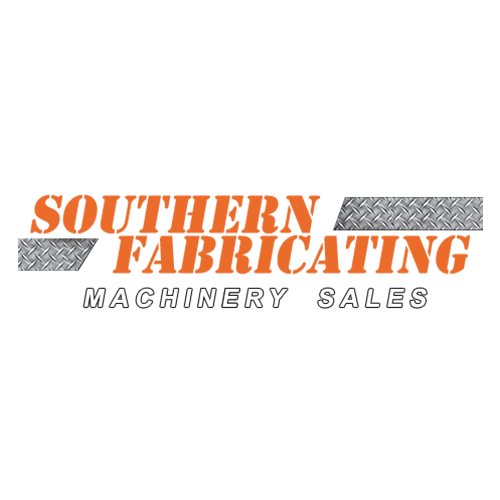
Posted By: Southern Fabricating Machinery Sales | Posted On: February 8, 2018
4 Different Types of CNC Machinery
The middle name of our company is Fab which is short for fabricating and a lot of what we sell is fabrication machines such as press brakes, shears, lasers, waterjets, plasma cutters, etc. We do quite well with fab equipment but we are also very good with buying and selling used CNC machines and some of us at Southern Fab have spent our whole working career working with CNC machinery.
The CNC side of Southern Fab Sales covers a wide range of CNC (computer numerical control) categories such as turning and milling which are commonly classified as “chip making” machine tools since they create chips as they cut metal. Four types of CNC machinery that fit this description include:
1) Turning
Generally, turning machines are horizontal and start with simple two-axis control of the tool. The cutting tool may be a manually-mounted single toolpost style or by a series of tools mounted in an indexing turret. This is known as the fixed headstock principle where the workpiece is clamped in a chuck or collet and the tools move around the part.
A very high percentage of the turning machines sold in the US are of the simple 2 axis configuration. Vertical turning comes into play for large diameter parts that are normally short when compared to the diameter which will be covered in more depth in another blog.
Milling capability can also be available utilizing a “C” rotational axis on the work spindle and rotary or driven tools in turret allowing various milling features to be included on the workpiece. A further enhancement to the “mill-turn” lathe would be the addition of a “Y” axis which would enable the driven tool to move above and below the centerline of the spindle.
From the concept shown above, a second spindle to oppose the main can be added. The second spindle, commonly referred to as the sub spindle, has the ability to pick-off a part from the main spindle as it is cut off and then further operations can be performed on the back side of the part. From here, a second turret can come into play which will add more tool capacity and will allow a tool in the cut at each spindle thereby reducing cycle time. Three and even four turrets can be added for either chucker style parts or bar stock machines.
CNC lathes from 2 to 12 axis and beyond can be used to fit an application for the end user.
View Our Inventory of Used CNC Machinery for Sale
2) Swiss Turning
The “sliding headstock” principle is strictly applied to running barstock and normally the barstock is precision ground in order to maintain a close fit to the guide bushing that the bar moves through and the cutting tool is positioned close to the guide bushing face.
Beyond turret style lathes, there are gang style lathes that are mainly for simple 2 axis turning and Swiss style lathes for multi-axis complex parts made exclusively from barstock. Swiss machines have the unique capability to turn long, slender parts without the issue of deflection as would be the case with a “fixed headstock lathe”.
3) Vertical CNC Milling
Most CNC milling is done on the vertical plane from very basic 2 or 3 axis Bridgeport knee mill style machine to a very typical VMC (vertical machining center) with X, Y and Z axis motion.
VMC machines are equipped with a tool magazine and an automatic tool changing mechanism to remove the existing tool that has completed its task and then replace it with another tool from the magazine.
Most VMC’s use taper style tooling such as BT or Cat but also can use more modern tooling such as HSK, a European standard. Since the tool is clamped in the spindle, higher speed machines (10,000 RPM +) may require that the tool be balanced.
Machining center tooling is common for vertical and horizontal machines.
Rotary tables can be added to provide additional capability along with the use of additional axis in the CNC control. Normally a 4th or 5th axis is added and in a lot of cases, both. Rotation can be provided for the side or end of a part. Beyond that, rotary tilt can be achieved with a table as shown below.
4) Horizontal CNC Milling
As with vertical milling, the tool rotates and the workpiece is stationary but the spindle is now rotated by 90 degrees. The part is mounted on the table that has at least an X and Y axis moving the part around the tool.
A rotary axis mounted on the X, Z axis (4th axis) is very common on horizontal machining centers. Horizontals also lend themselves to the adaptation of pallets and multiple pallet systems as seen below. Automation is a key advantage for a horizontal machining center since pallets outside of the machining area can be loaded and unloaded while the spindle is running thereby increasing the efficiency of horizontal machining over vertical machining.
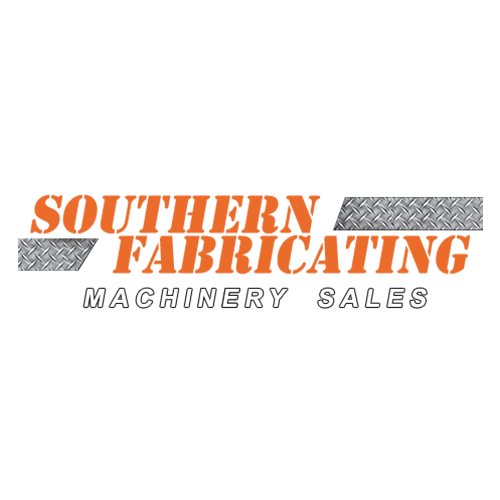