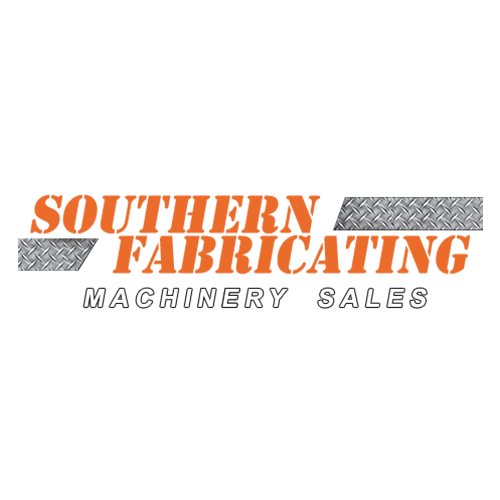
Posted By: Southern Fabricating Machinery Sales | Posted On: May 17, 2021
When to Use Bottom Bending for Press Brake Forming
On the topic of Press Brake operation we have discussed the differences between Air Bending and Bottom bending in the past in the article When to Use Airbending for Press Brake Forming but never when Bottom Bending should, or could be used. Bottom bending itself is as old as press brakes are and the technique was widely used a few decades ago but has lost the appeal over newer more accurate machines. However bottom bending still has a very necessary use in press brake forming applications.
What are the Types of Press Brake Forming?
In press brake forming there are several methods used such as:
- Air Bending: the process in which the material is forced by a punch held in the ram into the die seated on the bed of the machine only so far to produce the desired angle plus an additional amount to account for material springback.
- Bottom Bending: This process uses the ram and mounted punch to force the material all the way to the bottom of the die thus making the material yield to the shape and angle of the die it is forced into.
- Coining: Coining is a bending method that involves pressing the material between a punch and a die with a greater deal of tonnage or force. The punch literally compresses the material at the point of contact creating a very accurate & highly repeatable angle.
- Flattening: Used in the hemming operation, flattening uses a flat upper punch and lower die to close a folded section of material producing a “hem” in the material.
- Custom: In a custom forming application a tool will be designed and created for a specific forming application often having multiple bends in the same operation. These custom tools are material and application specific but can yield much higher accuracy as well as faster production results.
What is Bottom Bending?
As noted above, the press brake forming process of button bending forces the material all the way to the bottom of the die where the material takes the shape and angle of the die it is forced into. This process requires the punch and die to be designed to work together for a given material thickness.
How Does Bottom Bending Work?
Bottom bending in press brake forming works by forcing the material to take on the angle of the lower die. This process relies more on the accuracy of the die shape and less on the accuracy of the ram and thus, punch's position making this a preferable method of bending for older press brakes where the ram position is less controllable or repeatable. This method of forming however limits the user to only forming one angle per setup and requires a larger variety of bottom dies for the various angles desired.
What is Bottom Bending Used for?
Bottom bending in press brake forming is used today primarily for high production single bend applications such as clips, hinges, brackets or other parts where only a single bend is desired. A key advantage of bottom bending is speed as press brakes employing this method are typically mechanically operated and cycle very quickly without the hesitation and drag of newer hydraulic systems. Although bottom bending is used less frequently today it is still a very viable, and fast method of forming on a press brake.
At Southern Fabricating Machinery Sales we can assist you in selecting the right press brake and forming method for your application whether it be Airbending, Bottom Bending, Coining or any of the other methods available. Our fabrication experts can help you make the right forming choice for your application and budget.
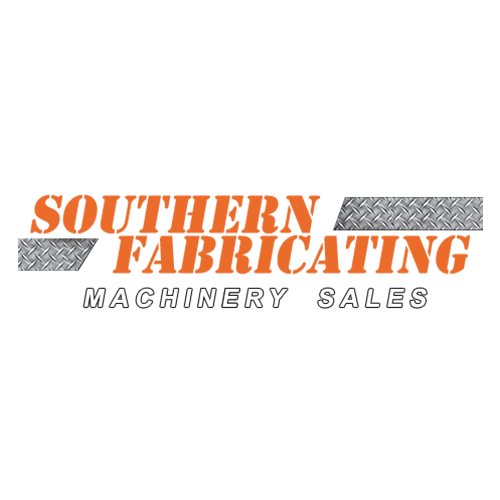