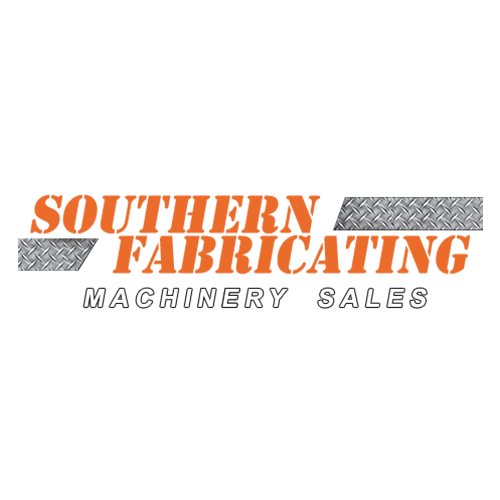
Posted By: Southern Fabricating Machinery Sales | Posted On: September 13, 2019
The Art of Wire Forming Machinery
Although there are many types of wire forming, in production wire forming specialized machinery is used. These wire forming machines have many methods that can be employed to achieve the desired results however only a few are available to manufacture repeatable and fast results. In years past this was achieved through the use of machinery using CAM’s to actuate benders (old technology). These CAM operated 4-Slide machines required extensive setup, many trial runs and scrapped parts and large quantities to make it all that setup worthwhile. Today, using CNC technology, the new and highly modifiable machines form wire for hundreds of processes from rebar used in concrete forms to store racks & shopping carts along with millions of other parts in between even including jewelry. Although this manufacturing technology has been around for thousands of years it has become a very specialized and highly technical industry.
What is Wire Forming?
Wire Forming is the process of taking a blank of wire whether from a spooled coil or blank length and forming or bending it into a specific configuration. This can be achieved either by a manual method of brute force applied to bending the wire around controlled shapes, or as this article focus’s on, utilizing machinery to feed and manipulate the wire to the desired shape. Wire forming can also include flattening and forming of the wires roundness as well in order to allow for proper fit for use of the product being designed. Wire formed parts can take nearly any shape or form, including one of the most common forms: springs. These wire forms can be bent left or right, up or down, angled, coiled and cut. They can be linked together to form a chain, or have other additional forms added to them. Wire can be from very small diameters such as used in springs and jewelry to over 25MM (1.0”) in size such as components that might be used in construction and chains.
How Does a Wire Forming CNC Machine Work?
A wire forming CNC machine utilizes a system of uncoiling the raw material from a spool and running it through a series of opposing wheels that are used to straighten the wire prior to the shaping and forming process. This feeding axis is controlled by the CNC controller as it controls the overall length of the part, the lengths between forms as well as the length of all components formed. Once a straight wire or bar is fed through the straightening rollers it is then fed to an articulating head whereas through a series of dies and pins the head twists and rotates around the straight wire whilst forming the wire in a series of preprogrammed bends. Once the part is completed to length an automated shearing blade is used to snip the wire off form the coil length and to the exact desired size. There are several types of wire benders on the market some of which are very limited in their application and scope. These 2D benders do not allow for the wire to be formed in anything other then a flat pattern. The more advanced 3D benders provide for an unlimited capability in wire in 3 dimensional space. These 3D Benders are by far the more preferred bending solutions for wire forming needs the world over allowing for complete flexibility in programming and design.
What Are the Critical Components of a Wire Bending Machine
A modern day CNC wire bender, as is most common in today's production environments, is made up of several critical components. Together these 5 critical features can produce the most complex forms and wire shapes.
Coil Feeder: The coil feeder is critical to ensuring the material is removed from the coil without tangling or snagging stopping the whole process. The winder should be motorized allowing the material to easily lift from the coil without compressing the coil and thus binding.
Straightener: The Straightening device ensures that all properties the wire obtained through manufacturing and storage in a coil shape are removed. Whether the wire is to be shaped into a spring, or flat shape the straightness of the wire being fed into the bending unit is critical to the accuracy and repeatability of the process.
Chamfering: One or both wire ends should be chamfered in the same machining and forming process eliminating s
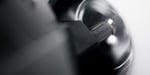
harp sheared edges or burrs from the cutoff process. A quality machine incorporates the chamfering process directly in the bender and does not require a separate manual chamfering operations.
Bending Head: The bending head is where all the forming is applied. The radii, angle, and forms are created by one or more articulating bending heads allowing the wire to be formed and wound while being fed via the feeding device for acute or varying angles and radii.
Cutting: The cutting or shearing system on a 3D wire bender should also be a programmable axis of the machine as it is the final element of the forming process.
At Southern Fabricating Machinery Sales, Inc., we are wire forming experts and can assist you with your 3D wire forming needs. Contact us today at 813-444-4555 or via email at sales@southernfabsales.com for more information or to assist you with your 3D wire bending needs.
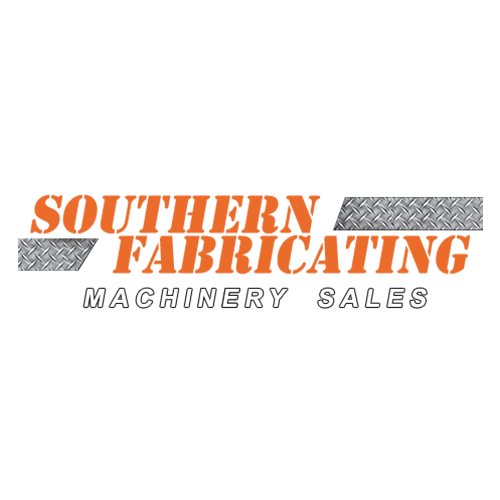