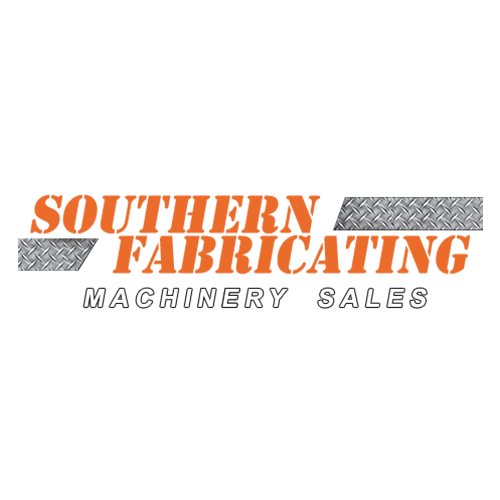
Posted By: Southern Fabricating Machinery Sales | Posted On: August 28, 2018
How to Choose the Right Type of Robotic Welding Equipment
Machine shop automation is becoming the norm for many processes. Robotic welding equipment, in particular, has caught on for manufacturers because it helps to prevent jobsite injuries from manual welding processes and helps to achieve more consistent results in welds—improving product quality and reducing part rejection rates.
The question is: “Which types of welding robots and equipment are right for your production floor?”
Because there are many different types of welding machines out there, it can help to narrow down your choices by asking a few key questions:
1) What Kind of Objects Will I Be Welding?
Different robotic welding processes are good at welding different things. For example, within the category of arc welding, there is gas metal arc welding (GMAW, or MIG welding) and gas tungsten arc welding (GTAW, or TIG welding).
TIG welding has a non-consumable electrode and must heat the objects being joined to something close to their melting point so they can be fused. This tends to work really well with thinner objects that can be heated through quickly and easily.
MIG welding uses a consumable electrode that melts to become a filler material for a weld. This helps to make MIG robotic welding equipment more useful for welding larger objects that would be difficult to heat through. It can also allow you to join objects made out of dissimilar materials.
So, if you frequently work with thicker workpieces or ones made of two different types of metal, a MIG robotic welding process might work better than a TIG one.
2) How Precise Does My Robotic Welding Process Need to Be?
Most robotic welding equipment is capable of incredible levels of accuracy for controlling the placement and timing of welds. However, there are different kinds of weld controllers that can manage the machine’s operation.
Computer numerical control (CNC) is the norm for welding equipment, helping to control the flash of the robotic welding process to minimize weld burns, spalling, and stress cracks. Some robotic welders have a medium-frequency direct current (MFDC) controller meant for resistance welding processes that require microsecond-precise control.
Plasma welding processes are fundamentally similar to torch welding processes and lack some of the fine timing control of arc/resistance welding processes that use electricity to heat metal—but, they can more easily control the size of the burn zone and the temperature of the burn.
When picking a welding machine, also be sure to consider how user-friendly the robotic welding programming process is for that machine—this can affect how well your team can use the machine and control the welds the machine makes.
3) How Cost-Efficient Should My Robotic Welding Process Be?
For some machine shops, the ongoing cost of a robotic welding process can be a major concern. Different types of welding robots can require different amounts of ongoing maintenance and consumable resources (wire, fuel, oil, etc.). These factors influence the total cost of ownership for a new or used robotic welding cell.
Ideally, you’ll want to buy a used robotic welder that has a very low operating cost. Here, resistance welding processes have an edge over MIG and plasma welding processes since resistance welds don’t require consumables. However, for some machine shops, it might be worth paying a little more on an ongoing basis to have access to a specific type of welding operation that works better with your most frequently-made goods.
4) Do I Really Need One Robotic Welder That Does Everything?
Probably not.
There are new and used robotic welders on the market that can perform multiple types of welding operations at once—there are even machines that can do welding and bending operations simultaneously. While this could be useful, becoming fixated on finding one machine that can fulfill all of your needs can quickly become costlier than it’s worth.
Instead of trying to hunt down one rare unicorn of a machine that can do 100% of the work you need to do, it’s often better to find a machine that can do 80% of the work you need to do and get a separate, less expensive machine to fill out the remaining “niche” work you need to do (or contract that work out to another shop that specializes in it).
5) Should I Get New or Used Robotic Welders?
A lot of machine shop owners are obsessed with having only the shiniest and newest fabricating machinery on their shop floor. However, there is rarely a good reason to buy a brand new, mint-in-box machine over a perfectly functional used machine that has been well cared-for.
Used robotic welding cells can be every bit as efficient and effective at joining metal objects as ones that use only new robots. Unless the brand-new machine has some capability that is absolutely critical for the effectiveness of your welding process not found in a used robotic welder, it is probably better to buy used because:
- Used Robotic Welders Are Less Expensive. Buying used is a great way to minimize the cost of acquiring a new piece of equipment for your factory.
- The Issues the Machine Has Are Already Known. Every machine has its issues. With a used robotic welding cell, the previous owners at least know what the machine’s issues are and can help you prepare for them so they aren’t a surprise to you.
- Used Equipment Can Be Shipped Immediately. Waiting times for new machines can be incredibly long. For example, some top brands might have waiting times for new machines in the 12-16 week range (or longer) to ship as you wait for a custom-manufactured solution. Buying used robotic welders means you’re buying something that’s already made and ready to go—reducing your wait to days for the machine to be boxed up and prepared for shipping.
These are just a few of the things that you should consider when purchasing robotic welding equipment.
Do you need help finding the right automated welding equipment for your shop floor? Contact Southern Fabricating Machinery Sales today to get expert advice and access to a large pool of potential sellers! We’ll help you find the perfect used robotic welder for your machine shop!
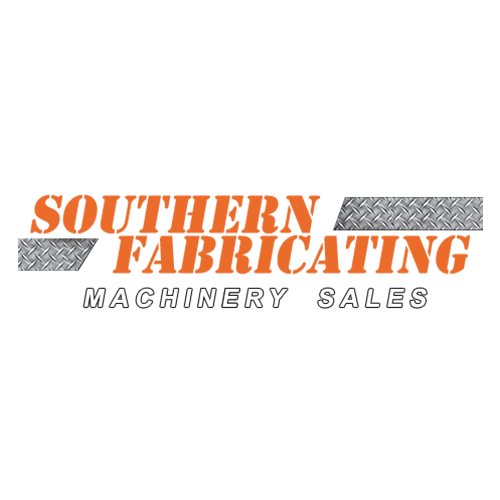