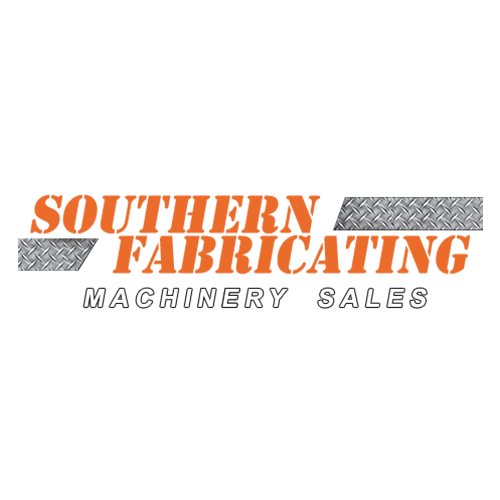
Posted By: Southern Fabricating Machinery Sales | Posted On: September 18, 2020
5 Factors to Consider Before Purchasing a Metal Cutting Shear
Working in metal manufacturing uses a lot of machinery and metal shearing is one of them. Shearing, in fact, is often the first step in the process. Sizing your material into easy to handle and workable pieces. Metal shearing machines have been around in some form or another, for many years, and believe it or not, have not changed significantly throughout time.
The type of metal shearing machine you need will ultimately depend on what you need to use it for. They are rated by their ability to cut a certain thickness of steel to a certain length. However they vary in design and are equipped with different options for a varying degree of production requirements. s
What is Metal Shearing?
Metal shearing is a term used in the metal fabrication process. It is a process used to trim unwanted material or trim sheet metal. It cuts a straight line and is used when you need to size a workpiece or prepare blanks for later metal processing such as CNC Punching.
How Does Metal Shearing Work?
The shearing process involves the use of a machine or tool to cut through sheet metal. These tools are designed to cut with extreme precision. Shearing doesn’t require the use of heat nor does it produce waste in the form of chips, or stray bits of metal. This makes it a popular choice for manufacturers as full material utilization is common.
The machine used holds the sheet metal in place with a series of pressurized clamps called ‘holddowns’ and then the blade from the top of the machine moves down across a lower blade to make a cut. The top blade and lower blade are not placed at the same position, yet are offset ever so slightly to avoid collision yet provide the cleanest possible sheared edge. The slight difference is called the blade clearance.
Usually, the lower blade stays still (fixed) while the upper blade is pushed down with a great deal of force. The upper blade is fixed at a slight angle to the lower blade. This angle allows the cut to be made from one end to another, instead of at once. It reduces the amount of force required to cut the metal.The blades themselves come in different qualities of tool steels for hardness, wear resistance or shock absorption.
5 Factors to Consider Before Purchasing a Metal Cutting Shear
Metal cutting shears come with different abilities for different materials. They are also far more technological advances, so they make work faster and are more productive.
1) What Type of Metal is Being Sheared?
The type, thickness and consistency of the materials you are shearing will greatly affect the recommended choice of shear you purchase. If you're shearing thin gage metals or light aluminum you might be fine with an air or electrically operated shear, whereas if you're shearing ¾” Plate with plasma cut holes throughout you may really need to consider a good mechanical shear for the shock absorption capabilities.
It's not only important to consider the type of material but also the structure of that material as Tread Plate, Expanded Metals, Perforated metal etc all shear differently than flat material of an equal make.
2) What Kind of Quantity of Sheared Parts are needed?
The quantity of parts you need to shear is almost as important as the type of material you are shearing. While a basic and inexpensive machine might be fine for low-volume intermittent use, a more sophisticated or robust machine would be required for the production duties of, say a steel service center.
Not only do the machines have a wide variation of designs but they also can be equipped with a large number of options including conveyor/stackers to bring the sheared material onto a stack on a pallet for quick removal. Other options can include high speed hydraulics or more accurate Front gauging options.
3) Mechanical, Hydraulic, Electric, Air or Manually Operated Shearing Systems?
When you are selecting that shear one of the choices you have to make is the drive, or power systems behind it. Different drive systems are available to meet different demands of production and different cost structures.
- Manual Shears - Manually operated shears, sometimes called “stomp’ shears are for the lightest gage materials in the metal working market. Common in HVAC and roofing the Stomp HSear is a low production light machine primarily used on only 18 Gage and Thinner.
- Air Operated - Although pneumatics do not increase a shears capacity greatly, a pneumatically driven shear does reduce operator fatigue and allows for operating a metal shear at a quicker rate.
- Electric Shears - Electric shears adre shears that are driven simply by electrically methods without the advantages of flywheels to increase inertia, and thereby Tonnage/Force. These shears can work down into the 12-14 Gage range of steels and provide a quiet, smooth and very fast operation.
- Hydraulic Shears - Hydraulics are the next preferred method in driving the shearing blade. Used primarily in 14 Gage shears and thicker hydraulics are easy to produce, place and service and are far less expensive than thenir mechanically driven counterparts however they can lack the speed and durability of other systems.
- Mechanical Shears - If you're looking for the best production rated, longest lasting and shock absorbing design in shearing, it definitely is a Mechanical shear. Mechanical shears are simpler, quieter, faster, and run cooler and are designed to run all day, every day. These are the shears of choice for heavy duty production demands, like steel service centers.
4) Design: Guillotine or Swing Beam?
Once you have decided on the drive type of the shear, you need to know what design style may be better suited for your needs. There are two basic design types of shears on the market (regardless if they are mechanically or hydraulically driven) and they are the Guillotine style or Swing Beam style. A guillotine design in a shear refers to the upper blade being driven directly downward by the drive mechanism whereas a swing beam pivots the upper blade forcing down the blade by using the power of leverage.
Guillotine style provides for a more robust, yet expensive shearing system whereas the Swing Beam style uses smaller drive (hydraulics) components due to the advantage of leverage it employs in the design.
5) Rake Angle, Adjustable or Fixed?
Rake Angle is the angle the upper shearing blade is canted at in order to not engage too much material during the shearing process. The lower the rake angle the better quality the resulting sheared edge (including twist, bow and camber) yet the more robust and powerful the shear must be. Lower rake angles engage more blade in the material requiring more force (and thus more machine) to shear. Ideally the perfect shear would have a zero rake angle, however the forces required to shear even the thinnest of materials would be astronomical making the machine itself far too costly. Adjustable rake angles can allow for smaller shears to engage thicker materials but at a cost. As the rake angle increases the sheared edge quality, blade life and machine stress increase. Thin sheared strips can come off twisted or bowed as a result of heavy rake angles.
New and Used Shearing Options
At Southern Fabricating Machinery Sales we have many options available in new and used shearing systems including shears from manual to mechanical driving methods. More importantly, we know shearing, the metals, the machines and the results they produce. We can work with you and your team and explain what makes one shear option better for your application then another. Contact us today for more information on shears available from Southern Fab.
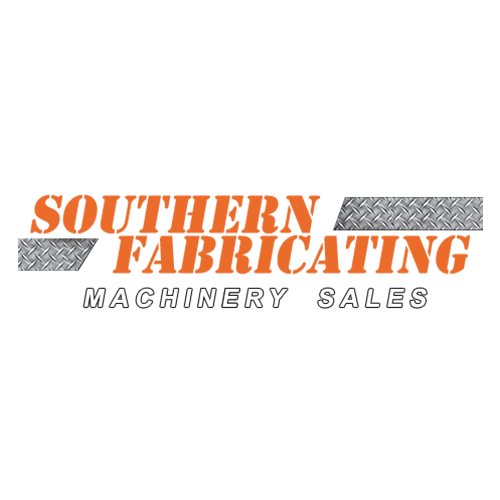