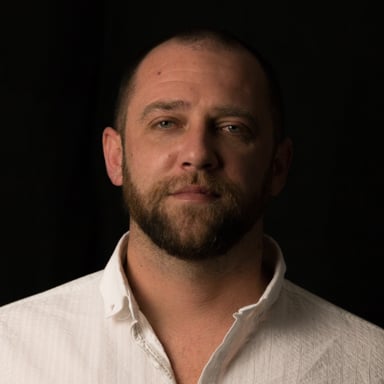
Posted By: Peter Yordanov | Posted On: November 29, 2021
Buying a Water Jet Cutter? The 6 Things You Need to Know
Waterjets can be used to cut virtually any material.
Pure water jets are capable of cutting soft materials like rubber, foam, or other gasket material quickly and accurately. Abrasive waterjets are able to cut virtually any material across a wide range of thicknesses. Virtually all metals are available, including hardened steel, stainless steel and aluminum as well as copper, titanium, and copper. Also other materials such as Non-tempered safety glass, including multilayer laminated safety glasses, composites, laminates, stone and ceramics in general
What number of parts would you like to be able to trim?
The setup time for waterjets machines with advanced control systems, is very short. Advanced control software allows you to program the cutting path for the part from a CAD drawing. Simply attach the material stock to a cutting table, and then enter the thickness and type of material into the control program. The control system takes care of the rest, and the part is ready for production in the first run. Waterjet is a great process for producing short-run parts and one-off production. Waterjets can also be used to mass produce parts using minimal waste thanks to modern nesting software.
Which size table are you looking for?
Waterjet cutting tables are now available in a variety of sizes. When choosing a table size, the two most important factors to consider are the size and type of part you need to make and the material that will be used. It is usually easier and more economical to choose a larger table that can handle all material stock sizes and future large parts.
What special features do I require?
Water cutting is attractive in certain applications because of its unique characteristics.
- Waterjets can cut without heat.
- Waterjets do not cause thermal distortion of complex or intricate parts.
- There is also no heat affected zone which could affect material properties. This means secondary machining processes such as thread-tapping can be easily performed on a waterjet-cut template.
- Waterjets have extremely low cutting forces and make very narrow cuts. Part designers can create complex parts with waterjet cutting that are virtually impossible to produce using traditional manufacturing processes.
- Waterjet cutting can easily create complex contours and shapes. Low waste costs are another benefit, especially when you're working with expensive materials.
What types of water and other waste factors should you consider?
Waterjets in the early days had a reputation for being noisy and filthy. A noisy water jet can cause noise and an abrasive waterjet could release a lot of abrasive particles into the air. Modern systems can eliminate these issues by simply removing a thin layer of water. The water layer reduces noise to a level below most machine tools. It also keeps the particles in water at bay. Abrasive waterjet machines can be used anywhere you would place a traditional machine tool. The part is free from noxious fumes and smoke, and it does not get contaminated by cutting oils.
A waterjet machine generates two waste streams:
Water containing small amounts of solids fines can be filtered and sent to a wastewater drain. You can send kerf waste and garnet waste to a landfill. If the material being cut contains poisonous materials, such as lead or beryllium - both waste streams must be cleaned in accordance with environmental regulations. The water can be recycled.
What is the cost of running and maintaining a waterjet?
When calculating the cost of operating the waterjet, there are many factors that must be considered. These include the number of cutting heads, defective parts, pump power and water supply costs, as well as the cost of abrasives. All these factors are considered and the water jet's handling will determine the running cost.
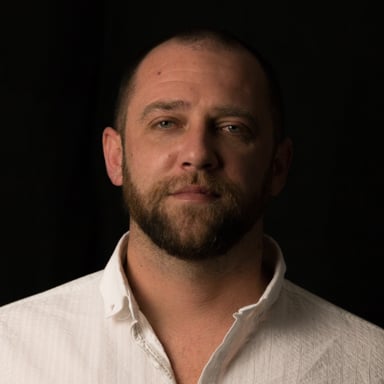