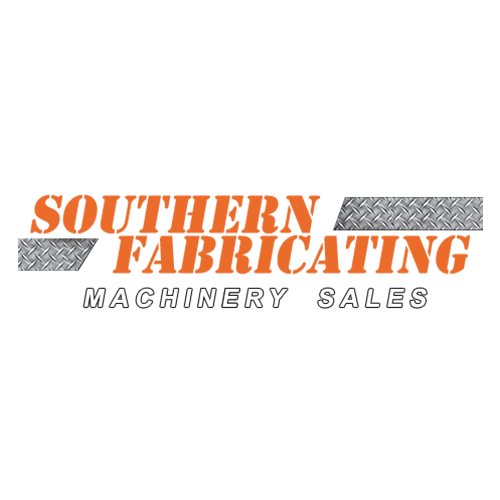
Posted By: Southern Fabricating Machinery Sales | Posted On: December 7, 2020
Plate Rolling 101 - Sizing the Right Plate Roll for Your Application
For those of you who are unfamiliar with purchasing a plate roll here’s some basics for users on how to select the right size plate roll for your application based on material thickness, material strength, diameter desired, and production needs. Because plate rolls vary not only in size but also in type it is important to also know the advantages of each plate roll design when making your decision.
What is Plate Rolling?
Plate rolling can be viewed as an art and with an experienced operator that understands the equipment, the material and the application, the outcome can be very profitable. Unlike other forms of metal bending such as press brakes, the material is not forced into a predetermined shape through a coining method, but rather it is coaxed into shape through a strategic positioning of rolls while moving the material. Experienced operator aside, it is important that the correct machine is matched to the job, material and production that is demanded.
Plate rolls are used to fabricate many components such as tanks, pressure vessels, pipes and just about any other cylindrical, oval or out of round shapes made with metals. Most plate rolls can adjust the top roll to a tilt position which allows products to be produced with cone geometries. There are also dynamic crowning systems that can be applied that facilitate adjusting the roll’s tension automatically or manually as needed. They are a vital tool in most every fabrication shop and given their capability can produce large profits for shops capable of rolling correctly.
Types of Plate Rolls
First of all, you need to become familiar with the different varieties of machines and their capabilities facilitating your selection for size and which machine is best suited for your type of bending application. There are 4 distinguished categories of plate or sheet bending rolls.
- 2 Roll Plate Rolls: Used only in high production thin material applications such as filter housings, cans etc. these machines are very limited in capability and are designed around a very specific application and production. A solid top roll is used to press the material into a softer urethane coated bottom roller and when thin strips of material are introduced the result is rolling the shapes very quickly into the diameter desired.
- Initial Pinch Style 3 Roll Plate Roll: Initial Pinch plate rolls are the most common plate roll purchased throughout the world due to mainly their price point. With 2 rolls mounted vertically over one another on centerline they “pinch” the material in position while a 3rd bending roll is manually positioned forcing the material up into an arch where the rolling process then can begin. These initial pinch machines are typically limited to materials ¼” in thickness and down
- Pyramid Style 3 Roll Plate Roll: The Pyramid style plate roll is designed with 3 rolls in a pyramid fashion (when viewed from the plate roll end) these rolls move diagonally up towards a fixed top roll. While this design is capable of rolling heavier plates it takes careful operation as to avoid misalignments during the rolling process.
- Variable Geometry Style 3 Roll Plate Roll: Also designed in a pyramid fashion this design allows greater flexibility in the 3 roll design to control the rolls during operation. The top roll can position up and down while the side rolls move laterally in or out allowing for varying geometry throughout the rolling process. Most often equipped with CNC Controls the Variable Geometry design is a difficult machine to master and one where plate slippage is common.
- 4-Roll Plate Rolls: The most desired plate rolls on the market are those of a 4 roll design. These plate rolls provide a constant grip (pinch) on the plate during the rolling process and also allow the material to be pre-bent in on simple setup unlike the 3 roll designs. Often equipped with CNC controls the 4-Roll machine can perform quick and accurate cylindrical rolling as well as many varying geometries such as ovals, squares, hexagonal patterns and an unlimited number of shapes only defined by the operator and designer.
These designs are often referred to in many different ways by manufacturers such as three-roll initial pinch, three-roll double-pinch, four-roll double pinch, three-roll variable translating, three-roll pyramid, and two-roll systems. They are also available in a vertical design that is suited for special applications allowing the material to roll across the floor instead of high into the shop ceiling space..
Why You Need the Right Size Plate Roll
When it comes to choosing a plate roll, alongside choosing the correct type it’s imperative that you get the correct size. If the size of the plate roll doesn’t match your application you’re going to waste your money unnecessarily. Getting the right type and size for the job should be a priority. To determine what size of plate roll you’re going to need or benefit from the most you’ll need to consider the types of applications, the material you will be rolling mostly and the operator skill level you have to work with.
How to Select the Plate Roll Size for Your Application
When it comes to choosing a plate roll, it’s imperative that you get the correct size. If the size of the plate roll doesn’t match your applications you’re going to waste your money unnecessarily. Getting the right size for the job should be a priority. To determine what size of plate roll you’re going to need or benefit from the most you’ll need to consider the types of applications that you are intending to use it for.
- Bending Length: The overall rolling capacity is determined by the physical length of the rolls which unlike other specifications cannot be “cheated” when purchasing a plate roll make sure you are sizing the roll length for the maximum width of material you will be rolling understanding that the longer the rolls the larger the roll diameter has to be in order to maintain strength ounder rolling pressure. The adverse reflection of that is the larger the diameter you will need to be rolling.
- Minimum Diameter: The minimum diameter is the smallest diameter you desire to roll your material into. Use the factors 1.5X the top roll diameter for easy, no problem, rolling in one pass to achieve this goal. 1.3X the top roll diameter can be achieved with multiple passes or material at a shorter length then the full width capacity of the pallet roll. 1.1X the diameter of the trop roll is also achievable in softer materials less then the full width of the rolls AND utilizing a multipass technique.
- Bending Capacity: Bending Capacity on a plate roll is the capacity at full width the machine is capable of. Rated in mild steel, a ¼” X 10’ plate roll is capable of bending ¼” thick mild steel in a 10’ width to 1.5X the top roll diameter in a single pass.
- Pre-Bending Capacity: Pre-Bend is the initial bend a plate roll operator must make before actually rolling the material. The process involves pinching the material firmly between two of the rolls and then using the side or lateral roll to force the material into an initial bend before rolling commences. This process must be repeated on each end of the plate being rolled to avoid large flattened sections at the mating ends of the cylinder. Pre-Bend capacity is always less than that of the rated bending capacity so it is important to ensure the rolling system you are looking at can properly pre-bend the material you are working with.
- Yield Point: The yield point is the strength of the material you are rolling, or better put, the strength of resistance to bending that the material has. The harder the material the higher the yield point and the larger/stronger the plate roll must be to roll the material. Yield points vary greatly from Aluminum to Stainless and other materials in between. Make sure you know the Yield strength of your material as plate rolls are all offered on a mild steel (36,000 PSI) yield strength rating.
Find the Right Plate Rolling Machine for the Job with Southern Fabricating Machinery Sales
Having the right information on the material you are rolling and the desired result in both capacity and production numbers can greatly simplify the plate roll machine of choice. If you choose the right plate roll supplier they can also provide you with a variety of detailed capacity charts for the machine offered. At Southern Fabricating Machinery Sales we help you select the right machine with our detailed plate roll selection spreadsheet. Just contact us and ask one of our experienced plate rolling experts for more information at 813-444-4555.
Get the plate roll you’ve been looking for from Southern Fabricating Machinery Sales!
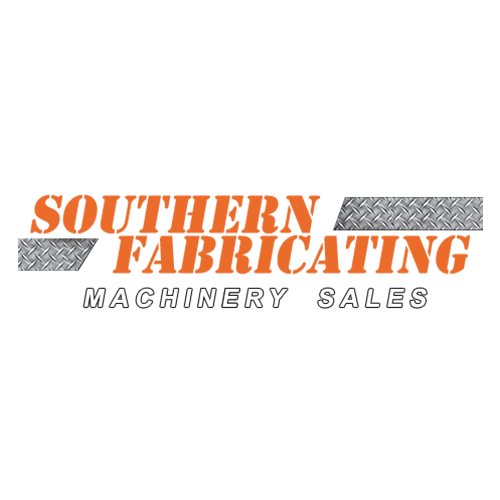