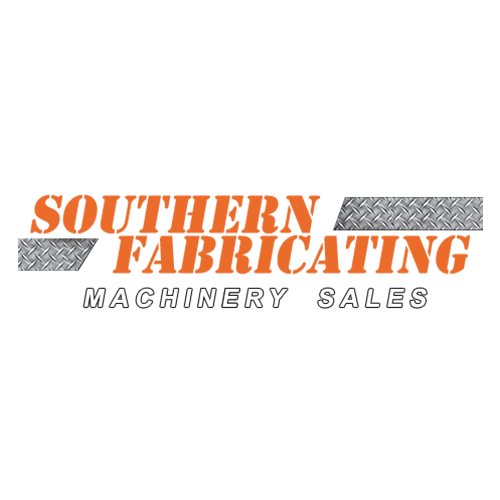
Posted By: Southern Fabricating Machinery Sales | Posted On: July 24, 2023
Simple Steps to Selecting the Right Plate Roll
Plate rolling is a critical process in various industries, from manufacturing tanks to construction. Selecting the right plate roll is crucial for achieving precise and efficient results. When considering a plate roll, several factors come into play, such as rolling length, top roll diameter, and the number of rolls. In this article, we will delve into each of these factors and explore their significance in the selection process. By understanding the importance of rolling length, top roll diameter, and number of rolls, you can make an informed decision and optimize your plate rolling operations.
Rolling Length
One of the primary considerations when selecting a plate roll is the length of rolls, which in turn determines the rolling length. Rolling length refers to the maximum length of the plate that the machine can handle. It determines the size of the plate you can roll and impacts the overall productivity of your operations. If you frequently work with long plates, it is essential to choose a plate roll with an adequate rolling length. Consider both your current and future requirements to ensure that the machine can accommodate your expanding needs but understand that as the rolls are lengthened the roll diameters become larger thus decreasing the minimum diameter that can be rolled.
Moreover, the rolling length affects the machine's stability during the rolling process. Longer plates exert more force on the rolls, requiring a robust and stable machine with features such as hydraulic crowning. Insufficient rolling length may result in plate deformation or unstable rolling, compromising the quality of your finished product. Therefore, carefully evaluate your rolling length needs and select a plate roll that can handle your desired plate sizes without sacrificing stability.
Top Roll Diameter
The top roll diameter is another crucial factor that influences plate rolling performance. It refers to the size of the largest roll in the machine. The top roll diameter directly affects the minimum bending radius that can be achieved during the rolling process and really determines the plate rolls capacity. A smaller top roll diameter allows for tighter bending radii, enabling you to roll plates into smaller diameters but subsequently lowers the plate thickness capacity.
However, it's important to strike a balance when selecting the top roll diameter. While a larger diameter offers more flexibility, it also increases the machine's overall size and weight. Additionally, larger rolls can impose more stress on the plate, potentially leading to deformation. Therefore, it is crucial to consider the range of plate thicknesses and materials you typically work with and select a top roll diameter that aligns with your requirements without compromising plate integrity.
Number of Rolls
The number of rolls in a plate roll machine significantly impacts its rolling capabilities and versatility. Most plate rolls feature either three or four rolls: two bottom rolls and either one or two top rolls. The number of rolls influences the machine's ability to create various bending profiles, such as cylinders, cones, or complex shapes easily while making sure the material does not slip in the rolling process.
Three-roll machines excel in rolling cylindrical shapes and are often suitable for applications where versatility or speed is not the primary concern. On the other hand, four-roll machines offer enhanced flexibility, allowing for the production of more complex shapes with minimal pre-bending requirements and only one setup. Four Roll machines provide better control over plate alignment, reduce the risk of plate slippage, and offer improved efficiency.
Consider your specific application needs when deciding between a three-roll and a four-roll machine. If you frequently work with diverse bending profiles or require high precision, a four-roll machine may be the better choice. However, if your operations primarily involve cylindrical rolling, a three-roll machine could be a cost-effective option.
Selecting the right plate roll is essential for optimizing your plate rolling operations. Carefully consider the rolling length, top roll diameter, and the number of rolls to ensure the machine aligns with your current and future needs. Assess the required rolling length to accommodate your plate sizes and maintain stability during the rolling process. Determine the ideal top roll diameter for achieving the desired bending radii without compromising plate integrity. Lastly, evaluate the number of rolls to strike a balance between versatility and cost-effectiveness. By considering these factors, you can make an informed decision and enhance the efficiency and quality of your plate rolling operations. At Southern Fabricating Machinery Sales our experts can help you select the right plate roll, new or used, for your needs and budget. Call or click below today.
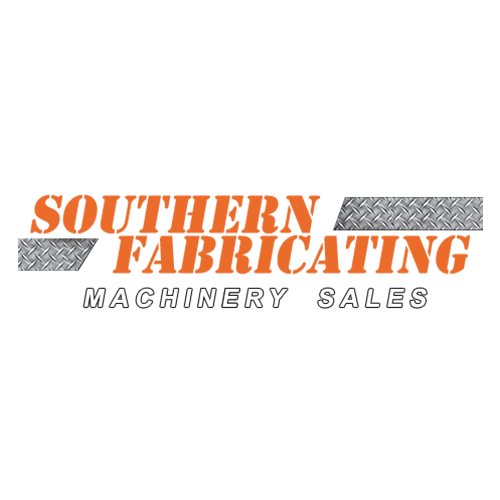