Posted By: Andy Kamashian | Posted On: December 7, 2018
An Introduction to Shears & Shearing
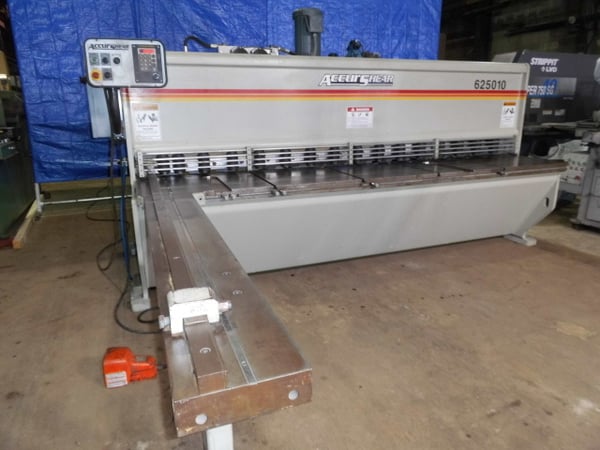
Shearing is one of the oldest metal working process available and is usually the first process and machine that is used when manufacturing fabricated parts. All shears are rated on their capability to cut steel and should be selected according to the capacity required as related to steel. If your application is Stainless Steel, you should select a shear that is rated for approximately 1.5-2x the material thickness you are using. Should you be shearing Aluminum, a shear sized for 1/2 the amount of material thickness you are working with is likely sufficient. Although there are small hand or foot operated shears as well (mostly used in HVAC and the Roofing Industries), this introduction will be focusing mostly on powered shears in the 14 gage (.075" x 10') range and heavier, which are found in most fabrication shops across North America.
Process Description:
Shearing sheet or plate steel is very much like that of using scissors to cut paper or cardboard. The blades come together at a minimum distance or offset that we describe as "blade gap" in order to fracture the material into the desired blank sizes for further processing. The lower blade is fixed into the "Bed" of the shear while the upper blade moves either in a straight up and down "guillotine" fashion or a swinging "rotary" motion. The thicker or harder the material, the wider the blades must be gapped apart or the blade angles increased (rake angle) in order to reduce the amount of tonnage required to shear (or fracture) the material up to the given rating of the machine.
A quality shear can save many hours on further processes such as bending, welding and assembly so it is important that you ensure you are capable of making quality, clean cuts that are square, accurate and can be repeated quickly. Some of the key factors in choosing a shear are described below and when choosing your shear, whether new or used, these factors should be considered in your decision making.
Components of a Shear:
All shears are made up of the same basic components and they are as follows:
-
Main Frame: The Main Frame of the machine is what supports all the other components, bed and drive system. A quality shear has a tough and heavy frame for the material size and rating. Some lightly built shears are known to be susceptible to having fractured sideframes, cracked beds or warped rams due to poor design or abuse.
-
Bed: The bed is what your operator will be working on as he introduces material to the shear blades. The bed is the support for not only the material but also the lower shearing blade. A quality shears bed should be heavy and solid with conveniences for material handling like cut outs for the operator to slip his hands under the sheet of material for lifting and ball transfers to "roll" the material being sheared easier into place.
-
Squaring Arm: A squaring arm is crucial in ensuring the material being cut is at a square 90 degrees. In order to achieve proper squareness, a squaring arm is used that has been setup and adjusted to ensure it is perfectly square to the shearing blades. This squaring arm can also have a measuring scale on it which can help in measuring very short sheared parts from the front of the machine as opposed to using the gage bar as a stop behind the shear blades. Typically the squaring arm is equal to the length of the shear blades but can be any length that works for the application you are selecting it for.
-
Hold Downs: "Hold downs" are clamps (or a single bar type clamp) that is located next to the shear blades and firmly hods the material being sheared to prevent it from moving during the shearing process and most importantly for tipping up which would introduce the material as a wedge between the upper and lower blades forcing the gap to open wider. Typically the more force and number of hold downs equates to the sign of a better and higher quality shear.
-
Blades: The cutting (or shearing) blades are typically tool steel and are hardened for wear resistance and ground for sharpness. They are mounted on the upper moving ram and the lower fixed bed and gapped usually just a few thousandths of an inch apart. The blades can be "flipped" when worn from progressive use to another side, resharpened or replaced. Shears typically have blades that have 2 sharp sides or 4 sides for use depending on the design of the machine.
-
Gaging (Measuring System): While not specific to every shear, gaging (or a part length stop/measuring system), is on about 95% of the shears on the market today. Proper gaging is crucial for not only maintaining the correct sheared length, but for allowing the operator to quickly "gage" the next sheared blank and repeat the process very quickly. Usually these "Gages" (or stops) are at the rear of the shear and commonly are computer controlled, screw driven gage bars for bumping the material up against. These gages can be manually or electronically (programmed) positioned to provide for multiple sheared lengths as well as repeated use of the same length. A quality gaging system will be strong enough to support material weight equivalent to the the full capacity of the shear for many years to come.
-
Control: A shear control can be as simple as a hand wheel manually positioning the back gage in conjunction with a foot/clutch pedal, or can be as extensive as a programmable gaging system allowing for precise programmable positioning of the gage system while keeping an accurate cycle count. While most shear gage controllers are used as a simple "Go Here" positioner, many are capable of much more including shearing "kits" of multiple part pieces and lengths all postioned and counted automatically.
-
Accessories/Options: A shear can be customized to meet a variety of needs by adding optional accessories that can make the operation of the shear simpler, faster, more accurate and more reliable. Common shear options include:
-
Stacker/Conveyor
-
Hydraulic Cooling Systems
-
Front Gaging
-
Extended Backgages
-
High Speed (Hydraulics Only)
-
Safety Options like light curtains, fencing, etc.
-
Ball Transfers in the Bed
-
Hand Cutouts
-
Scales in the Bed
-
Mitering Squares
-
Special Bed Machining or Tapping for Accessories
Types Of Shears
Guillotine
A "Guilliotine" design in a shear refers to the upper blades action of motion. The blade is driven in a straight direction by a mechanism and way system driving the ram and blade straight down and up. Usually this design equates to a bigger heavier design in a shear and is almost always found on designs rated in the 1/2" capacity or greater.
Swing Beam
A swing beam design shear uses the power of leverage through a cantilevered ram to increase tonnage and thus shearing capacity. Placing the upper blade on a pivoting mechanized ram, the blade is than forced down by mechanical or hydraulic actuation using the power of leverage. This design usually equates to a shorter in height machine design and also blades that must be relieved for clearance allowing typically for only 2 cutting edges per blade. There are also modified versions of this design that are some of the most popular designs sold today.
Types of Shear Drive Systems
Hydraulic
Hydraulic pressure is applied through one or more cylinders to force the ram and upper blade of the machine down. Hydraulic machines can have typically one or two hydraulic cylinders for operation.
Mechanical
A motor spins a large flywheel at high speed the operator then engages a clutch which can be activated via pneumatic, hydraulic or mechanical engagement. Once the clutch is engaged the moving flywheel is mated to a crankshaft in which the machines ram is attached. The crankshaft then spins cycling the ram and shear blade up and down.
Other Shear Design Factors to Consider:
Rake Angle: "Rake Angle" is the angle of the upper cutting blade as it is introduced past the lower cutting blade. This angle of introduction allows for only a small portion of material to actually be engaged with the blades at any given time, thus greatly reducing the forces required to shear long lengths. Ideally, if the force required to shear a part was of no consideration then a machine would have 0 rake angle as it would theoretically provide for the straightest sheared part and quickest cycle time. However since shears are typically working with 120-144" of material length or more, the amount of the force required would be massive and therefore, cost prohibitive. "Rake" angle is thus necessary in order to minimize the actual force required to "fracture or cut" the material being sheared.
Ideally a quality machine has as minimum a rake angle as possible, typically 1/4" of angle per foot, as excessive rake angle can cause Twist (sheared part curling) and/or Bow (Sheared part rolling into an arc).
Adjustable Rake Angle: Some shear manufacturers use a mechanism that allows the upper blade to vary the angle of rake in order to maximize the shears capacity. By increasing the angle of rake, the amount of thicker material actually engaged in the blades remains within the shears power "window". While these manufacturer's advertise this as a "benefit" of their machine, the reality is they are offering a much lighter machine with the capability to shear thicker material through this increased rake angle. When choosing a shear with variable rake angle, be sure to investigate it thoroughly as to what its capacity is at its lowest, or recommended, rake setting as this is really what the shear was designed to handle and greater thicknesses are only achieved through increase the rake angle and thus increasing the Twist and Bow you can expect in resulting sheared part.
Blade Gap Adjustment: In any shearing operation the higher the offset between the upper and lower blades, the lower the force required to break, or fracture the material. As the blade gap becomes excessive, burring (or tearing) begins to occur on the sheared blanks. If Blade Gap is set too closely then the force required to break the material can be in excess beyond the shears ability. Because different materials like Aluminum, Steel and Stainless steel have different fracturing forces they require different blade gap settings to ensure you are getting the best quality sheared part for thew given material type and thickness you are working with. All shears come with the ability to "Gap" the blades either by manual shimming (very slow), Bed/Lower Blade adjustment (slow) or by a quick blade gap adjusting mechanism which also can be powered (fastest). Depending on the range of material types and thickness you are working with will determine the necessity for a quick blade gap adjustment feature on your shear.
Common Arguments when Selecting a Shear
Argument 1: Mechanical vs. Hydraulics- Which is Better?When selecting a shear many people assume that hydraulic operation is a better option as they equate it with a press brake. However shearing is a completely different process and mechanical actuation can actually be preferred in a shear due to the following factors.
-
Speed: Mechanical Shears are faster in full cycle mode
-
Simplicity: Mechanical Shears have simpler mechanisms to maintain and repair making up time longer and downtime shorter
-
Noise: Mechanical Shears are quieter as they do not have the constant running of hydraulics
-
Heat: Without hydraulics mechanical shears run much cooler
-
Green: No hydraulic Oil, No Hydraulic Heat (requiring cooling), No Hydraulic Oil Waste, No Filter Waste
Where hydraulic shears have an advantage is:
-
Variable Stroke Length: Mechanical shears must make the full cycle when shearing whereas hydraulic shears can be set perform quick short strokes useful when shearing material of only a few inches in width.
-
Overload Protection: Protected by a blowout valve a hydraulic shear can stop the blade from getting into a "locked" position with the material as when the hydraulics reach the maximum PSI for the shear a safety valve opens up and dumps the high pressure hydraulics stopping the downward force and thus allowing the ram to backed off and the oversize/hard/obstruction to be removed.
Argument 2: Pit Vs. No Pit - Which is Better?
As shears increase in material thickness capabilities (force/tonnage), or stretch out in width, they may require a "pit", or more accurately described as a slot in the floor. The reason this relief in the floor is required is due the mechanical properties of shearing that cause both the bed and ram to deflect under the high tonnage required. While adding mass to the ram (upper part of the shear) simply makes the machine taller, adding mass to the bed would raise the working height of the machine beyond a comfortable level. Therefore the easiest and best way to counter these forces is to add more mass to the bed and put that mass below the floor. By adding this mass the manufacturers have made a stronger, heavier machine that can operate with low rake angle for good quality parts and will not flex under load. This added mass actually increases the rigidity, part quality, life expectancy and manufacturing cost of the shear and therefore is found in better quality heavier and wider shears.
The best method for keeping the machine and parts straight is to not let it bend in the first place and thus a pit is actually preferred over flush floor mount machines in higher capacities (3/8" and up) or wider widths (14' and Wider).
Summary
When selecting your shear, or any machine for that matter, ensure you are getting the best machine for your application. It is so easy to get trapped in the common pitfall of price, availability, location, freight, etc all of which will never matter in 6 months after the right (or wrong) machine is on your floor and certainly not in 3, 5 or even 10 years later. Remember your salesman can sell you literally whatever your "buying" and that includes discount, location or the right machine, but only if you ask for it.
At Southern Fabricating Machinery Sales, Inc. our staff are experts at shearing, both the process and the common problems. Call us today at 813-444-4555 to help you select the right shear for your application AND Budget.