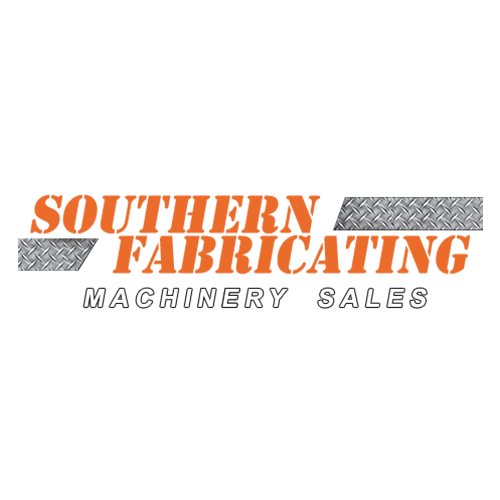
Posted By: Southern Fabricating Machinery Sales | Posted On: June 21, 2019
How to Perform Fiber Laser Cutting Machine Maintenance
Successful Fiber Laser cutting machine maintenance shouldn't be about fixing things at all, rather it should be about NOT having to fix things which can only be achieved through proper maintenance. Although not all shop owners or fabrication managers realize this, the truth is a successful fiber laser maintenance schedule is the key to a successful fiber laser operation. Fiber laser cutting machinery repairs, when they do occur, can be a costly reminder to proper maintenance as these machines can run upwards of 1M or more, and every moment they are not producing parts they are costing your plant money. If the approach to proper maintenance is hamstrung, the likelihood of costly downtime and extensive repairs is greatly increased thus increasing the costs of parts that the system produces which certainly negatively impacts a plants bottom line.
Train the Team: Every winning team requires training. Training to ensure they are working together, and training to ensure they are operating together for the good of the company and thus the performance of the machine. Your operator should be just as trained on the machine as your maintenance personnel and vice-a-versa. Training your team is an investment that will pay dividends back in up time and production throughput. Whether your team is operating a 10 year old used laser cutting system or a brand new state of the art Fiber Laser Cutting System make sure they are trained at the task ahead to keep the machine operating at peak performance and thus saving your company money.
Follow Directions: Every Fiber Laser Cutting System manufacturer offers a recommended maintenance schedule. Follow it, as it’s there for a reason. Although it may sound simple enough, this is an often ignored or overlooked factor. A maintenance log should be kept and adhered to with each maintenance interval and because maintenance, or lack thereof is logged, it is more likely to be performed as required when logging is required. These instructions are often now in videos embedded in the control software of the fiber laser machine and are easily available to operators and maintenance personnel alike. There should be no excuse for not following the manufacturer’s directions on proper maintenance techniques and intervals and likewise there should be no tolerance for excuses made.
Know your MRO: Maintenance, Repair and Operating (MRO) inventory is critical to your maintenance schedule of your fiber laser cutting machine. Having the right parts on hand can mean the difference between a few minutes of downtime, or a few days, and although fabricators in today's lean shop environments aren't keen on keeping a plethora of inventory in spare parts, they should recognize the value and importance of having the right spares on hand. One good way to avoid this issue is by having a service agreement in place. An annual laser service agreement or contract allows for the shop to maintain a smaller amount of critically needed items while the contracted service team perform the major maintenance required at semi annual or annual intervals and thus maintains a stock of those required components.
Connecting with your machines manufacturer and reviewing the parts you have or need to have, on hand can be a great and simple way to ensure your uptime. Many items that seem simple enough (like filters) can bring a fiber laser cutting system to a halt while it awaits a replacement that is just a few dollars. Having that item in stock and available is critical to the overall success.
Predict Your Downfall: A keen service team and operator can predict failures by monitoring machinery parameters such as hours of use of each consumable. Monitoring the machine closely can be an easy and effective way to detect anomalies and predict when things like lenses and nozzles will likely need replacement. Further by outfitting the machine with remote monitoring capabilities is another way to ‘catch the culprit in the act’ as you are able to watch in real-time your cutting capacity decline due to dirty, worn or failing components.
Know Your Part: Whether you order parts direct on your machine controller (available on the newest fiber laser cutting systems) or you use a purchasing department and internal Purchase Requisitions. Know your part number and item description. Many times purchasing agents are just copying your information from one spreadsheet to another or by hand. The more accurate the information you provide the more likely you are to get the right part. Instead of ordering part #982345-01 try ordering part #982345-01 Upper Head Coolant O-Ring Seal as it may make all the difference when the OEM catches the mistake in part number vs. description. Also always try to include your machine serial number with every order as that is another way your manufacturers parts department can help ensure you get the right part the first time.
Keep Your Key Accounts Happy: Most shops have a few major customers or “key“ accounts that provide the majority of their fiber laser cutting work. Knowing their production schedule and aligning your maintenance schedule to it can be extremely beneficial to both parties as it allows for more uptime when the demand is there and time for preventive maintenance when peak demand is down. This can also be helpful in ordering materials for forecasted jobs and scheduling necessary maintenance on other machinery associated with completing your "key" accounts projects.
Know Your Options: Whether you purchase your consumables, spares, filters and replacement parts from your OEM or an after market source, know what your buying. You should know the quality, reliability and lifespan of aftermarket components to ensure you have calculated for them in your production schedule. Components that are 30% less but fail during peak runs can be detrimental to our overall operation and in the end not worth the cost savings at all. Typically as machines age the availability of aftermarket components becomes greater. Knowing what's available and from whom can greatly reduce your operating costs overall. Whatever the savings ensure you are comfortable with the life span and availability of these replacement parts as well as the support you get from the supplier of them.
It is important to set boundaries for your purchasing department when purchasing aftermarket components as their job (to save the company the most money on the part they buy) may not align with your job (to keep that fiber laser machine making quality parts). Any final decision on laser consumables purchased should never be made on part cost alone but rather cover all the aspects of quality, availability, technical support and your chosen suppliers track record.
Extend the Coverage: On new equipment you can buy an extended warranty and in a fiber laser cutting system it’s a wise idea as the cost associated with it vs. the value received is negligible at best. On used machinery that is often not an option, however you can get setup with a preventive maintenance package from either your OEM or an aftermarket service company that specializes in your make and model. A preventative maintenance that provides scheduled service is a great way to minimize downtime and have an expert on hand for those intermittent problems that are not easily resolved by the operator onsite.
At Southern Fabricating Machinery Sales, Inc. we pride ourselves in helping manufacturer’s the world over wring the most productivity out of their new, or used fiber laser cutting systems, or other machinery. We recognize that a well maintained machine breaks down less and most importantly, performs better then ill maintained systems. Our staff of experts can help you pick the right machine, new or used and connect you with all the components to make your fiber laser machine a reliable and successful tool in your shop. We offer great tools as well like this free Machinery Inspection Checklist as well as many other resources. Call us today at 813-444-4555 or visit us on the web at www.southernfabsales.com for more info on how, our team can make your team, a winning team too!
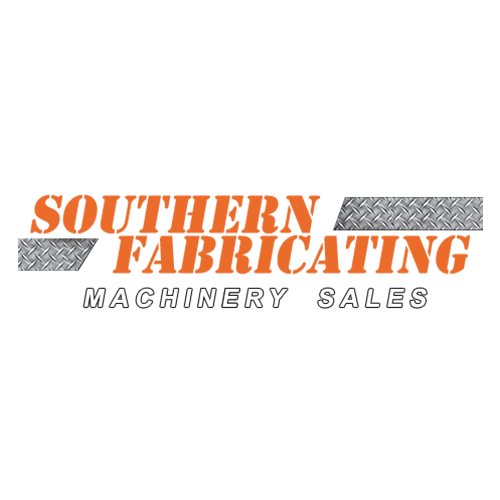