Electrical discharge machining (EDM), also known as spark machining, uses either an electrode for EDM sinking or a brass wire for wire EDM. This is a process where electrical discharge “sparks” come from the wire or electrode which, basically, erodes the material to make the required part.
Uses of a Sinker EDM Machine
A sinker (or diesinker) EDM has many uses—from making starting holes for wire EDM to mirroring an electrode shape into the desired shape in the part. The sinker EDM will burn any electrically-conductive material without inflicting the same physical stresses caused by other types of machining. This can help to improve the overall condition of the finished product compared to other cutting and shaping processes. They are still commonly used in the manufacturing of dies and molds and can be used as a “lights out” type of cutting.
There are many parts that need intricate holes or cavities that just can’t be done on a milling machine and the machine takes the advantage of using all movable axis to get the cavity made without harming the rest of the part. That will keep the sinker EDM business going on the parts where there is just no other way to get to them. Some parts will require multiple electrodes, so tool changers are available for the sinker EDM—which makes lights out production very achievable.
Sinker EDM Electrodes
There are many types of electrode materials that can be used for sinker EDM centers, such as brass or graphite. In some cases, they can use the upper mold cavity as the electrode—such as in the case of making molds line up smoother to create a less of a parting line or seam.
When making the electrode, it can be as easy as a simple shape (such as a round or square tip), or as complex as a three-dimensional shape that is burned in the workpiece as a reverse image.
With recent advances in controls and programming, these complex shapes are often made on vertical machining centers (VMCs) with high spindle speeds to achieve the finishes needed to make the electrodes and vacuum systems that are required to remove the graphite dust that is produced. With that being said, some sinker EDMs have been upgraded to directly make the shape in the part just using a simple electrode as well.
Keeping a Sinker EDM Operating at Peak Efficiency
When a sinker EDM is being used, the part will be in a bath of EDM dielectric fluid. This is used to control the spark between the part and electrode and then leave an inactive debris, the solution also acts a flushing agent with the up and down movement of the EDM center allowing the debris to be washed clear of the part. Keeping this solution clean will make for better parts—just like coolant does in a chip cutting machine.
Want to know more about the principles of sinker EDM machines? Or, just need help finding the right EDM tool for your shop floor? Contact the SFMS team to get useful advice and support for your fabricating equipment needs!
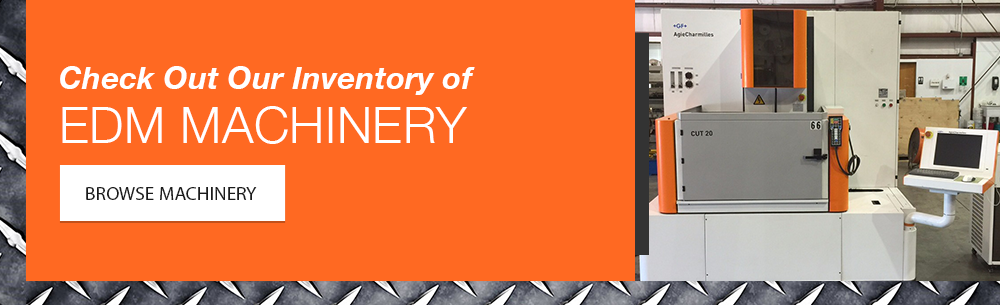