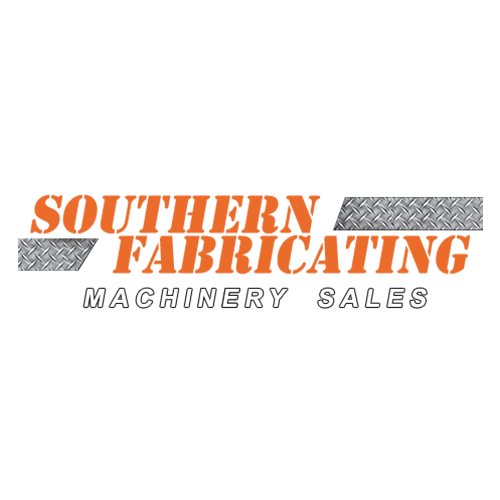
Posted By: Southern Fabricating Machinery Sales | Posted On: July 13, 2020
5 Unique Use Cases for Finishing Machinery
Metal products are everywhere around us, whether it is in buildings, vehicles, or aircraft. However, depending on the purposes, metals come in different colors, texture, or even finishes. For a metal component to be readied for its final purpose, it likely must pass through some sort of surface finishing, which is often one the final manufacturing steps. Finishing is one of the last processes that is performed on a particular piece of metal. It can be done to clean the surface, polish for appearance, burnish for an enhanced shine, strip coatings, smooth the surfaces and even deburr the surfaces and edges of metallic products. This is achieved through the use of specialized finishing machinery. However, before we delve deep into the matter, let’s try to understand more about surface finishing.
What is Surface Finishing?
Surface finishing simply refers to all the processes designed to alter the surface of a manufactured item to attain a given property. Using a specialized finishing machine and surface finishing technologies, fabricators and manufacturers can ingrain, deburr or alter a metal surface to achieve a given purpose. This can improve appearance, tarnish resistance, enhance corrosion resistance, wear resistance, chemical resistance, simply be preparation for paint or powder coating or modify electrical conductivity. In selected cases, surface finishing can also be used to salvage, repair, or restore an item's original finish changed through the fabricating process.
In the past, surface finishing was done by hand or using simple machinery, but as technology continues to advance, more sophisticated abrasive finishing machines have been introduced. These pieces of equipment perform a more refined work as they combine an abrasive material with or brushes to give a workpiece a sturdy and long-lasting finish.
5 Unique Use Cases for Surface Finishing Machinery
- Rumbling and Tumbling
This technique delivers the results of removing sharp metal points, small burrs and finishes the surfaces. Whether you use the barrel typoe or the vibratory type these finishing systems make short work of larger quantities of parts. Tumbling involves putting components in a tub or box along with abrasive particles (fabricated grinding stones or pellets in most cases) and rotating or vibrating the machine to mix everything randomly. The vibratory tumblers achieve the same goal through simple vibration induced to mix the abrasive media and parts together. This vibratory action removes burrs and creates a mottled finish that can be used directly or can be easily coated by clear lacquers, paint, powder coat or other protective materials providing for a long lasting finish much more durable to chipping and scratching then a non prefinished part.
- Sanding
Sanding is a finishing method used to clean contoured and curved surfaces by creating random, non-linear surface textures. In this method, different abrasive media can be used, and the higher the grit number, and the smaller or finer the particles and thus the more elegant the finish. Coarse grits help get rid of materials faster (such as the black scaling found on Hot Rolled Steel), while the finer grits are excellent when you want to achieve a mirror polish (such as Aluminum or Stainless steel control consoles. These types of machines can either be a large manually operated belt sander or a more automated belt feed system passing the material to be finished under a rotating belt or even multiple belts if the finish desired requires it.
- Magnetic Polishing
Magnetic polishing is ideal for finishing metal areas and small parts that are difficult to reach, such as pockets, deep holes, and chambers. Like tumbling, magnetic polishing involves placing components in a box or tub that is throttle-full with magnetized particles. And through the magnetic field, the particles are directed to rub the interiors of the hard to reach parts delivering an excellent and smooth polish. Magnetic polishing makes intricate parts soft and resistant to liquids or air.
- Abrasive Wheel Finishing
One of the more popular types of finishing machinery can use the afford mentioned Belt Sanding method in conjunction with either a drum style rotating abrasive brush and/or cup style rotating brushes. These brushes are made of a very durable material and often coated with abrasives such as garnet to further enhance thor material removal and surface finishing properties. Often these systems are used to not only provide a random or brushed finish on a material’s surface but to also deburr and round sharp edges providing for safe handling of the parts for later processing or use.
- Abrasive Blasting Machinery
Typically used in larger applications (structural steel) abrasive blasting machines can quickly remove scale, p[aint, rust etc from metals preparing them for use or more likely, for a prime and painting process for sorrion protection long term. These systems can be anything from a booth type manually operated sand blasting system or a chain-fed conveyor system capable of processing thousands of pounds of steel an hour.
At Southern Fabricating Machinery Sales we are experts in the fabricating process including Surface Finishing Machinery and can work with your application to direct you to the correct type of surface finishing machinery for your parts and budget. Call us today at 1-813-444-4555 or visit us on the web at www.southernfabsales.com to learn more.
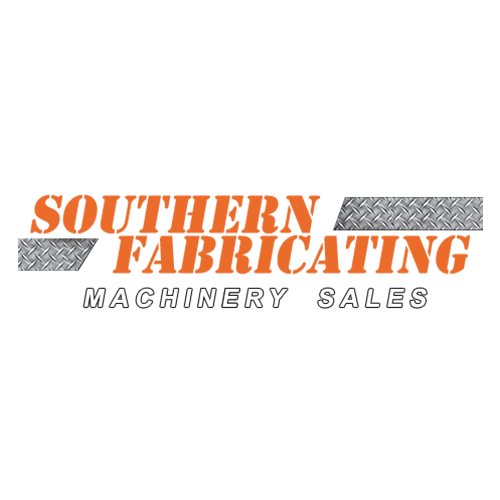