics can add a big boost to your quality, throughput and bottom line.
At Southern Fabricating Machinery Sales, Inc. our team are experts in Robotics and Welding applications. Contact us today for a review of your welding application.
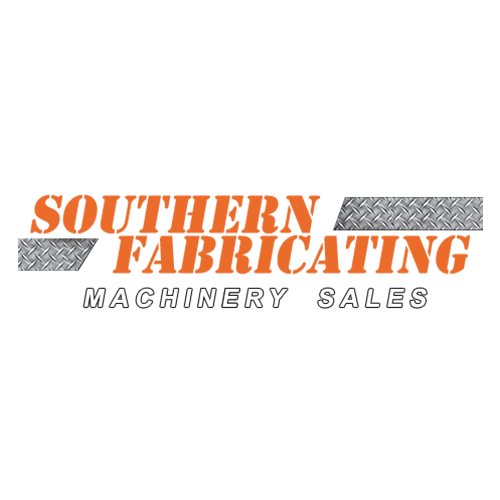